In CNC machining, threading may seem routine, but it actually demands extremely high efficiency, precision, and process flexibility. For a long time, tapping has been the mainstream method. However, as part geometries become increasingly complex and material performance continues to improve, more and more companies are realizing—
“Tapping is no longer the only option, and often not the best one.”
Instead, thread milling , a more modern, flexible, and adaptable machining method, is taking the lead. It not only overcomes the limitations of traditional processes but also demonstrates higher productivity and greater stability in practical applications.
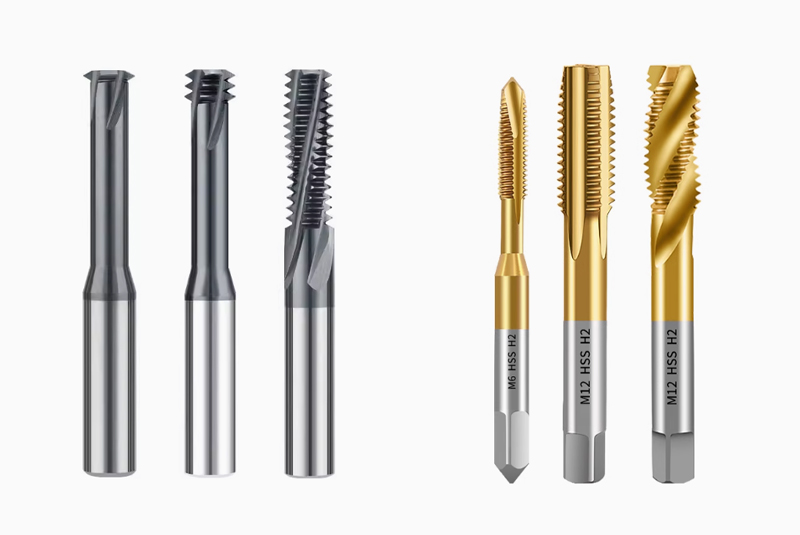
🧩 1. Limitations of Traditional Tapping
Although tapping is simple to operate and has low equipment requirements, it exposes several pain points when used on modern machining centers:
❌ 1. Single Direction of Machining
- Can only tap from top to bottom; unable to perform side or inverted machining;
- Ineffective for non-standard angles or holes with limited space.
❌ 2. Poor Tool Rigidity, Prone to Breakage
- Especially in small-diameter, deep blind holes, or hard-to-cut materials, taps are highly prone to breaking;
- Handling broken taps is complicated and disrupts overall production flow.
❌ 3. Chip Evacuation Difficulties
- Chips accumulate inside the hole, causing secondary cutting or galling;
- Frequent tool retraction for chip removal reduces efficiency.
❌ 4. Difficulty in Precision Control
- Tap wear directly affects thread dimensions;
- No support for programming adjustments, making it hard to maintain consistency.
🛠️ 2. Advantages of Thread Milling: Why Is It the Ideal Choice for Modern Machining Centers?
✅ 1. Flexible Machining, Highly Adaptable
- Supports clockwise/counterclockwise helical interpolation , enabling both left-hand and right-hand threading;
- Programmable arbitrary-angle entry , meeting the needs of irregular parts;
- A single tool can handle multiple thread sizes without requiring tool changes.
✅ 2. Layered Cutting, Even Force Distribution
- Small cutting increments distribute forces more evenly;
- Reduces vibration and heat buildup, enhancing machining stability;
- Particularly suited for high-strength materials like stainless steel and titanium alloys.
✅ 3. Smooth Chip Evacuation, Reduced Intervention
- The tool continuously rotates and exits during milling, aiding chip evacuation;
- Combined with high-pressure coolant or air-blow systems, almost no built-up edge forms.
✅ 4. Controllable Precision, Stable Quality
- CNC programs can adjust diameter, pitch, depth, and other parameters;
- Even with tool wear, compensation ensures consistent thread quality;
- High repeatability, ideal for automated production lines.
✅ 5. Longer Tool Life, Lower Overall Costs
- Unlike disposable taps, thread mills can be reground and reused multiple times;
- A single tool can handle different thread sizes, reducing inventory pressure;
- In mass production, per-piece costs are significantly lower than traditional tapping.
💡 Real-World Case Study: SDFTools Boosts Customer Efficiency
An automotive parts manufacturer once faced a typical challenge: M10×1.5 blind hole threads, 40mm deep, on cast iron housings . Originally using high-speed steel taps, they had to replace taps 8 times per shift on average, with a scrap rate of up to 7% due to poor chip evacuation.
We recommended a solid carbide thread mill with through-coolant , paired with optimized cutting paths and cooling solutions. The results were impressive:
Metric | Original Tap Solution | Thread Milling Solution |
---|---|---|
Tool Life (per edge) | ~50 pieces | ≥1,200 pieces |
Processing Time per Piece | ~12 seconds | ~15 seconds |
Scrap Rate | ~7% | <0.3% |
Overall Cost per Piece | ¥6.8 | ¥1.2 |
📌 Outcome : Per-piece cost decreased by 82% , tool change frequency was drastically reduced, and production line stability improved significantly.
📈 Industry-Specific Recommendations
Industry | Typical Application | Recommended Thread Mill Type |
---|---|---|
Aerospace | Titanium, Inconel parts | Integral solid carbide micro thread mills |
Medical Devices | Micro stainless steel implants | Precision-coated thread mills |
Automotive Manufacturing | Cast iron/aluminum alloy housings | Indexable thread mills (with coolant holes) |
Mold Making | Hardened steel blind holes | Multi-flute high-performance thread mills |
✅ Conclusion: From “Habitual Tapping” to “Rational Process Selection”
On modern CNC machining centers, thread milling is gradually replacing traditional tapping as the mainstream process thanks to its flexibility, stability, and efficiency. It is not only a powerful solution for handling complex geometries and difficult-to-machine materials but also a key tool for achieving cost savings, improving efficiency, and enhancing competitiveness.
If you’re looking for a smarter, more economical, and stable threading solution , consider upgrading your process—unlock the full potential of your machining center.
📩 Want to learn more about thread milling applications or get a custom solution? Feel free to contact us anytime!
📞 WhatsApp: +65 89420188 / WeChat: +8618971569567
📧 Email: sdfgroup@sdftools.com
🔗 LinkedIn: Shengdefu Precision Tools Co., Ltd