In CNC machining, the performance of carbide tools directly impacts processing efficiency, precision, and cost. Selecting the right tools not only improves product quality but also extends equipment lifespan and reduces scrap rates. However, with the vast array of carbide tools on the market, how can you quickly identify the optimal choice? This article outlines 10 key evaluation criteria to ensure precise tool selection.
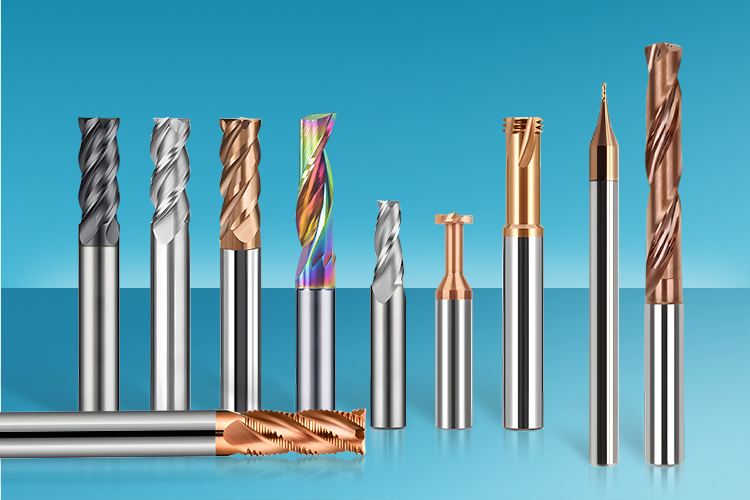
1. Material Compatibility: Match Workpiece Properties
Selecting carbide tool grades (e.g., G, G-SUS, M series) determines their suitability for specific applications:
- G Series (General Purpose): Versatile for multi-material and complex working conditions.
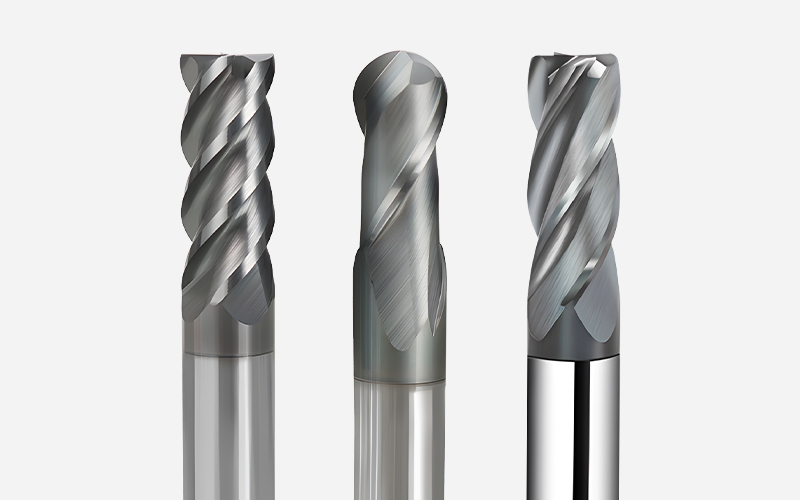
- G-SUS Series (Stainless Steel Specialized): Optimized for stainless steel, cast iron, non-ferrous metals, and non-metallic materials, with high bending strength.
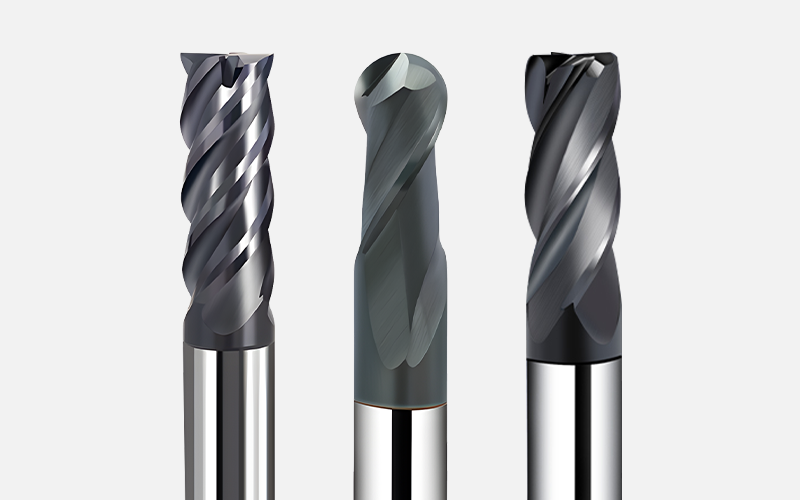
- H Series (High Performance): Ideal for steel processing, offering exceptional high-temperature resistance.
