General-Purpose End Mills: Efficient Machining, Cost Reduction & Extended Tool Life
In today’s global manufacturing landscape where higher efficiency and lower costs are paramount, tool users frequently face challenges such as brand complexity, model confusion, management difficulties, high costs, and unpredictable tool life. Additionally, with the increasing diversity of machining materials, selecting cost-effective and highly versatile tools has become an industry pain point.
To address these issues, SDFTools introduces the new G-Series General-Purpose Solid Carbide End Mills, specifically designed for 10+ material groups, 5+ machining methods, 3+ cooling conditions, and 2+ part types. Covering 300+ application scenarios, these tools significantly simplify the tool selection process. Through comprehensive upgrades in tool materials, structural design, coating technology, and more, the overall performance and predictable tool life have been greatly enhanced.
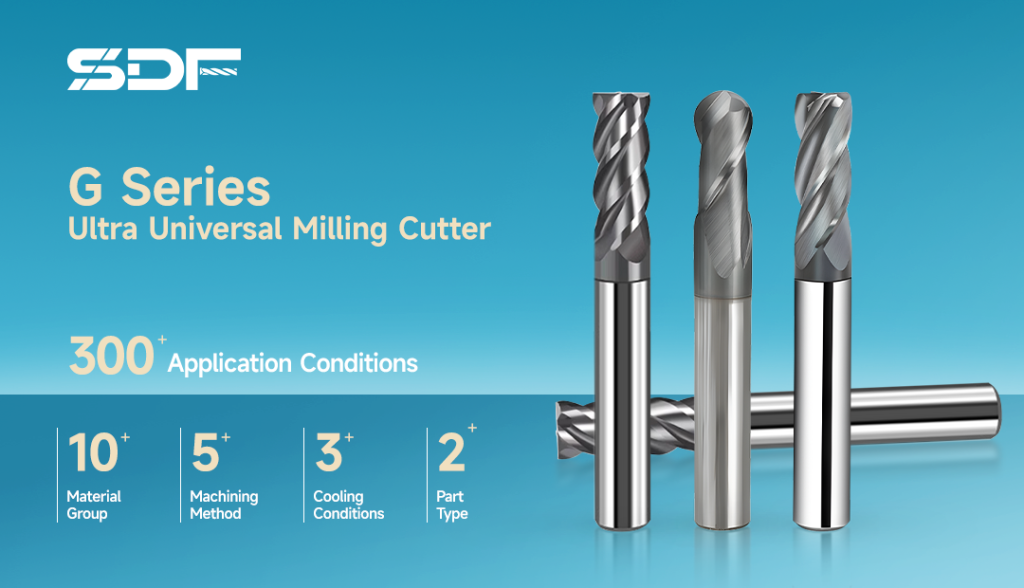
Why Choose SDFTools G-Series General-Purpose End Mills?
1. Exceptional Versatility – One Tool for Multiple Applications
Wide Material Compatibility:
Suitable for materials including P, M, K, N, H, etc., enabling efficient milling of carbon steel, alloy steel, tool steel, stainless steel, cast iron, and more. Capable of machining high-hardness steels up to 45 HRC.
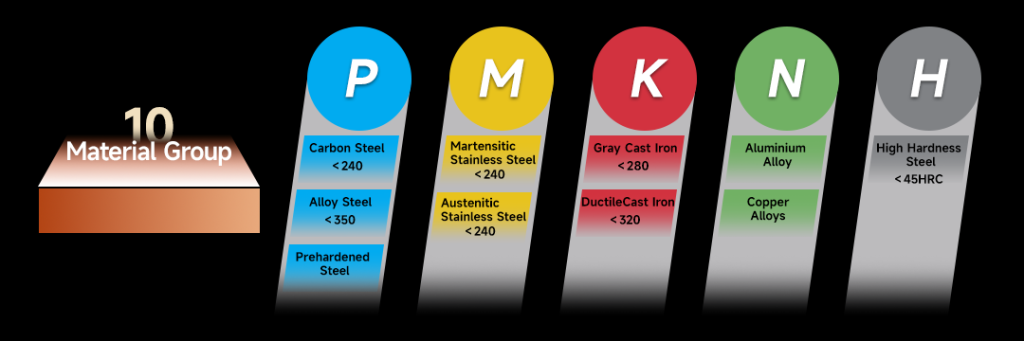
Full Process Coverage:
G-Series general-purpose tools support all CNC machining scenarios.
