success cases
Дом/служба
success cases 1
A Defense Conglomerate (Honeycomb Structure Machining for Y-20 Transport Aircraft)
Challenge: Aviation-grade aluminum alloy honeycomb structures prone to deformation; conventional tools caused severe vibration with <30min tool life.
Solution: Customized 600mm large-diameter carbide end mill with optimized helix angle + vibration-damping coating and expanded chip flutes.
Results: 50% machining efficiency improvement, 2-hour tool lifespan achieved, meeting annual production demand of 50 aircraft.
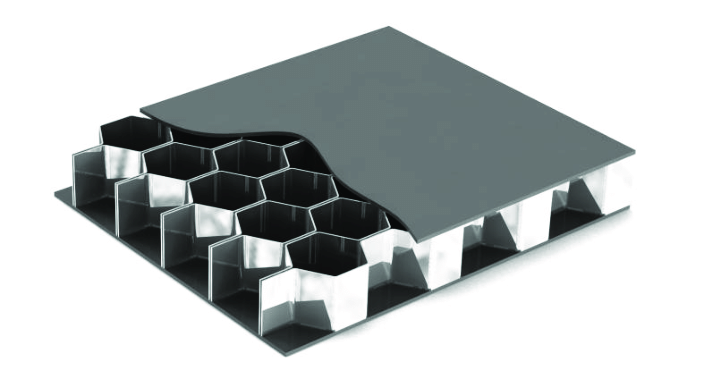
success cases 2
Huawei Technologies (High-gloss Chamfering for Titanium Alloy Phone Frames)
Challenge: Mirror finish required for micro-radius chamfers (R0.05mm) on titanium frames with ±0.003mm tolerance.
Solution: 0.2mm ultra-fine grain tungsten steel ball-nose cutter with PVD nano-coating + dynamic balancing design.
Results: Yield rate increased from 82% to 98%, tools maintained edge integrity through 8,000 continuous cycles.
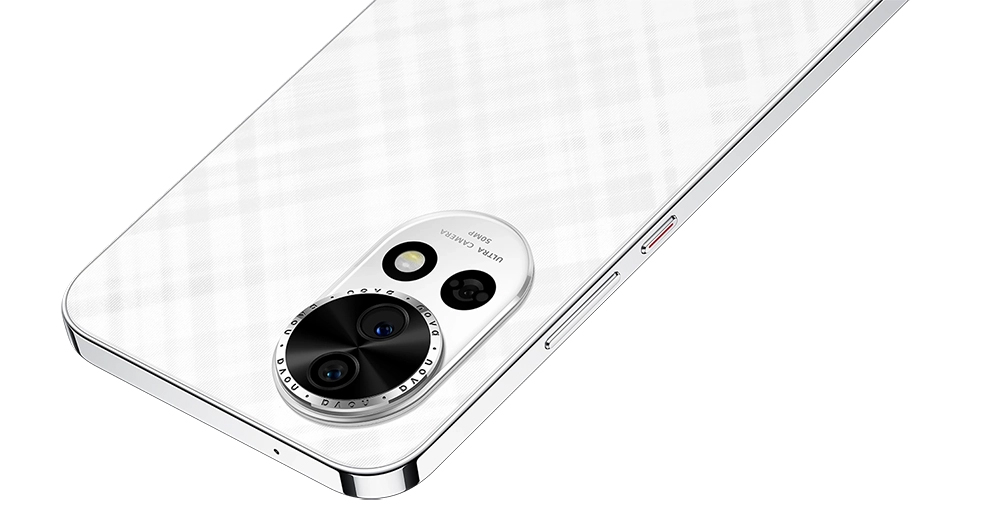
success cases 3
New Energy Vehicle Motor Housing Supplier
Challenge: Severe built-up edge in silicon-aluminum alloy deep cavity machining, surface roughness exceeding Ra1.6.
Solution: Variable-rake stepped milling cutter with TiAlCrN coating to reduce friction coefficient.
Results: 25% cycle time reduction, 3× tool life extension, achieving annual cost savings of 1.2 million RMB.
