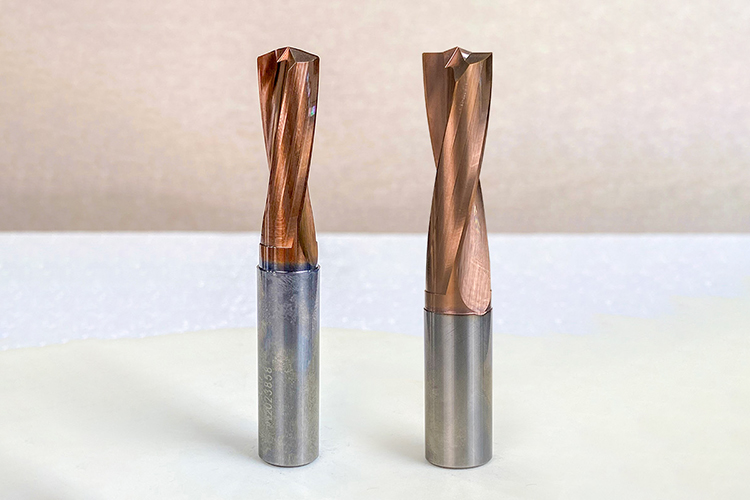
In heavy industries such as mining and tunnel engineering, low air pressure drill tools are critical consumables, directly impacting operational efficiency and cost control. However, with the widespread adoption of high-strength alloy steels (e.g., 42CrMo, 45CrNiMoV), traditional machining technologies have revealed significant limitations:
- Hardness Challenges: Materials with surface hardness of HRC 38-48 cause rapid tool wear and reduced efficiency.
- Precision Deficiencies: Issues like hole roundness deviation and diameter fluctuation lead to assembly errors.
- High Costs: Frequent tool replacements and regrinding downtime escalate production costs.
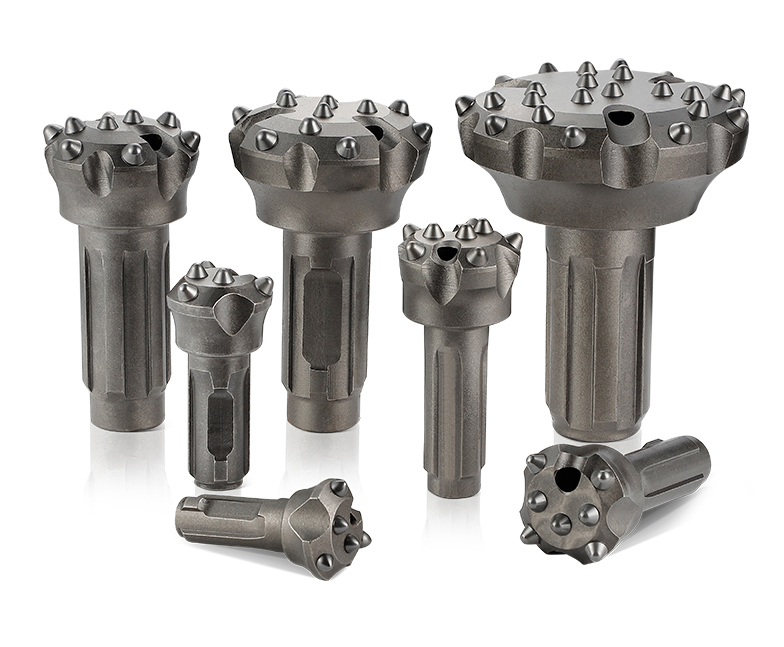
How can these barriers be overcome? SDFTools LongForce Drill Series offers an efficient and sustainable solution through advancements in materials science and process innovation.
Technical Analysis: Core Innovations of the LongForce Drill Series
1. Nano-Composite Coating Technology: The “Invisible Armor” for Extended Tool Life
To address high-hardness material cutting challenges, SDFTools employs nano-composite coatings (e.g., AlCrN/TiSiN), enhancing surface hardness and thermal resistance. Lab tests show that when machining HRC 45 steel continuously, coated tools exhibit a 50% longer lifespan and 15% lower cutting temperatures compared to conventional tools, minimizing thermal deformation risks.
2. Dual-Drill Tip Design: Flexibility for Complex Applications
- Tapered Tip: Features self-centering functionality for deep-hole drilling, automatically correcting drill paths to reduce deflection errors.
- Flat Tip: Optimized edge geometry ensures hole bottom flatness ≤0.01mm, meeting high-precision assembly requirements.
3. Intelligent Cooling Systems: Balancing Efficiency and Quality
Dual cooling modes—internal (high-pressure coolant直达刀尖) and external (spray cooling)—resolve heat dissipation challenges in deep-hole machining. Field tests by a tunnel equipment manufacturer demonstrated a 20% improvement in hole consistency and 30% extended tool life when using internal cooling.
Case Study: Validating Efficiency from Theory to Practice
Background: A mining machinery manufacturer required batch processing of 42CrMo drill head齿孔 (Φ25mm diameter, 80mm depth, HRC 42). Previously, frequent tool chipping and dimensional inaccuracies caused delivery delays.
Solution:
- Adopted SDFTools flat-tip drills (135° main edge angle + R1.0mm tip) with internal cooling.
- Implemented single-pass forming to reduce tool changes.
- Introduced periodic regrinding management (every 200 holes).
Results:
- Tool lifespan increased from 150 to 600 holes.
- Hole diameter tolerance stabilized within ±0.015mm; roundness error ≤0.008mm.
- Total machining costs reduced by 35%, saving over ¥120,000 annually on tool procurement.
Future Outlook: Driving Sustainable Industry Development
With the global push toward “dual carbon” goals, demand for high-efficiency, low-consumption machining technologies is rising. The LongForce Drill Series not only addresses current industry pain points but also pioneers advancements in:
- Digital Management: Developing tool life prediction systems integrated with IoT for real-time wear monitoring.
- Green Processes: Optimizing coating compositions to reduce rare metal usage and enhance eco-friendliness.
- Customization: Providing dynamic edge design support based on client-specific materials and parameters.
Conclusion: Redefining Machining Boundaries with Technology
The challenges in low air pressure drill tool processing stem from the synergy of materials, processes, and tools. Through scientific design and evidence-driven innovation, SDFTools LongForce Drill Series delivers a replicable path for efficiency gains. We look forward to collaborating with partners worldwide to advance “hardcore manufacturing” with precision engineering and sustainability.