Ball Nose End Mills: Side milling, dynamic milling, face milling, contour milling, helical interpolation milling, slot milling, ramp milling.
Flat End Mills: Side milling, shoulder milling.
Ball End Mills: Profile milling.
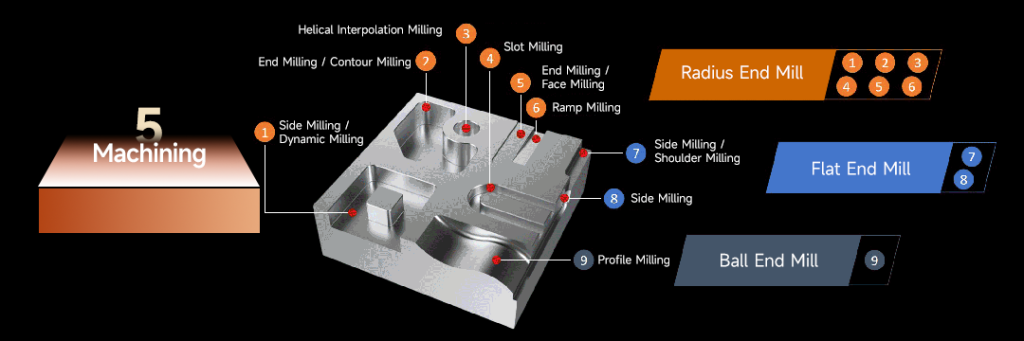
Adaptability to Various Cooling Methods:
G-Series tools deliver high efficiency under different cooling conditions, including air, water, and oil cooling.

Diverse Industry Applications:
Ideal for both high-efficiency machining of general parts and high-precision mold processing.
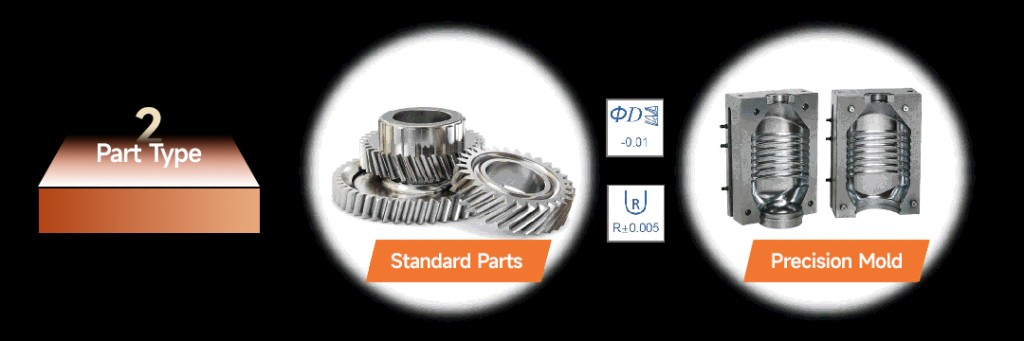
While achieving superior versatility, the G-Series also significantly improves overall performance and predictable tool life.
2. Four Core Technologies for Comprehensive Performance Upgrade
✅ Ultra-Fine Grain Substrate
High toughness + high hardness, suitable for both high and low cutting speeds.
Enhanced wear resistance due to special formulations and precision sintering processes.
✅ PVD Nano Multilayer Composite Coating
Improved wear resistance, adaptable to various cooling conditions.
Excellent high-temperature stability for better edge protection.
✅ Optimized Structural Design
Unequal tooth pitch + variable helix angles to reduce machining vibrations.
