In the aerospace manufacturing industry, machining aluminum alloy components has always presented unique challenges—how to achieve high-efficiency cutting while ensuring minimal deformation of thin-walled structures and perfect surface quality. Through years of practical validation, the 45° helix angle end mill has become the gold standard in this field. This article delves into why this specially designed end mill is the preferred choice for machining aerospace aluminum alloys and how it helps manufacturers improve productivity and reduce costs.
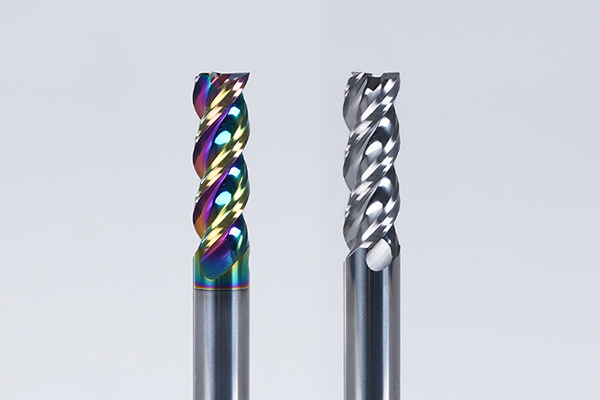
Unique Challenges in Machining Aerospace Aluminum Alloys
Aerospace aluminum alloys (such as the 7050 and 7075 series) are ideal materials for aircraft structural components due to their lightweight and high strength. However, machining these materials poses several critical challenges:
- Thin-wall deformation: Modern aircraft designs prioritize weight reduction, often resulting in wall thicknesses of less than 1mm, making deformation during machining highly likely.
- High material removal rates: The material removal rate for monolithic structural components can reach 70–95%, requiring extremely high metal cutting efficiency.
- Surface quality: Aerospace components demand Class 1 or 2 precision, with stringent surface roughness requirements.
- Thermal deformation control: Preventing heat accumulation during machining to avoid dimensional deviations. Traditional end mills often struggle with these challenges, but the introduction of the 45° helix angle design has revolutionized the landscape.
Five Core Advantages of the 45° Helix Angle End Mill
- Optimized Cutting Force Distribution The 45° helix angle design perfectly balances three cutting force components:
- Axial force: Approximately 40% higher than 30° helix angle tools.
- Radial force: 25–30% lower than 30° helix angle tools.
- Tangential force: Remains stable. This unique force distribution offers two key benefits:
- Reduced vibration: Lower radial force significantly minimizes chatter risk in thin-walled workpieces.
- Stable cutting: Balanced force distribution ensures smoother machining. “When machining 0.8mm thin-wall aluminum alloy, the 45° helix angle end mill controls deformation within 0.05mm, whereas traditional end mills typically cause 0.15–0.2mm deformation.” — Technical report from an aerospace manufacturer.
- Exceptional Chip Evacuation Performance The high helix angle design creates an ideal chip evacuation path:
- Chip flow direction: Naturally ejected upward along the flute.
- Chip pocket capacity: Approximately 35% larger than 30° helix angle tools.
- Chip shape: Forms short spiral chips, preventing entanglement. This advantage is particularly evident in deep cavity machining (depth > 3× diameter), reducing tool breakage risks caused by chip clogging.
- Higher Tolerance for Cutting Parameters Comparative test data:
Parameter | 30° Helix Angle | 45° Helix Angle | Improvement |
---|---|---|---|
Cutting speed (m/min) | 2000 | 2500–3000 | 25–50% |
Feed per tooth (mm/z) | 0.12 | 0.15–0.2 | 25–67% |
Axial depth of cut (mm) | 5–8 | 8–12 | 60% |
This performance enhancement directly translates to a 30–50% reduction in machining time.
- Extended Tool Life The 45° helix angle design excels in:
- Heat distribution: Cutting heat is dispersed more evenly, avoiding localized overheating.
- Wear pattern: Uniform flank wear with no abnormal damage.
- Regrinding cycles: Can be reground 6–8 times (compared to 4–5 times for 30° helix angle tools). Practical cases show that when continuously machining aerospace aluminum alloy frames, the 45° helix angle end mill can achieve a lifespan of 120–150 minutes, extending tool life by over 50% compared to conventional tools.
