The cutting depth of the Schaftfräser refers to the distance that the cutting tool cuts into the workpiece in the feed direction during the milling process. Specifically, depth of cutting can be divided into axial depth of cutting (AP or ADOC) and radial depth of cutting (AE or RDOC) :
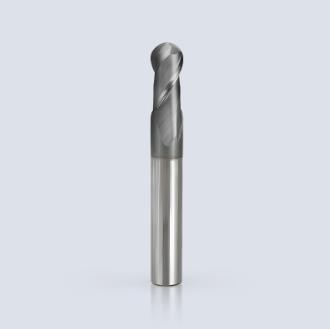
Depth of Axial cutting (AP or ADOC) :
Definition: The axial cutting depth is the length of the workpiece in the axis direction, that is, the depth of the cutting tool in the direction perpendicular to the surface of the workpiece.
Influencing factors: Axial cutting depth has significant effects on cutting force, cutting temperature, tool wear and machining surface quality. In general, the greater the cutting depth, the greater the cutting force, the higher the cutting temperature, the faster the tool wear, but the higher the processing efficiency.
Value range: The value range of the axial cutting depth should be considered according to the workpiece material, tool material, machine tool performance and other factors. In general, the cutting depth should not exceed the length of the main cutting edge of the blade, and it is necessary to ensure stability and safety during the processing.
Radial cutting depth (AE or RDOC) :
Definition: The radial cutting depth is the length of the tool that engages with the workpiece perpendicular to the axis of the workpiece, also known as the cutting width. It represents the contact width between the cutting edge of the tool and the workpiece in the radial direction (that is, the direction parallel to the surface of the workpiece) during the cutting process.
Influencing factors: The radial cutting depth has an important influence on chip load, processing power consumption, heat dissipation performance, etc. Larger radial cutting depths increase chip load and machining power consumption, but may also improve thermal performance.
Value range: The value range of radial cutting depth also needs to be considered according to the workpiece material, tool material, machine tool performance and other factors. Generally, the cutting width should not exceed the tool radius value to ensure the stability and safety of the cutting process.
In practical applications, the choice of cutting depth needs to be considered according to the specific processing requirements, workpiece materials, tool materials, machine tool performance and other factors. Reasonable setting of cutting depth can improve machining efficiency, ensure machining quality and extend tool life. For example, in roughing, the cutting depth can be appropriately increased to improve processing efficiency; In finishing, it is necessary to reduce the cutting depth to ensure the quality of the machined surface.