End milling cutter as the most commonly used tool in CNC milling, has many significant advantages, the following is a detailed introduction to its advantages:
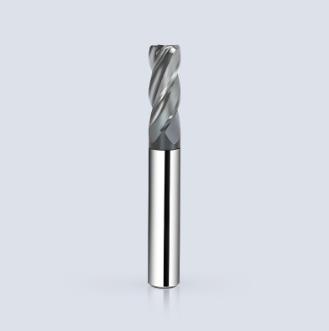
First, efficiency
Fast cutting speed: the main cutting edge of the end mill is located on the cylindrical surface, and the secondary cutting edge is distributed on the end face. This structure makes the end mill can cut in multiple directions at the same time, which greatly improves the cutting efficiency.
High cutting efficiency: end milling cutter is suitable for large cutting amount processing, can complete a large number of processing work in a short time, improve the overall production efficiency.
Second, high precision
High processing accuracy: the end mill head is relatively strong, not easy to deformation and wear, the contact area between the tool and the workpiece is small when cutting, so the machined parts have high accuracy.
Adapt to complex surface processing: the end mill head is relatively thin, can mill out more complex curved parts, such as three-dimensional surface, groove, step surface, etc., to meet the needs of high-precision processing.
Third, versatility
A wide range of processing: the end mill can not only be used for surface milling, groove milling, step surface milling and other traditional processing, but also for copying milling, side processing, groove processing and other processing forms, with a wide range of applications.
Adjustable cutting profile: the cutter head cutting profile of the end mill can be arbitrarily adjusted to adapt to the processing of different shapes and sizes of the workpiece, improving the flexibility and adaptability of processing.
Fourth, economy
Reduce production costs: Although the end mill itself may have a high procurement cost, due to its high cutting efficiency and high processing accuracy, processing time and material waste can be significantly reduced, thereby reducing the overall production cost.
Extension of tool life: Through reasonable cutting parameter selection and tool maintenance, the end mill can maintain a long service life, reduce the frequency of tool replacement, and further reduce production costs.
Fifth, other advantages
Good stability: the main cutting edge of the end mill is spiral teeth, which can improve the smoothness of cutting, reduce vibration and noise, and protect the machine tool and the workpiece from damage.
Easy to operate: the structure of the end mill is relatively simple, easy to operate and install, reducing the difficulty of operation and labor intensity.
Matters needing attention
Although the end mill has many advantages, the following points also need to be noted when using:
Selection of cutting parameters: According to the material, shape and processing requirements of the workpiece, the appropriate cutting speed, feed and depth of cutting parameters should be selected to ensure the processing quality and tool life.
Tool maintenance: Regular inspection and maintenance of the opposite milling cutter, timely replacement of worn blades or tool heads, to maintain the sharpness and stability of the tool.
Safety protection: Safety protection measures should be taken during the cutting process, such as wearing protective glasses, ear plugs, etc., to ensure the safety of the operator.
In summary, end milling cutter has been widely used in manufacturing and machining field for its high efficiency, high precision, versatility, economy and good stability.