End milling cutter is a kind of tool commonly used in CNC milling. Its structure features are distinct and each part has different functions. The following is a detailed analysis of each part of the opposite milling cutter:
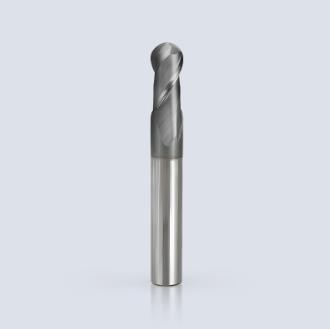
First, the tip of the knife
Position: The tip of the cutter is the meeting point of the cutting edge of the end mill, and it is the first part to contact the workpiece during the cutting process.
Function: The shape and Angle of the tool tip have an important effect on the cutting performance. Reasonable tip design can improve cutting efficiency and prolong tool life.
Second, peripheral edge
Location: The peripheral edge is located on the cylindrical surface of the end mill and is the main cutting edge of the end mill.
Function: The peripheral edge undertakes most of the cutting work, and its sharpness and wear resistance directly affect the cutting efficiency and processing quality.
Features: The peripheral edge is usually spiral, which can increase the smoothness of cutting and improve the chip removal performance.
Third, bottom edge (end edge)
Position: The bottom edge is located on the end face of the end mill and intersects with the peripheral edge to form the tip.
Function: The bottom edge is mainly used to process the bottom plane perpendicular to the side, and can also participate in the side processing.
Features: The cutting edge length and Angle design of the bottom edge need to be determined according to the processing needs to ensure the processing accuracy and surface quality.
Fourth, the core thickness
Position: Core thickness refers to the thickness of the center part of the end mill, that is, the part between the peripheral edge and the bottom edge.
Function: Core thickness is an important factor that determines the rigidity of the end mill and the chip sink. The larger the core thickness, the better the rigidity of the end mill, but the chip removal performance may be worse as the space of the chip containing slot is reduced.
Selection: The choice of core thickness should be considered according to the machining material, cutting depth and cutting speed.
Fifth, chip tank
Location: The chip sink is located between the outer edge and the bottom edge of the end mill and is used to store the chips generated during cutting.
Function: The design of the chute has an important influence on the chip removal performance. Reasonable chip tank shape and depth can ensure smooth chip discharge, avoid chip clogging and tool overheating.
Features: The shape and depth of the chute need to be determined according to the shape of the cutting edge and cutting parameters.
Sixth, spiral Angle
Position: Spiral Angle refers to the Angle between the tangent line of the spiral cutting edge of the end mill and the axis of the milling cutter.
Function: The size of the spiral Angle has an important effect on the cutting performance. The larger the spiral Angle, the longer the contact line between the cutting edge and the workpiece, the more uniform the cutting load distribution, which is conducive to extending the tool life. However, too large spiral Angle will also increase the axial component of cutting resistance, and the rigidity of the tool holder is higher.
Selection: The choice of spiral Angle should be considered according to the machining material, cutting depth and cutting speed.
Seventh, knife handle
Position: The shank is the part of the end mill connected to the machine spindle, which is used to grip the tool on the machine spindle and drive its rotation.
Function: The rigidity and accuracy of the tool handle have an important influence on the cutting performance. Reasonable tool handle design can ensure the stability and accuracy of the tool in the cutting process.
Type: There are many types of knife handle, such as BT knife handle, NT knife handle, MT knife handle, HSK knife handle, etc. Different types of tool handles have different characteristics and scope of application.
Eighth, knife neck
Position: The neck is the part between the cutting edge and the tool handle, used to connect the cutting edge and the tool handle.
Function: The design of the knife neck has an important effect on the rigidity and vibration performance of the tool. Reasonable neck design can improve the rigidity and stability of the tool and reduce vibration and noise.
Features: The shape and length of the knife neck should be determined according to the shape of the cutting edge and cutting parameters.
Ninth, other parts
Front Angle and back Angle: The front Angle and back Angle are important Angle parameters on the cutting edge of the end mill, which have an important impact on the cutting performance. The larger the front Angle, the sharper the cutting, but the lower the tip strength; The larger the back Angle, the smaller the friction between the cutting edge and the workpiece, but the wear resistance of the cutting edge may become worse.
Edge bandwidth: Edge bandwidth refers to the width of the cutting edge on the right Angle section of the shaft, which has an important impact on the cutting load and chip removal performance.
Center slot: Some end mills have a center slot on the bottom edge to improve chip removal performance and cutting stability.
In summary, the design and function of each part of the end mill are closely related, which jointly determines the cutting performance and processing quality of the tool. When machining with an end mill, it is necessary to select the appropriate tool type and parameter Settings according to the processing needs to ensure processing efficiency and processing quality.