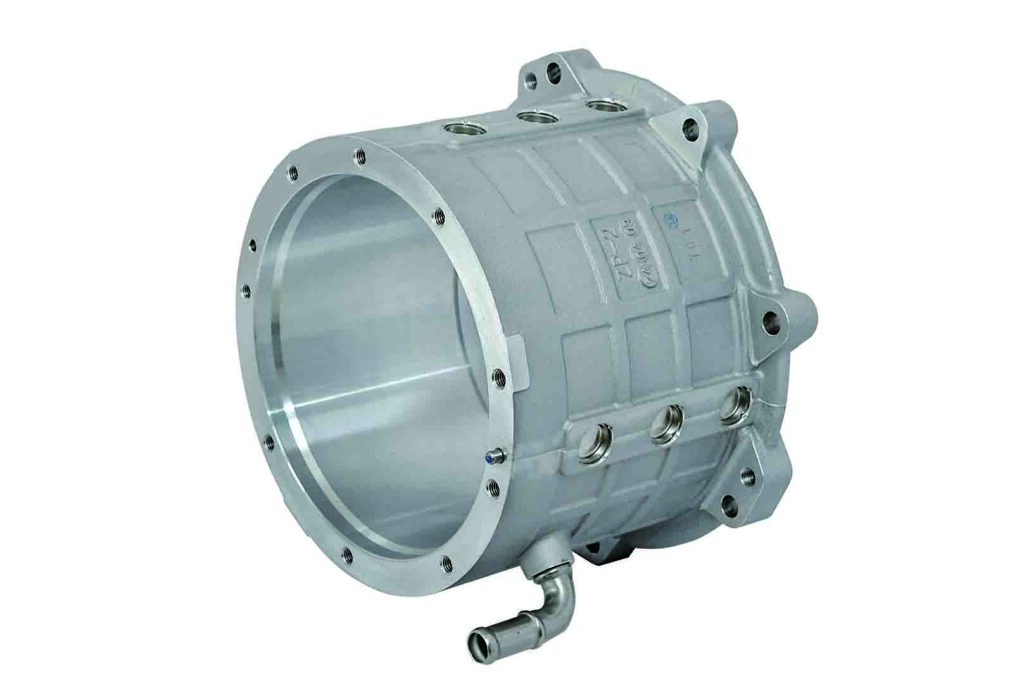
success cases 4
China's Leading Cable Mold Manufacturer (HRC65 Tungsten Carbide Die Machining)
Challenge: Over 40% edge chipping rate in tungsten carbide die cavity machining (HRC65).
Solution: Dual-layer composite coating (AlTiN+MoS2) spiral end mill with optimized edge passivation.
Results: 35% efficiency improvement, IT5-grade die accuracy achieved, 100% repeat order rate.
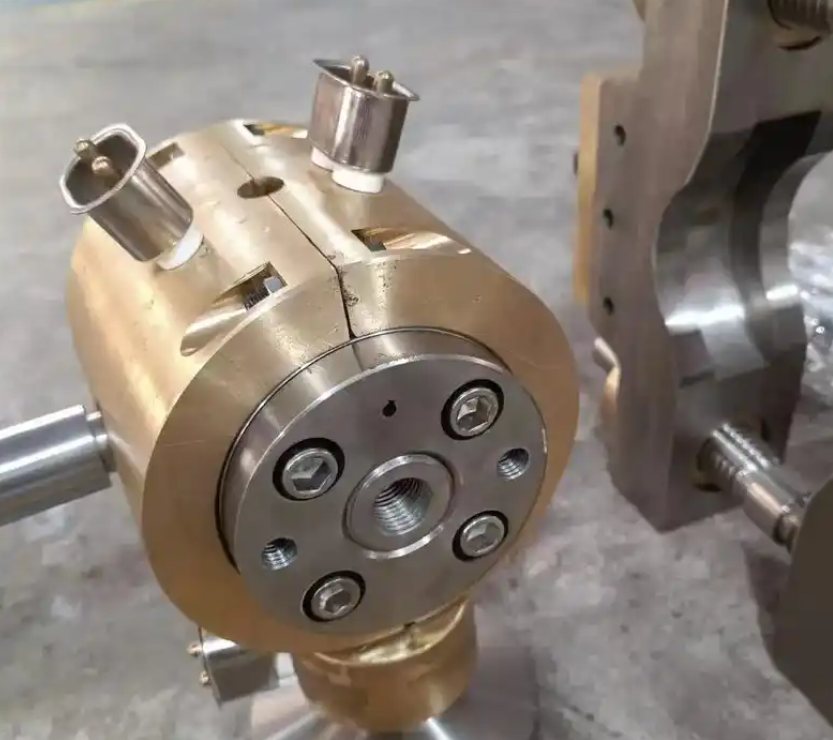
success cases 5
Aerospace Fuel Tank Manufacturer (Inconel 718 Thin-wall Machining)
Challenge: >0.1mm deformation in 2mm-thick Inconel 718 thin-wall components.
Solution: Low-depth-of-cut high-feed mill with negative rake angle + high-pressure internal coolant channels.
Results: Deformation controlled within 0.03mm, tool lifespan reached 2.2× industry benchmark.
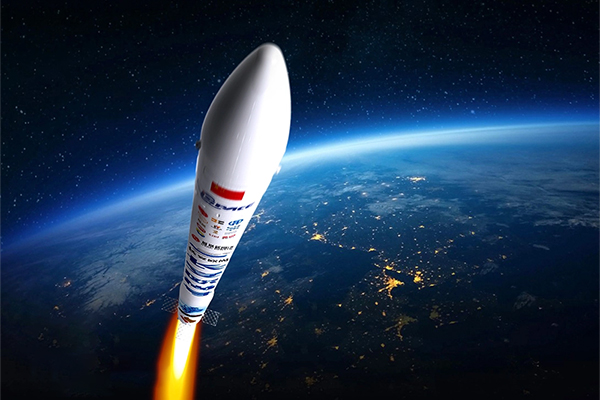
success cases 6
Medical Device Leader (Cobalt-Chromium-Molybdenum Alloy Joint Machining)
Challenge: Burr formation in biocompatible material machining requiring ISO Class 5 cleanliness.
