Introduction
In the field of machining, while standard tools can meet most general needs, industries such as aerospace, medical devices, and automotive components often require customized tools that are deeply optimized for specific materials, processes, and equipment. As a company specializing in high-end custom tooling, we leverage our strong customization capabilities, extensive case library, and professional engineering team to provide tailored solutions for virtually any machining application.
This article will showcase our technical expertise and customization advantages through an actual case study of a custom step drill designed for a complex machining scenario.
Customer Requirements Analysis
An aerospace manufacturing company needed to process a high-strength alloy component involving multi-step hole machining with extremely high dimensional accuracy and surface quality requirements. The specific needs were as follows:
- Size Specifications:
- First step diameter: 4.8 mm, length: 10 mm;
- Second step diameter: 8 mm, length: 20 mm;
- Total length: 80 mm.
- Tolerance Requirements:
- Diameter tolerance: ±0.01 mm;
- Length tolerance: ±0.05 mm;
- Angular tolerance: ±0.25°.
- Material Properties:
- The material to be machined was a hard alloy with a hardness of HRC 50-60.
- Surface Quality:
- Hole wall roughness needed to achieve Ra 0.8 μm.
- Tool Life:
- Each step drill had to guarantee at least 5,000 parts processed while maintaining precision.
The customer attempted to use standard step drills available on the market but encountered the following issues:
- Excessive tool wear, leading to frequent replacements;
- Dimensional deviations during machining, failing to meet high-precision requirements;
- Poor chip evacuation, affecting machining efficiency.
Our Customized Solution
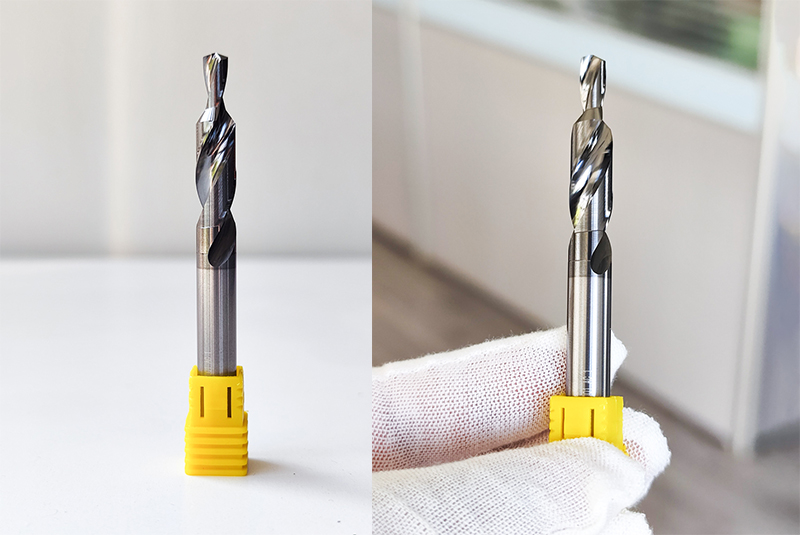
1. Demonstrating Strong Customization Capabilities
With extensive customization experience and technical expertise, we quickly responded to the customer’s needs and addressed the following aspects in the design:
- Structural Design:
- The first step (diameter 4.8 mm, length 10 mm) featured an optimized cutting edge design to reduce cutting resistance and enhance machining stability.
- The second step included widened chip grooves to ensure efficient chip evacuation.
- Overall rigidity was optimized to prevent vibration issues during long overhang machining.
- Material Selection:
- A high-performance carbide substrate was chosen for its excellent wear resistance and impact resistance.
- A TiAlN (Titanium Aluminum Nitride) coating was applied to further enhance high-temperature and wear resistance.
- Geometric Parameter Optimization:
- A custom helix angle of 30° balanced cutting forces and chip evacuation performance.
- The point angle was adjusted to 140° to reduce heat accumulation and improve machining stability.
- The land width was optimized to 0.15 mm to ensure smooth hole walls.
2. Support from an Extensive Case Library
Our case library contains thousands of successful customization examples covering a wide range of machining scenarios, from ordinary steel to high-strength alloys and composite materials. Drawing on similar cases, we quickly identified the optimal design and fine-tuned it based on the customer’s unique requirements. This “data-driven” customization approach significantly shortened the development cycle while ensuring the reliability of the solution.
3. Technical Assurance from a Strong Engineering Team
Our engineering team consists of experts with over 10 years of industry experience. They not only excel in tool design and manufacturing but also have deep insights into various machining processes. In this project, the team ensured the success of the solution through the following measures:
- Using advanced CAD/CAM software for 3D modeling and simulation analysis to validate the feasibility of the design;
- Employing five-axis CNC grinders for precision machining to ensure that each step’s diameter, length, and angle met strict tolerance requirements;
- Conducting dynamic balancing tests to further enhance the stability of the drill during high-speed rotation.
Testing and Validation
After completing the manufacture of the custom step drill, we sent it to the customer’s production site for testing. Below are the test results:
- Machining Accuracy:
- All step holes had diameter errors controlled within ±0.005 mm, far exceeding the customer’s requirement of ±0.01 mm.
- Hole depth errors were controlled within ±0.03 mm, also surpassing expectations.
- Surface Quality:
- The average roughness of the hole walls was Ra 0.6 μm, fully meeting the requirement of Ra 0.8 μm.
- Tool Life:
- After continuously machining 5,000 parts, the drill showed minimal wear and could still be used. The estimated total lifespan was 7,000–8,000 parts.
The customer was highly satisfied with the test results and decided to place a bulk order for the custom step drill for formal production.
Results and Value
The successful development of this custom step drill fully demonstrated our core strengths in the following areas:
- Strong Customization Capabilities:
- From analyzing customer requirements to final delivery, the entire process was efficient and precise, enabling rapid response to complex demands.
- Support from an Extensive Case Library:
- Our case library covers most machining applications, providing matching solutions and data for both material properties and process requirements.
- Technical Assurance from a Professional Engineering Team:
- With deep technical expertise and innovative capabilities, our engineers provided the optimal solution for the customer.
Through this collaboration, we not only helped the customer solve their machining challenges but also significantly improved their production efficiency and product quality. This win-win cooperation model is the core value of our customization service.
Conclusion
As a company specializing in high-end custom tooling, we are committed to providing the highest-quality solutions for our customers. No matter how complex your machining requirements may be, we are confident in delivering the best solution tailored to your needs through our strong customization capabilities, extensive case library, and professional engineering team.
If you have similar customization needs, feel free to contact us anytime! With our professional technology and attentive service, we will help you achieve more efficient and stable machining goals.
Customization Capability, Rooted in Professionalism; Perfect Solutions, Achieving Excellence!