At SdfTools, everyone knows that without customer satisfaction, we cannot thrive. Customer satisfaction is measured by the quality of our customer service and products.
Quality is SdfTools’ attitude. We are committed to providing products that meet or exceed all detailed specifications for every tool, every order, every day. Another major quality goal is to monitor and improve the processes that ensure high quality whenever possible.
Service is SdfTools’ strength. Our sales team started from basic technical roles and can efficiently and promptly address issues for distributors and tool users.
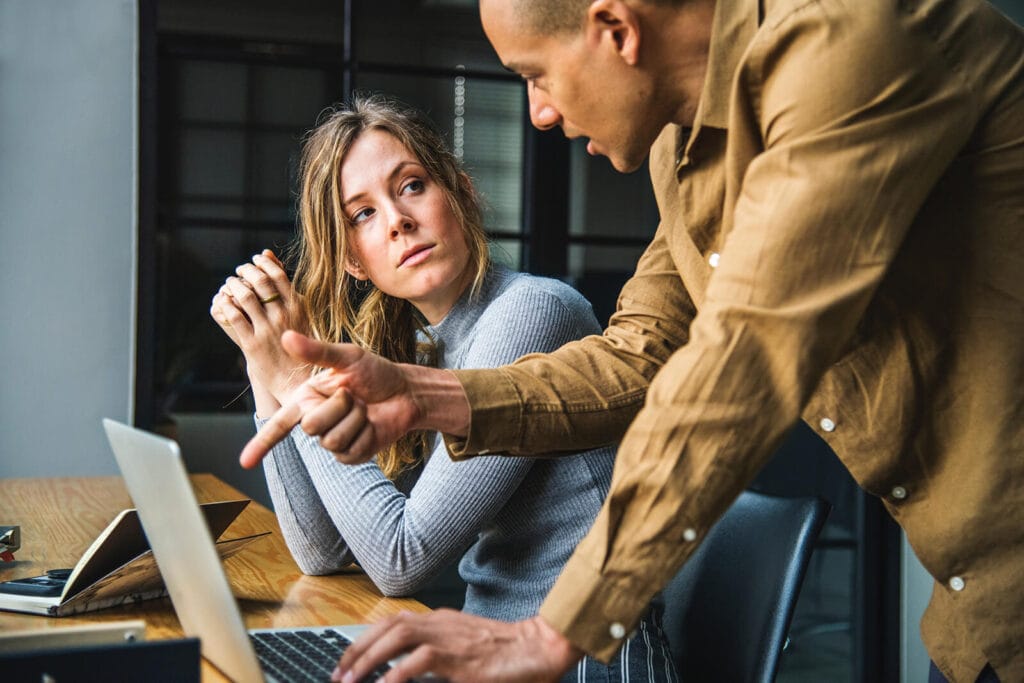
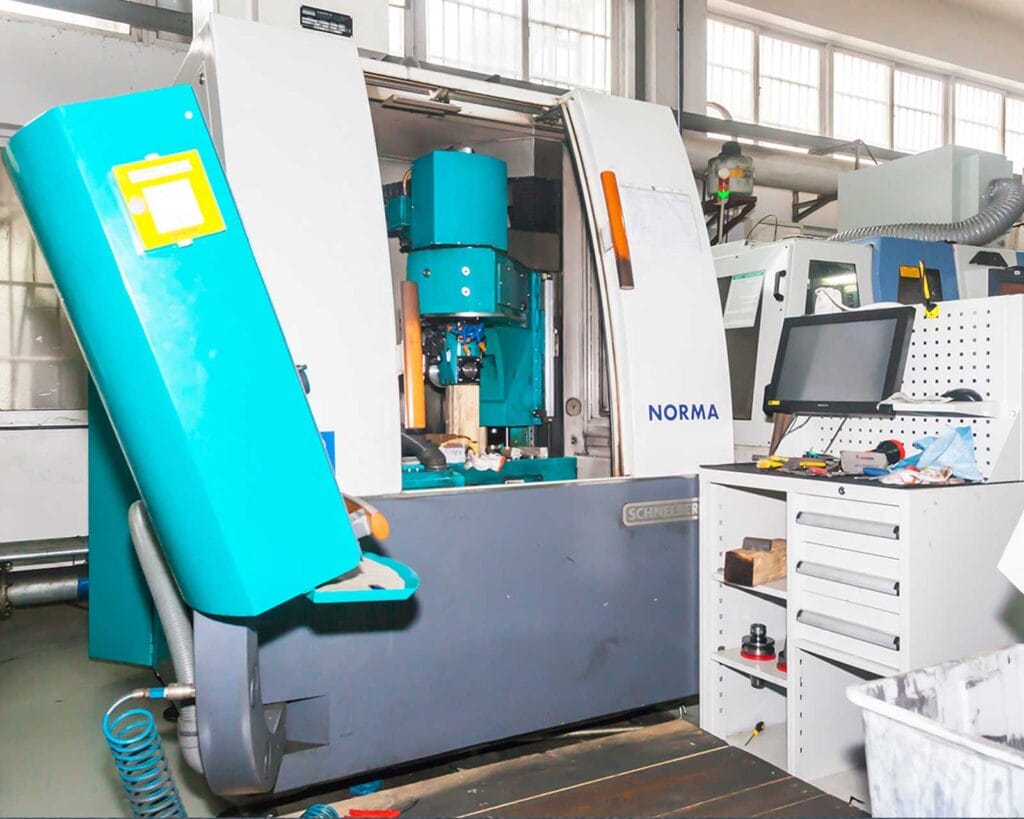
How is SdfTools Different from Other Tool Manufacturers?
Our manufacturing facility is located in Wuhan, China. Every member of the SdfTools team understands that only superior products and excellent service can drive our growth. We offer high-quality end mills and other cutting tools, and in some niche markets, we have unique patents.
SdfTools also provides many added-value features:
- All tools are CNC precision finished.
- Ample stock, typically ships same day.
- Friendly and courteous sales representatives to help you find the right tools for your needs.
- A complete range of solid carbide end mills, including many high-performance carbide tools.
- Excellent engineers to customize highly complex tools for you.
- High-quality carbide and PCD tools at very competitive prices.
- Certified quality systems (ISO 9001:2000) to ensure tools meet or exceed your tolerances.
Visit Process
A Comprehensive Guide from Appointment to Farewell
- Appointment Booking 1
• Customers contact us via phone or email to schedule a visit.
• We confirm the date and time of the visit and arrange a receptionist - Reception and Welcome 2
• Upon arrival, customers are greeted by a receptionist and escorted to the reception room.
• Tea and water are provided, along with a brief introduction to our company background. - Factory Tour 3
•A dedicated guide accompanies customers to tour the production lines and workshops.
•Detailed explanations of production processes, equipment, and quality control procedures are provided.
- Technical Exchange 4
•Arrange a meeting with the technical team to discuss specific customer needs.
•Show samples and relevant technical documents. - Lunch Reception: 5
•nvite customers to join us for lunch to build rapport.
•Lunch can be served in the factory canteen or a nearby restaurant. - eedback and Summary&Farewell 6
•After the tour, collect feedback from customers.
•Summarize the visit and discuss potential future cooperation.
•Escort customers to their departure point and thank them for their visit.
•Provide contact information for further communication.