Reinforced core thickness for superior chipping resistance.
✅ Predictable Tool Life
Research on substrate, coating, and structural compatibility ensures controlled tool wear.
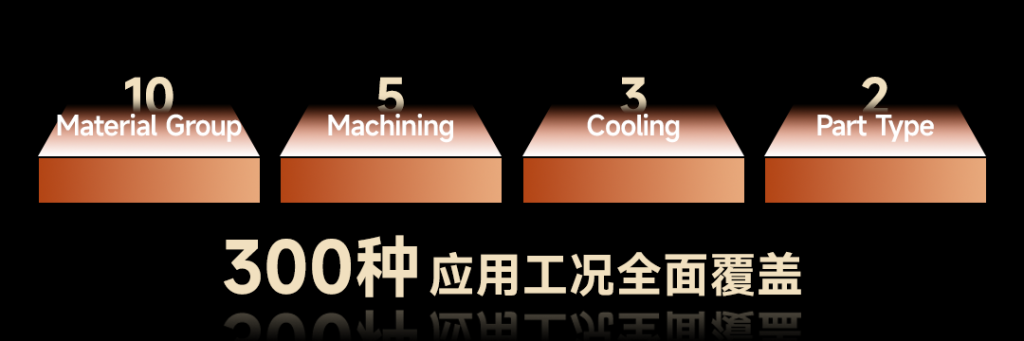
SDFTools G-Series Machining Case Studies
Case 1: The service life of G series flat-end milling cutters is increased by at least 13% ~ 50%
G Series | Brand A | Brand B | |
Time (min) | 275 | 244 | 183 |
Tool Model | Flat End Mill | ||
Workpiece Material | NAK 80 (HRC 30-35) | ||
Part Name/Application | General Industry | ||
Cutting Speed (Vc) | Vc=80m/min | ||
Feed per Tooth (Fz) | Fz=0.06mm/t | ||
Depth of Cut (Ap) | Ap=6mm | ||
Width of Cut (Ae) | Ae=1mm | ||
Milling Method | Side Milling | ||
Cooling | Dry Cutting | ||
Overhang | 20 | ||
Machining Equipment | Mikron MILL E 500U |
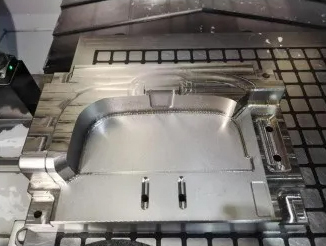
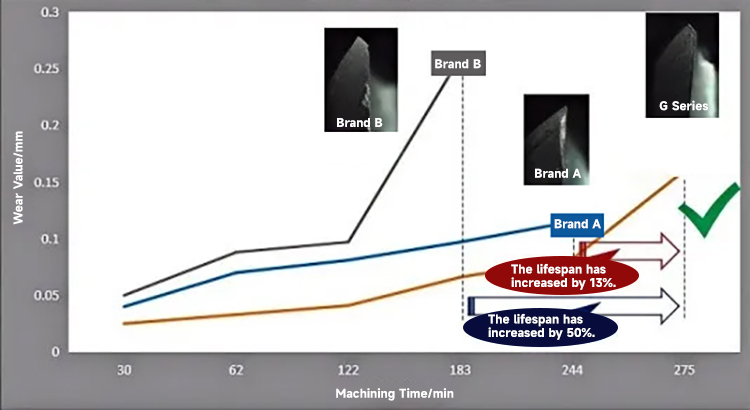
Case 2: The wear value of G-series arc milling cutters is reduced by 15% – 53%
G Series | Brand A | Brand B | |
Milling Length (m) | 200 | 200 | 183 |
Tool Model | Radius End Mill | ||
Workpiece Material | 304 Stainless Steel | ||
Part Name/Application | General Industry | ||
Cutting Speed (Vc) | Vc=80m/min | ||
Feed per Tooth (Fz) | Fz=0.08mm/t | ||
Depth of Cut (Ap) | Ap=0.5mm | ||
Width of Cut (Ae) | Ae=4mm | ||
Milling Method | Frame Face Milling | ||
Cooling | Water-Soluble Emulsion | ||
Overhang | 22 | ||
