A broca escalonada de acabamento personalizado melhora a qualidade e a eficiência no fabrico de dispositivos médicos de precisão
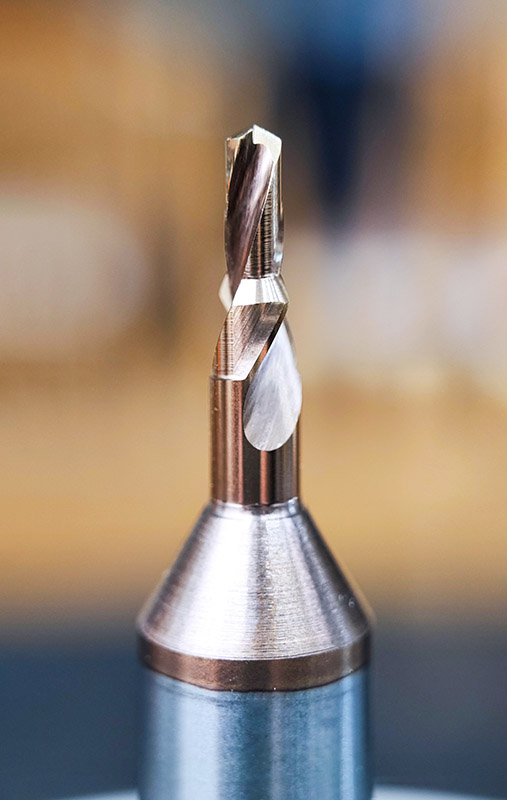
Customer Background
A high-end medical device manufacturer needed to machine Φ2.5mm and Φ4mm dual-stage precision holes in 4Cr13 martensitic stainless steel workpieces during the production of precision orthopedic surgical instruments. The hole depth ratio reached 1:3, with strict tolerance requirements of ±0.005mm. Traditional tools faced challenges due to material hardness and brittleness, leading to high chipping rates, insufficient machining efficiency, and a pass rate of only 65%.
Technical Challenges
- Material Properties: 4Cr stainless steel has a hardness of HRC48-52, making it prone to adhesion and vibration during cutting.
- Geometric Structure: Stress concentration in the transition zone between two stages often leads to tool breakage.
- Precision Assurance: A 5.9mm deep hole requires straightness ≤0.01mm and surface roughness Ra0.4μm.
Customized Solution
▶ Gradient Composite Coating Technology
- Utilizes AlCrN/TiSiN nano-multilayer coating (3.2μm thick), reducing the friction coefficient by 40%.
- Edge rounding process (R0.03mm) to suppress micro-chipping.
▶ Innovative Chip Evacuation Design
- 10° helix angle + variable lead spiral flute increases chip evacuation speed by 35%.
- R0.15mm stress relief structure at the transition between two stages.
▶ Ultra-precision Manufacturing System
- Swiss TORNOS CNC lathe for processing, with radial runout ≤0.003mm.
- 100% inspection of hole diameter tolerances using a coordinate measuring machine (CMM).
Implementation Results
- Machining Efficiency: Single-edge life increased from 80 to 420 pieces, reducing tool change frequency by 81%.
- Quality Breakthrough: Hole diameter CPK value improved from 0.89 to 1.67, reducing defect rate to 1.2%.
- Overall Cost: Reduced single-piece machining cost by 54%, saving RMB 280,000 annually on tool costs.
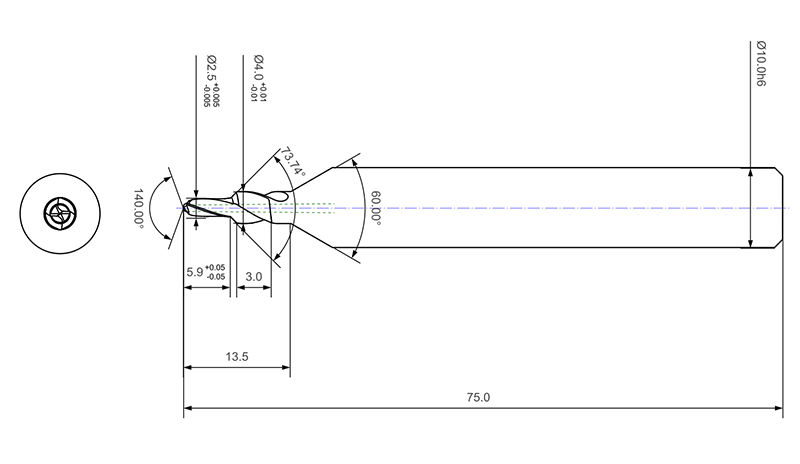
Customer Testimonial
“Your customized tool solution has completely resolved our machining bottlenecks. Currently, we are stably delivering 120,000 precision components per month, helping us secure CE certification orders from the EU.”
Technology Extension Value
This solution has been successfully applied to aerospace precision bushings (17-4PH stainless steel) and automotive fuel injection valves (440C stainless steel), demonstrating the industry-wide applicability of the technology.
About SDFTools
As an innovator in the field of precision tool customization, SDFTools always focuses on customer pain points, providing full-chain solutions from process analysis, tool design to production optimization. Whether in aerospace, automotive manufacturing, or medical device fields, we empower precision manufacturing with technology, helping you gain a competitive edge.
For breakthroughs in precision manufacturing of difficult-to-machine materials, please contact us for customized tool solutions. Our professional technical team provides 24/7 support.
Technology-driven, precision-focused—SDFTools, your efficient machining partner.
