The end milling depth of the end mill refers to the depth of the end mill tool when cutting on the workpiece, starting from the surface position of the workpiece and cutting along the workpiece axis. This parameter is usually expressed in millimeters (mm) or inches (in), and is an important concept for the neutral milling method of metal working. Here is a more detailed explanation of the end milling depth:
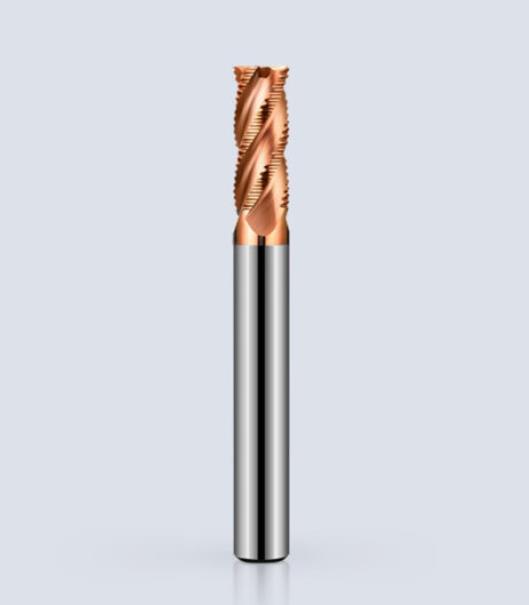
First, definition and meaning
Definition: The end milling depth is the distance of the cutting edge deep into the workpiece when the end milling tool is cutting on the workpiece. It directly determines the thickness of the workpiece material removed by each cutting.
Significance: The depth of end milling is an important factor affecting the efficiency and quality of end milling. The proper depth of end milling can improve the machining efficiency, reduce the machining time, and ensure the quality of the machined surface.
Second, influencing factors
Tool diameter: The effective cutting depth of the end mill is usually designed between 1-3 times the tool diameter to ensure a balance between machining efficiency and tool life. The larger the tool diameter, the greater the allowable cutting depth.
Workpiece material: Workpiece material hardness, toughness and other characteristics will affect the depth of cutting. In general, when processing materials with high hardness and toughness, it is necessary to choose a smaller cutting depth.
Processing requirements: Different processing requirements (such as surface roughness, dimensional accuracy, etc.) need to select different cutting depths. For example, when finishing, it is usually necessary to select a small cutting depth to ensure the quality of the machined surface.
Third, precautions
Avoid overload: Too much cutting depth may cause tool overload, vibration and even break, which affects the machining quality and tool life. Therefore, when selecting the depth of cutting, it is necessary to consider the strength, stiffness and performance of the tool.
Reasonable choice: In actual processing, it is necessary to select the cutting depth reasonably according to the specific processing conditions (such as workpiece materials, processing requirements, tool types, etc.) to achieve the best processing effect.
Fourth, the classification of cutting depth
In end milling, the depth of cutting can also be divided into axial depth of cutting (ap) and radial depth of cutting (ae) :
Axial cutting depth (ap) : refers to the depth of the cutting edge in the workpiece axis.
Radial cutting depth (ae) : refers to the width of the cutting edge in the radial direction of the workpiece.
For different types of end mills (such as right-angle end mills, ball end mills, etc.), the selection and calculation of cutting depth may be different. For example, when using a right-angle end mill for side machining, it is necessary to consider both axial cutting depth (ap) and radial cutting depth (ae). When the ball end mill is used for side machining, due to the cutting characteristics of the ball end mill, the periodic feed (pf) is usually used instead of the radial cutting depth (ae).
Generally speaking, the depth of end milling is an important parameter in end milling, which directly affects the efficiency and quality of machining. In actual processing, it is necessary to select the cutting depth reasonably according to the specific processing conditions to achieve the best processing effect.