Solution: 5-axis dedicated polishing cutter with nano-diamond coating + specialized edge reinforcement.
Results: Achieved Ra0.2μm surface roughness, eliminating post-machining manual polishing.
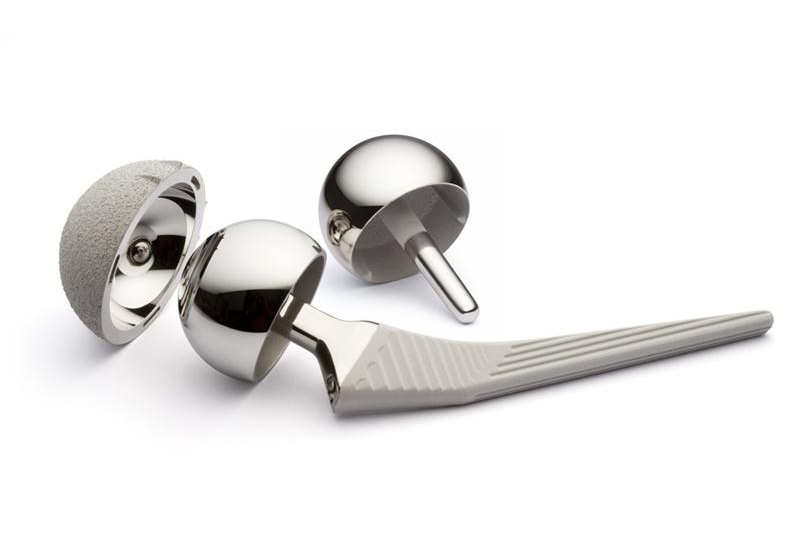
success cases 7
Wind Turbine Blade Mold Supplier
Challenge: Delamination defects in GFRP machining with 10× faster tool wear vs metal cutting.
Solution: PCD-coated milling cutter with 72° helix angle for optimized fiber cutting.
Results: 800-hour mold service life, 60% dust reduction during processing.
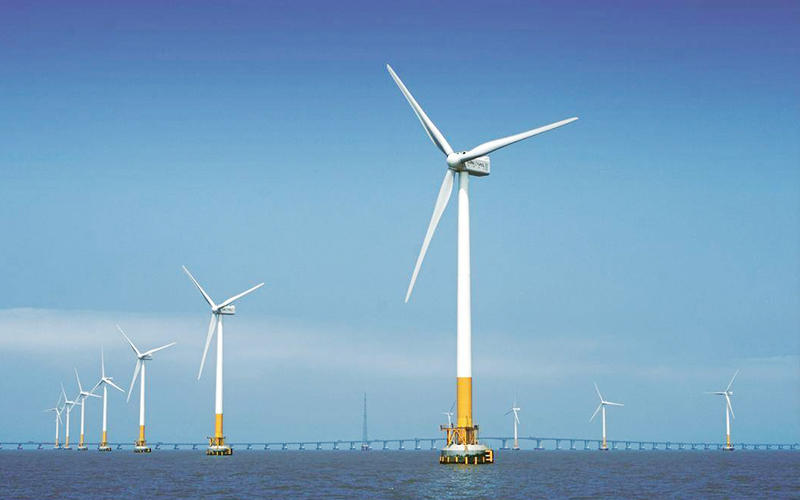
success cases 8
Case 8: High-speed Train Gearbox Supplier
Challenge: 180min/part cycle time for 18CrNiMo7-6 carburized steel gear profile machining.
Solution: Modular indexable gear cutter with dual-positive rake insert design.
Results: Cycle time reduced to 110min, tool change frequency decreased by 70%.
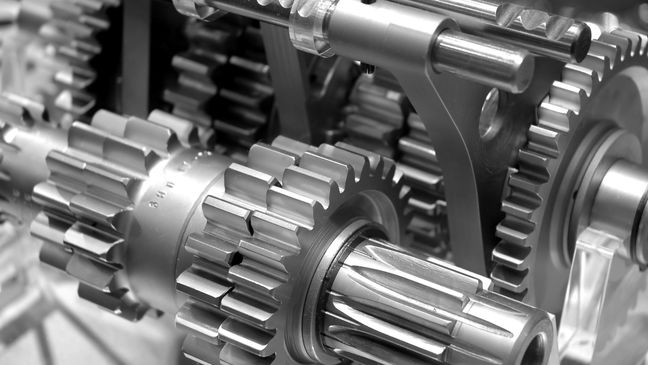