- Superior Surface Quality The high helix angle delivers:
- Smooth transitions: Progressive cutting edge engagement reduces vibration marks.
- Surface roughness: Achieves Ra 0.4–0.8μm.
- Dimensional accuracy: Consistently maintains IT7–IT8 grade. This is critical for aircraft structural components with strict requirements, reducing the need for post-machining manual finishing.
The Critical Role of Carbide Material
The 45° helix angle design must be paired with high-quality carbide substrates to maximize performance:
- Substrate selection:
- Fine-grained WC-Co (grain size 0.5–0.8μm).
- Cobalt content: 8–10% for enhanced toughness.
- Additives: TaC/NbC to improve red hardness.
- Coating technology:
- TiAlN: Excellent heat resistance, suitable for high-speed cutting.
- DLC: Reduces aluminum adhesion tendencies.
- Nano-multilayer: Enhances coating toughness.
- Recommended substrate/coating combinations:
- General aluminum alloys: K20/K30 + TiAlN.
- High-silicon aluminum alloys: K10 + DLCMX.
- Composite materials: K40 + nano-multilayer.
Practical Application Cases
Case 1: Aircraft Wing Spar Machining
- Material: 7075-T651.
- Tool: Ø16mm 45° helix angle end mill.
- Parameters: S = 18,000 rpm, F = 3,000 mm/min, ap = 10mm.
- Results: Machining time reduced by 40%, surface quality improved by one grade.
Case 2: Aerospace Connector Component
- Material: 2024-T3.
- Issue: Thin-wall (1.2mm) deformation.
- Solution: Switched to a 45° helix angle end mill.
- Outcome: Deformation reduced from 0.3mm to 0.08mm.
Guidelines for Proper Use of 45° Helix Angle End Mills
Mounting Tips:
- Keep overhang within 3×D.
- Use hydraulic or shrink-fit tool holders.
- Ensure radial runout < 0.01mm.
Cutting Parameter Recommendations:
Diameter (mm) | Speed (rpm) | Feed (mm/min) | Depth of Cut (mm) |
---|---|---|---|
6 | 20,000–25,000 | 1,200–1,800 | 5–8 |
10 | 15,000–18,000 | 2,000–3,000 | 8–12 |
16 | 10,000–12,000 | 3,000–4,500 | 12–20 |
20 | 8,000–10,000 | 4,000–6,000 | 15–25 |
Maintenance Recommendations:
- Inspect cutting edges every 60–90 minutes of machining.
- Use dedicated aluminum cutting fluid (dry cutting not recommended).
- Avoid edge collisions during storage.
Frequently Asked Questions
Q: Can 45° helix angle end mills be used for other materials? A: While optimized for aluminum alloys, they can also be used for soft materials like magnesium alloys and plastics. They are not recommended for steel or titanium alloys.
Q: How do they compare to variable helix angle designs? A: The 45° constant helix angle offers superior stability, while variable helix angles (e.g., 35–45°) provide slightly better vibration damping but at a higher cost.
Q: How to determine if the helix angle is suitable? A: Consider a 45° helix angle if you encounter excessive thin-wall deformation, surface chatter marks, poor chip evacuation, or insufficient tool life.
Conclusion
The 45° helix angle end mill, with its unique geometric design, perfectly addresses the core challenges of machining aerospace aluminum alloys. It demonstrates significant advantages in efficiency, quality, and cost control. As the aerospace industry continues to demand higher efficiency and precision in machining, this tool will remain indispensable.
We offer a comprehensive range of 45° helix angle end mill solutions, from standard products to custom designs, to meet all aerospace aluminum alloy machining needs. Contact our technical team for personalized recommendations.
Are you facing challenges in machining aerospace aluminum alloys? Consult our expert team today for a tailored tooling solution!
Contact Us
If you’re looking to enhance your machining efficiency, reduce costs, or tackle challenging materials, our team of experts is here to help. Whether you need tailored recommendations for your specific application or advanced tooling solutions, we’ve got you covered.
Email Us: sdfgroup@sdftools.com
Connect on LinkedIn: Your Company LinkedIn Profile
Let’s collaborate to optimize your cutting processes and achieve superior results!