Machining Equipment | 50 HURCO |
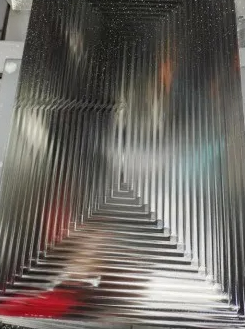
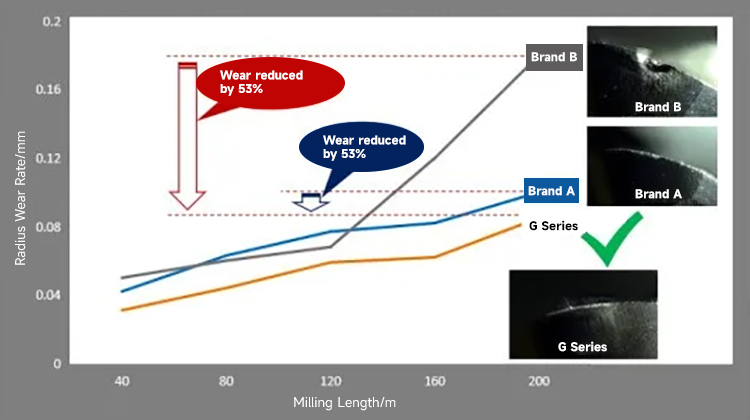
Case 3: The wear value of G-series ball nose end mills is reduced by more than 40%
G Series | Brand A | Brand B | |
Milling Length (m) | 356 | 356 | 356 |
Tool Model | Ball End Mill | ||
Workpiece Material | 718H(HRC37-40) | ||
Part Name/Application | Mold Industry | ||
Cutting Speed (Vc) | Vc=280m/min | ||
Feed per Tooth (Fz) | Fz=0.1mm/t | ||
Depth of Cut (Ap) | Ap=0.8mm | ||
Width of Cut (Ae) | Ae=0.8mm | ||
Milling Method | Profile Milling | ||
Cooling | Dry Cutting | ||
Overhang | 15 | ||
Machining Equipment | Mikron MILLE P800 U D |

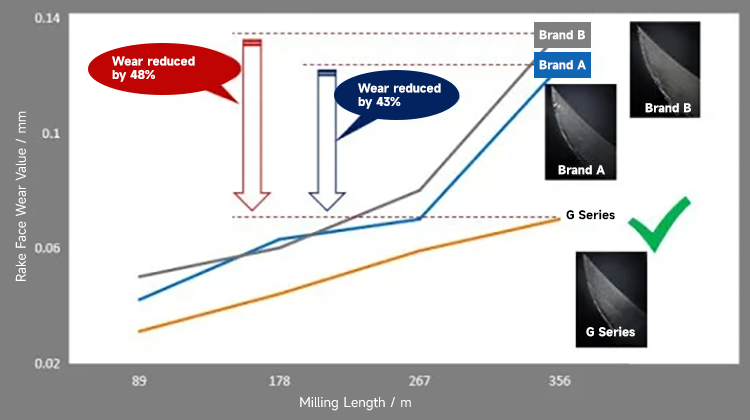
About SDFTools – Specialized in High-Performance End Mill Manufacturing
Since 2006, SDFTools has been committed to the R&D and production of high-precision, high-performance end mills. With customer satisfaction as our core focus, we adhere to the ISO 9001:2000 quality management system to ensure every product undergoes rigorous testing, meeting and exceeding customer expectations.
🔹 Our Commitment:
✔ Higher versatility – Fewer tool changes
✔ Longer tool life – Lower machining costs
✔ More stable performance – Improved productivity
Contact us today to learn more about SDFTools G-Series End Mills and optimize your machining process!
网站:www.sdftools.com
邮箱:sdfgroup@sdftools.com