The service life of end mill is a complicated problem affected by many factors. The following is a detailed introduction to the service life of the opposite milling cutter:
First, overview of service life
The service life of end mills is usually between 3,000 and 4,000 hours, but this is only a rough estimate. The actual service life will be affected by many factors such as blade material, working conditions, maintenance and so on.
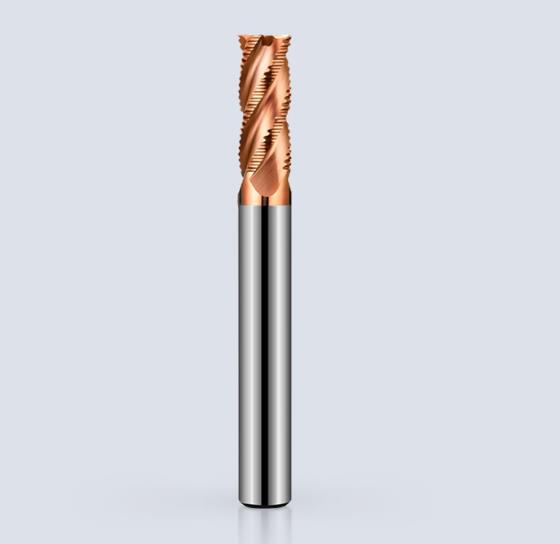
Second, the factors affecting the service life
Blade material:
Carbide: Suitable for high-speed machining because of its good wear resistance, but the cost is higher.
High speed steel: economical, but relatively short life.
Working conditions:
Workpiece material: the strength, hardness, toughness, thermal conductivity and other characteristics of the material will affect the wear rate of the mill.
Cutting speed and depth: increasing the cutting speed will significantly increase the cutting temperature and accelerate the milling tool wear; Increasing the cutting depth will make the cutter withstand greater cutting forces, which will also accelerate wear.
Maintenance:
Regular cleaning and lubrication: prevents tool rust and reduces wear.
Timely grinding or replacement of worn blades: can maintain the cutting performance of the tool, extend the service life.
Other factors:
Tool geometric parameters, such as front Angle, main declination Angle, etc., affect the cutting force and cutting temperature of the tool, thus affecting the service life.
Cutting fluid: Reasonable selection and full use of cutting fluid can reduce cutting temperature and reduce friction resistance, extend tool life.
Third, the method of extending the service life
Reasonable selection of cutting parameters: scientific setting of cutting parameters according to workpiece material and tool performance to avoid overload use.
Use the right cutting fluid: to improve heat dissipation conditions, reduce the cutting temperature.
Improve the geometric Angle of the tool: such as increasing the front Angle, reducing the main deflection Angle, etc., to reduce the cutting force and cutting heat.
Regular maintenance: including cleaning, lubrication, inspection and grinding.
In summary, the service life of end mill is a dynamic process affected by many factors. Through comprehensive consideration of material selection, optimizing working conditions and strengthening maintenance measures, the service life of end mill can be effectively extended, and production efficiency and economic benefits can be improved.