The Challenges of Stainless Steel Machining: Why is it So “Stubborn”?
Mastering Stainless Steel Machining: Techniques, Tools, and Strategies – The Right Tools Make All the Difference
Stainless steel is widely used in industries such as aerospace, medical equipment, and food processing due to its excellent corrosion resistance, high strength, and aesthetic appeal. However, these advantages also bring significant machining difficulties:
- High Hardness and Toughness: Stainless steel is harder than ordinary steel and has extremely high toughness, resulting in large cutting forces and rapid tool wear.
- Low Thermal Conductivity: Heat generated during cutting is difficult to dissipate, easily causing workpiece surface hardening or tool overheating damage.
- Work Hardening Tendency: The material surface rapidly hardens during cutting, increasing subsequent machining difficulty.
- Long Chip Problem: Stainless steel chips have strong adhesion and are difficult to break, potentially causing tool entanglement or even breakage.
Facing these challenges, only through proper tool selection, optimized process parameters, and efficient cooling strategies can efficient and stable machining results be achieved.
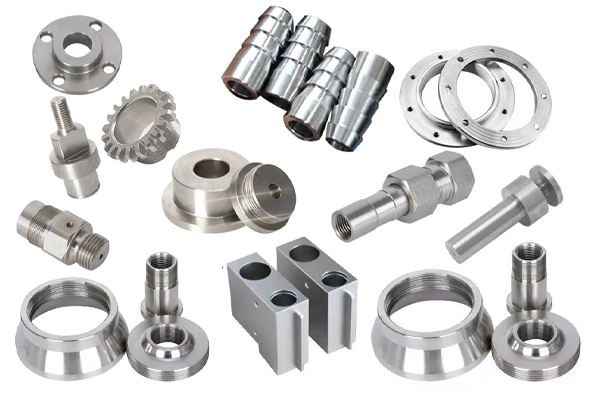
4 Core Strategies to Overcome Stainless Steel Machining Challenges
1. Drilling: Comprehensive Optimization from Tools to Operational Details
Drilling is a critical and often problematic aspect of stainless steel machining. Here are the best practices we’ve summarized for you:
① Tool Selection: Prioritize Internal Coolant Carbide Drills
Internal Coolant Carbide Drills: Internal cooling channels directly deliver cutting fluid to the tool tip, rapidly cooling and effectively removing chips, making them the preferred choice for stainless steel drilling.
External Coolant Carbide Drills: If the machine does not support internal coolant, high-pressure external coolant drills are a reliable alternative.
Powder Metallurgy Drills: Designed for high-strength materials, suitable for complex geometric shape machining requirements.
HSS Twist Drills: Recommended only for emergency use due to their lower wear resistance and shorter lifespan, unsuitable for prolonged machining.
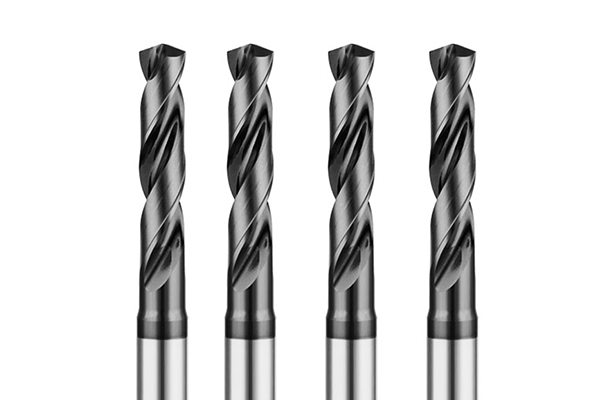
② Operational Techniques: Avoid Common Mistakes
Low-speed start, fast feed: Avoid drilling at high speed with low feed rates, as this causes heat accumulation and accelerates surface hardening.
Timely chip removal: Stainless steel chips are long and sticky. If not removed promptly, they may cause tool jamming or breakage. Internal coolant drills significantly improve this issue.
Control drilling depth: Step drilling (gradually increasing depth) reduces tool stress and extends service life.
Real Case Study
A customer frequently experienced tool breakage when drilling 316L stainless steel without using internal coolant drills. After switching to internal coolant carbide drills, machining efficiency increased by 40%, and tool life extended by more than 2 times.
2. Stainless Steel Milling: Combine Roughing and Finishing, Skillfully Use Techniques and Tools
Milling is one of the most common processes in stainless steel machining, but its complexity should not be underestimated. The main difficulties lie in its high toughness, tendency to work harden, and poor thermal conductivity. Cutting processes easily generate built-up edges, accelerating tool wear; work hardening significantly shortens tool life; cutting heat is difficult to dissipate, causing workpiece deformation; and stainless steel’s high viscosity makes chip removal difficult, leading to surface scratches. These characteristics impose higher demands on tool materials, geometric parameters, cutting parameters, and cooling methods, requiring specially optimized processes to ensure machining efficiency and quality. Below are specific recommendations for roughing and finishing stainless steel:
① Roughing: Prefer Fine-tooth Wavy-edge Milling Cutters
Advantages of Fine-tooth Wavy-edge Milling Cutters:
Low cutting resistance: Reduces friction between the tool and workpiece, minimizing heat accumulation.
High feed rates: Improves machining efficiency and shortens production cycles.
