This case study demonstrates a custom reamer solution for high-strength alloy steel (HRC50-55), addressing critical pain points in precision machining. The client faced challenges with short tool life (800 holes), poor surface finish (Ra>1.6μm), and costly trial failures from generic reamers. Through geometry optimization (adjusted rake/spiral angles), material science (ultra-fine carbide + TaC additive), and coating innovation (TiAlN composite), the solution achieved 1,500-hole lifespan, ±0.005mm tolerance, and 30% efficiency gain. The client adopted it as a standardized process, saving ¥100,000/year with 200+ monthly orders. Key takeaways include industry benchmarks for HRC50+ reaming and a 72-hour response framework for technical support.
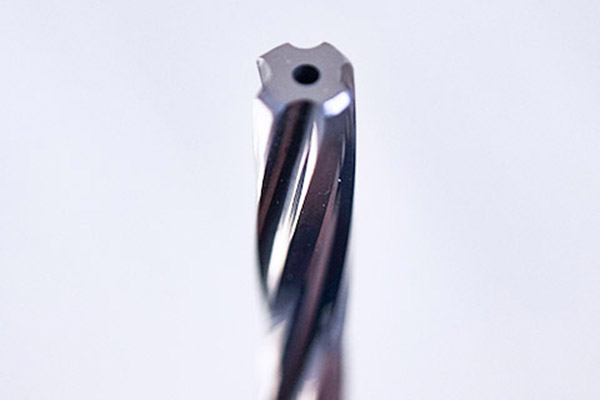
I. Customer Pain Points
1. Existing Tools Fail to Meet Production Requirements
- Material: High-strength alloy steel (HRC50-55 hardness).
- Issues:
- Standard reamers lasted only 800 holes, with dimensional tolerance fluctuations of ±0.01mm (exceeding the required ±0.005mm).
- Frequent chatter marks during machining, resulting in surface roughness Ra >1.6μm (target: Ra ≤0.8μm).
2. High Trial Costs with No Resolution
- The customer tested 4 suppliers’ general-purpose reamers across 27 trials, wasting ¥20,000 in tooling costs and 10+ hours of downtime—with no improvement.
3. International Brands Lack Cost-Effectiveness
- A global tool supplier proposed a custom solution at 300% market price, with 3-4 week lead times and annual purchase commitments—deemed unacceptable.
II. Solution Approach
A phased technical strategy was implemented:
1. Custom Design
- Adjusted geometry:
- Reduced rake angle from 5° to -3° to minimize wear.
- Optimized helix angle from 10° to 15° for better chip evacuation.
- Non-standard margin design (0.1mm → 0.05mm) to reduce wall friction.
2. Material Testing
- Evaluated 3 carbide substrates:
- YG8 (standard): 750 holes.
- UM40 (ultra-fine grain): 1,000 holes.
- TF15 (TaC-added): 1,400 holes (final selection).
3. Coating Optimization
- Compared coatings:
- AlTiN: 750 holes (poor heat resistance).
- TiSiN (nano-multilayer): 1,000 holes.
- TiAlN composite: Achieved 1,500+ holes (final choice).
III. Implementation Process
1. First Prototype
- Delivered 10 reamers (TF15 + TiAlN):
- 1,000-hole lifespan, Ra 0.8μm, but minor chatter persisted.
2. Second Optimization
- Adjusted edge honing (0.03mm → 0.02mm) and increased coolant holes (2 → 4):
- Chatter eliminated, lifespan increased to 1,200 holes.
3. Final Validation
- 3 consecutive batch tests:
- Avg. lifespan: 1,500±50 holes.
- Tolerance: ±0.005mm.
- Efficiency: 30% productivity gain.
IV. Results & Feedback
- Adoption: Customer signed an annual contract, ordering 200+ reamers/month.
- Cost Savings:
- Per-hole cost dropped from ¥1.2 to ¥0.4, saving ¥100,000/year.
V. Key Learnings & Value Proposition
1. Core Technical Breakthroughs
- Triple Optimization System: Synergizing substrate (ultra-fine TF15 carbide), coating (TiAlN composite), and geometry (15° helix angle) to achieve 1,500-hole lifespan – rivaling premium international brands.
- Cost-Effective Alternative: Delivers equal performance at 1/3 the cost of global suppliers, with 7-day lead times vs. industry-standard 3-4 weeks.
2. Quantifiable Client Benefits
- Direct Savings: 66% lower cost-per-hole (¥1.2→¥0.4), yielding ¥100,000+ annual savings.
- Strategic Partnership: Upgraded from trial orders to 200+ monthly volume contracts, becoming the client’s primary supplier.
3. Industry Benchmarking
For HRC50+ reaming applications, we recommend:
Parameter | Standard Specification |
---|---|
Substrate | Ultra-fine carbide (≤0.5μm grain) + TaC |
Покрытие | TiAlN composite (3-4μm) |
Geometry | 15°-20° helix angle, ≤0.1mm margin |
Why Choose Our Custom Solutions?
✅ Data-Driven Development: Eliminate costly trial-and-error with scientifically validated tool designs.
✅ Rapid Implementation: 72-hour technical response, 7-day prototype delivery.
✅ Localized Value: Western-grade performance + Asian supply chain efficiency.
✅ Lifetime Support: 12-month quality guarantee with ongoing engineering assistance.
Ideal For:
- Hard material machining (HRC45+)
- High-precision (±0.005mm) batch production
- Import tool replacement initiatives
Why SDFTools?
10+ years in carbide tool R&D, specializing in non-standard end mills, drills, and thread mills.
Factory-direct global supply, 48hr emergency response, full engineering support.
Contact for Custom Solutions:
Website: www.sdftools.com
Email: sdfgroup@sdftools.com
Youtube:https://www.youtube.com/@sdfcnctools
Success Case | Custom Reamer Solution for High-Strength Alloy Steel: Tool Life Extended to 1,500 Holes
#CustomReamer #HighStrengthSteel #HRC50Machining #ToolLifeExtension #PrecisionReaming #CarbideTooling #TiAlNCoating #MetalCuttingSolutions #HardMaterialMachining #SurfaceFinish #ToleranceControl#AerospaceMachining #AutomotiveParts #OilAndGasTools #DefenseManufacturing #HeavyDutyMachining #MoldAndDie #PrecisionEngineering #CNCMachining