In the field of mechanical machining, tool selection and material classification are critical factors affecting processing efficiency, cost, and quality. Have you noticed the letter markings (such as P, M, K, N, S, H) on tool packaging? These markings are not just for aesthetics—they represent internationally recognized standards for material classification. For small and medium-sized enterprises (SMEs) with limited budgets, rational planning of tool usage is particularly important. Today, we will analyze these material classifications and share strategies for using the same tool across multiple materials to help you reduce costs and improve efficiency.
Overview of Material Classification and Corresponding Tools
What Are P, M, K, N, S, and H?
P Class (Steel): Includes carbon steel, alloy steel, cast steel, etc. Suitable for carbide tools and cermet tools.
M Class (Stainless Steel): Covers easy-to-machine stainless steels like 303 and 304, as well as difficult-to-machine materials such as 316 and duplex stainless steel.
K Class (Cast Iron): Includes gray cast iron, ductile iron, etc. Suitable for carbide tools.
N Class (Non-Ferrous Metals): Such as aluminum, copper, and their alloys. Best suited for sharp carbide tools and PCD (polycrystalline diamond) tools.
S Class (Superalloys): Includes Hastelloy, titanium alloys, and nickel-based superalloys. Requires specialized ultra-fine grain carbide tools.
H Class (High-Hardness Materials): Materials with hardness ≥45 HRC after heat treatment. Recommended tools include CBN (cubic boron nitride) or high-quality carbide tools.
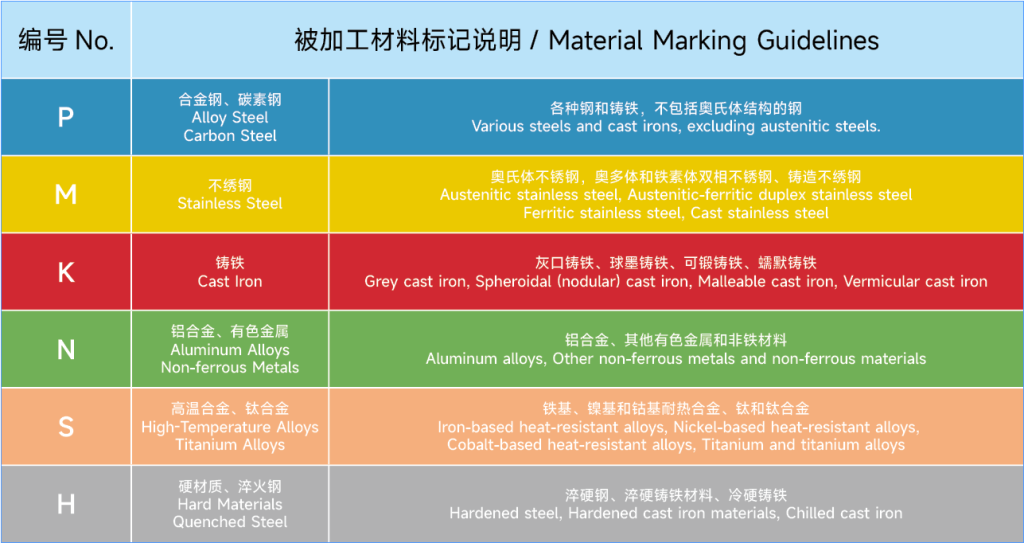
💡 Tip: While each material has its dedicated tools, SMEs can often share tools across certain materials to reduce inventory and procurement costs.
Material Classification and Tool Sharing Strategies
First Category—Carbon Steel, Alloy Steel, Cast Steel, and Ductile Iron
Characteristics: These materials are relatively easy to machine, with moderate hardness and stable cutting performance.
Tool Selection Recommendation: Carbide tools are the first choice; cermet tools are also suitable.
Sharing Strategy: These materials can share the same tools, especially drills, milling cutters, and turning tools. However, taps should preferably be made of high-speed steel (HSS) since carbide taps are brittle and prone to breakage.
💡 Case Study: A machining factory improved processing efficiency by 20% for carbon and alloy steels while reducing tool inventory costs by using universal carbide milling cutters.
Second Category—Easy-to-Machine Stainless Steels (303, 304, etc.)
Characteristics: These stainless steels are relatively soft but sticky, leading to built-up edge formation.
Tool Selection Recommendation: Tools with unequal pitch and irregular tooth spacing are recommended to reduce vibration and chip evacuation issues.
Sharing Strategy: For small batch processing, tools from the first category (steel) can be substituted. However, dedicated tools are still advised for mass production to extend tool life and improve precision.
💡 Technical Tip: For stainless steel machining, tools with large helix angles (45°–60°) enhance cutting sharpness and chip evacuation.
Third Category—Difficult-to-Machine Materials (316, Duplex Stainless Steel, Titanium Alloys, Nickel-Based Superalloys)
Characteristics: These materials have high hardness and toughness, generate excessive heat during cutting, and rapidly wear out tools.
Tool Selection Recommendation: Ultra-fine grain carbide tools or custom-coated tools are preferred.
Sharing Strategy: Tools for this category can also process second-category materials (e.g., 303, 304), enabling tool sharing. However, tool wear must be monitored. For nickel-based superalloys, custom tools are strongly recommended.
💡 Case Study: An aerospace parts manufacturer extended tool life by 30% and significantly improved surface quality by using dedicated superalloy tools.
Fourth Category—Non-Ferrous Metals (Aluminum, Copper, etc.)
Characteristics: These materials are soft and require sharp tools with smooth chip evacuation.
Tool Selection Recommendation: Aluminum-specific tools with sharper edges are ideal. Carbide and PCD tools are commonly used.
Sharing Strategy: Cast aluminum alloys (e.g., ADC12) contain high silicon content, making them harder to machine. Tools from the third category (difficult-to-cut materials) can be used as substitutes.
💡 Technical Tip: Polished tool surfaces reduce chip adhesion when machining aluminum.
Fifth Category—High-Hardness Materials (≥45 HRC)
Characteristics: These materials are extremely hard after heat treatment, demanding high wear resistance and edge toughness from tools.
Tool Selection Recommendation: Premium ultra-fine grain carbide or CBN tools are the best choices.
Sharing Strategy: Due to their unique properties, dedicated tools should be used exclusively for high-hardness materials.
💡 Important Note: Coatings play a crucial role in tool performance for high-hardness materials. ALTIN or TiAlN coatings enhance heat and wear resistance.
Gray Cast Iron
Characteristics: Gray cast iron contains impurities and produces powdery chips, making it relatively easy to machine.
Tool Selection Recommendation: Both carbide and HSS tools can be used.
Sharing Strategy: Straight-flute taps are recommended for gray cast iron to handle powdery chip evacuation.
💡 Case Study: An automotive parts manufacturer increased efficiency by 25% by using straight-flute taps to resolve chip clogging issues in gray cast iron machining.
Conclusion: Optimize Tool Usage for Cost Savings and Efficiency
By analyzing P, M, K, N, S, and H material classifications, we can clearly understand the different tool requirements for various materials. For SMEs, rational tool-sharing strategies not only reduce inventory costs but also enhance processing efficiency. Here are our key recommendations:
- Prioritize universal tools: For low-volume production, choose tools that can handle multiple materials.
- Focus on tool coatings: Coatings significantly impact tool performance, especially for high-hardness materials and superalloys.
- Regularly evaluate tool life: Track tool lifespan to optimize management and minimize wear.
- Make informed tool selections: Choose the most suitable tools based on material classification.
🎯 Action Suggestion: If you’re looking for high-efficiency tools for multi-material machining, Kontakt today! We provide expert tool selection advice and technical support.