Short chip generation: Especially in slot milling, the fine-tooth design produces shorter chips for easy removal, avoiding secondary cutting damage.
② Dynamic Milling Technology: The Secret to Smooth Cutting
Dynamic milling is an advanced machining method that utilizes the tool’s side cutting capability, combined with large helix angles and unequal division designs, to achieve efficient chip removal and stable cutting. This technique is particularly suitable for deep cavities and complex curved surfaces in stainless steel.
③ Finishing: Focus on Surface Finish
Use high-precision coated milling cutters (such as TiAlN-coated) to significantly improve workpiece surface finish and machining efficiency. TiAlN coating has excellent high-temperature and wear resistance, maintaining tool sharpness under high-speed cutting conditions, effectively reducing cutting forces and friction heat, thereby avoiding burrs and scratches on the workpiece surface. Additionally, this coating extends tool life and reduces machining costs. Combined with reasonable cutting parameters (such as appropriate feed rates, cutting depths, and coolant use), machining effects can be further optimized to ensure mirror-like surface smoothness, meeting the stringent requirements of high-precision components.
Control cutting parameters to avoid excessive feed rates affecting surface quality. When machining stainless steel, it is recommended to use lower cutting speeds (turning 50-120 m/min, milling 30-80 m/min) to reduce heat accumulation and tool wear, while selecting medium feed rates (roughing 0.1-0.3 mm/rev, finishing 0.05-0.1 mm/rev) to avoid work hardening or surface burrs; cutting depths should be reasonably allocated (roughing 2-5 mm, finishing 0.1-0.5 mm) to balance cutting forces and machining efficiency. Additionally, prioritize ultra-fine grain carbide or coated tools (such as TiAlN), and use high-pressure coolant or minimum quantity lubrication (with extreme pressure additives) to lower cutting temperatures and improve chip removal. The key is to optimize tool geometric parameters (such as rake angles of 8°-15° and relief angles of 6°-10°) and process system rigidity to address stainless steel’s poor thermal conductivity, sticky and tough chips, and work hardening, thereby balancing machining quality and tool life.
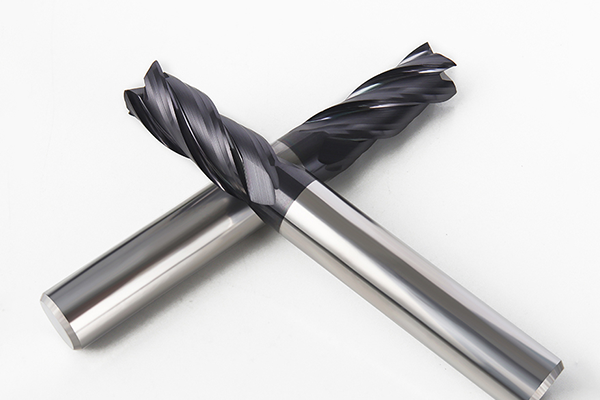
3. Stainless Steel Machining Tool Coatings and Materials: Details Determine Success or Failure
Tool selection for stainless steel machining directly impacts efficiency and costs. Here are some key points:
TiAlN-coated Tools: High-temperature and wear resistance, especially suitable for high-heat environments in stainless steel machining.
Use Stainless Steel-specific Tools: Different material types have varying tool requirements. Stainless steel tools should never be mixed with other material tools to avoid accelerated wear.
Cost-benefit Balance: Although high-quality tools are more expensive, their superior durability and machining effects often yield higher overall returns.
4. Stainless Steel Machining Cooling Strategies: A Dual Revolution in Cooling and Lubrication
Cooling plays a crucial role in stainless steel machining. Here are several effective cooling methods:
Oil Mist + Cold Air Cooling: Compared to traditional water-based coolants, this combination more efficiently reduces cutting zone temperatures while providing lubrication, minimizing tool wear.
High-pressure Cooling: Suitable for deep hole or complex shape machining, ensuring rapid chip removal and tool cooling.
Case Verification: A customer machining duplex stainless steel extended tool life by 30% and significantly improved surface finish after switching to oil mist + cold air cooling.
Stainless Steel Machining Tool Selection, Our Advantages: One-stop Stainless Steel Machining Solutions for You
Whether you face tool wear, low machining efficiency, or subpar surface quality, we can provide tailored stainless steel machining solutions:
✅ Professional Tool Supply: From internal coolant drills to TiAlN-coated milling cutters, covering all stainless steel machining needs.
✅ Technical Support Team: Free process parameter debugging and cooling solution design to optimize your machining workflow.
✅ Global Rapid Delivery: 72-hour shipping, supporting major markets like Europe, America, and Southeast Asia, ensuring your production schedule remains uninterrupted.
Call to Action: Solve Your Stainless Steel Machining Challenges Now!
If you’re struggling with any issues in stainless steel machining, don’t hesitate—contact us immediately! We offer:
Free Technical Consultation: One-on-one analysis of your machining pain points with targeted recommendations.
Sample Machining Service: Verify solution effectiveness before ordering, ensuring worry-free procurement.
Click the button below to get your exclusive stainless steel machining solution! Consult Now →
#StainlessSteelMachiningSecrets #CNCToolSelection #Difficult-to-MachineMaterialSolutions #StainlessSteelMachining #CNCMillingTechniques #CarbideDrills #TiAlNCoatedTools