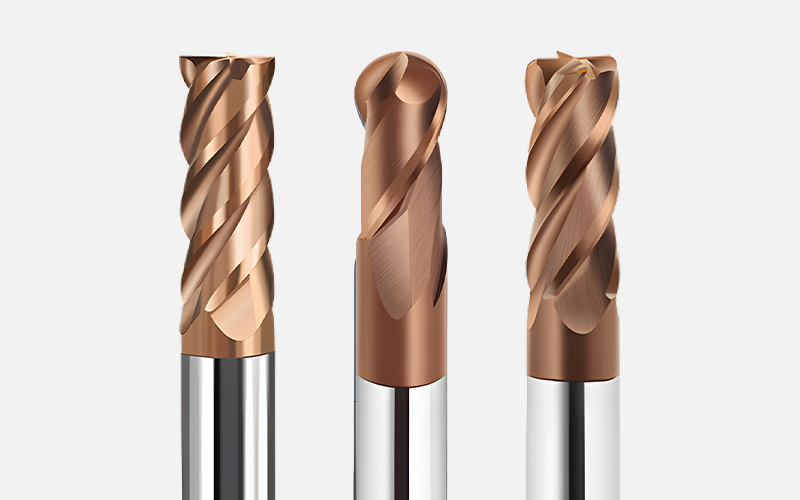
Tip: For high-hardness materials (e.g., stainless steel, titanium alloys), choose ultra-fine grain carbide grades.
2. Coating Technology: Enhance Wear & Heat Resistance
Coatings are critical for extending tool life:
- CVD Coating: Thick, wear-resistant layers suited for high-speed steel machining.
- PVD Coating: Smooth surface with low friction, ideal for precision parts and thin-walled components.
- Case Study: TiAlN-coated tools achieve over 3X longer lifespan in high-temperature alloy machining.
3. Tool Geometry: Optimize Cutting Efficiency
Parameters like rake angle, relief angle, and helix angle directly affect cutting force and chip evacuation:
- Roughing: Large rake angle + high helix angle for improved chip removal.
- Finishing: Smaller rake angle + sharp edge to reduce surface roughness.
Note:
- Avoid excessively sharp edges for steel machining to prevent chipping; adjust edge preparation.
- For aluminum/soft non-ferrous metals, prioritize sharp-edged tools.
4. Cutting Parameter Matching: Speed, Feed & Depth
- Cutting Speed (Vc): 80–200 m/min for carbide tools in steel machining.
- Feed Rate (Fz): Excessive feed accelerates wear; insufficient feed causes built-up edge.
- Depth of Cut (Ap):
- Roughing: ≥50% of tool diameter.
- Finishing: ≤0.5 mm.
5. Brand & Quality Certification
Prioritize ISO 1081-certified brands for tool consistency. While global brands (e.g., Sandvik, Kennametal) dominate with technical stability, Chinese manufacturers like SDFTools now match global standards through independent R&D. By integrating smart manufacturing, SDFTools delivers 30% higher cost-efficiency while maintaining “German Precision, Chinese Smart Pricing.”
6. Supplier Technical Support
Evaluate:
- Customization: Non-standard tool design capabilities?
- After-Sales: Regrinding services, troubleshooting response time.
7. Cost-Effectiveness Analysis
- Per-Piece Cost: Low-priced tools may increase overall cost due to shorter lifespan.
- Total Cost: Factor in tool life, changeover time, and downtime.
- Data Insight: Coated tools cost 20% more but boost lifespan by 50+%, proving more economical long-term.
8. Application-Specific Requirements
- Roughing: Prioritize high-strength, impact-resistant tools.
- Finishing: Focus on edge sharpness and surface finish.
- Special Industries:
- Aerospace: High-temperature resistance.
- Medical: Contamination-free coatings.
9. Tool Life & Stability
Predict lifespan via the Taylor Equation (VT^n = C) and monitor wear in real-world applications.
Recommendation: Record wear curves periodically to optimize replacement cycles.
10. Compatibility & System Integration
- Shank Type: Match HSK, BT, or other interfaces to machine tool.
- Dynamic Balancing: Use G2.5+ balanced tools for high-speed machining.
- Cooling Method: Internal coolant for deep cavities; external coolant for simple structures.
Conclusion
Selecting the right carbide tools is pivotal for cost-effective, high-quality CNC machining. Every step—from material matching to parameter optimization, brand evaluation to cost calculation—requires meticulous planning. For tailored solutions, contact our engineering team for free tool selection guidance!
Service Commitment
Fast Delivery:
Standard items shipped in 3 days | Custom orders completed in 5-10 days | Small trial batches supported
Technical Support:
Senior engineers available for real-time collaboration
CAD drawings provided or custom-designed per requirements
Contact Now:
? Website: www.sdftools.com
? Technical email: sdfgroup@sdftools.com
⚡ Urgent Needs: WhatsApp: +65 89420188 (24/7 Engineer Hotline)