The helix angle of the end mill has a significant impact on machining, which is mainly reflected in the following aspects:
First, cutting performance
Cutting sharpness:
The larger the helix angle, the larger the actual front angle of the end mill, the sharper the edge, the lighter and smoother the cutting.
Cutting resistance:
The tangential cutting resistance decreases with the increase of helix angle, which helps to reduce the friction and heat generation in the cutting process.
Axial cutting resistance increases with the helix angle, which may lead to the tool in the axial direction to withstand a greater force, the need to choose a good rigidity of the toolholder to support.
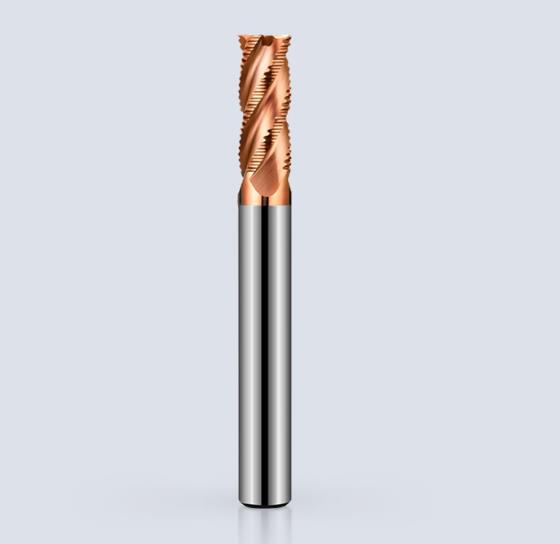
Second, machining quality
Surface roughness:
Helix angle increases, the contact length between the cutting edge and the workpiece increases, the load borne by the cutting edge per unit length decreases, and the cutting process is smoother, which is conducive to reducing surface roughness and improving machining accuracy.
Machining accuracy:
The change of helix angle has a complex effect on machining accuracy. In general, an increase in the helix angle may increase the perpendicularity and flatness tolerance value of the machined surface, but after the helix angle is greater than 40 °, this trend may weaken.
Third, tool life
Wear rate:
The wear rate of the circumferential edge band is basically proportional to the size of the helix angle. The larger the helix angle, the longer the contact length between the cutting edge and the workpiece, the more uniform the tool wear, but the overall wear rate may be faster.
Rigidity change:
Helix angle is too small, the tool rigidity may be insufficient, the slightest tool wear will significantly reduce the cutting performance of the tool, causing vibration, so that the tool can not continue to use.
Helix angle is too large, although it can reduce the load per unit length of the cutting edge, but the overall rigidity of the tool may become worse, especially in the processing of less rigid workpieces, easy to deflection or high-frequency vibration, affecting tool life.
Fourth, cutting heat and chip removal performance
Cutting heat:
Helix angle increases, the contact area between the cutting edge and the workpiece increases, and the heat generated during the cutting process may be more. Therefore, for hard-to-cut materials with low thermal conductivity and an easy rise in cutting edge temperature, it is necessary to choose end mills with special cutting edge shapes to suppress the effect of cutting heat on the cutting edge.
Chip removal performance:
The size of the helix angle has a certain effect on the chip removal performance. Generally speaking, the larger the helix angle, the wider the chip removal slot, the better the chip removal performance. However, in some cases (such as high helix angle milling groove channel), it may be necessary to use a small amount of fast cutting to improve chip removal performance.
Fifth, machining efficiency and cost
Machining efficiency:
The helix angle increases, the contact length between the cutting edge and the workpiece increases, and the amount of material removed per unit time may be more, thus improving machining efficiency.
Machining cost:
The selection of helix angle needs to be considered comprehensively tool life, machining quality, machining efficiency and other factors. Reasonable helix angle selection can reduce machining costs and improve economic efficiency.
Suggestions for selection
Selection according to the machining material:
When processing soft materials with low hardness, end mills with large helix angle can be selected to improve cutting sharpness and machining efficiency.
When machining hard materials with high hardness, the end mill with small helix angle can be selected to improve tool rigidity and cutting stability.
Select according to the processing requirements:
When roughing, the end mill with large helix angle can be selected to improve the material removal rate and machining efficiency.
For finishing, select end mills with small helix angle to improve machining accuracy and surface quality.
Consider machine tool performance:
The rigidity of the machine tool, power and other properties will affect the choice of helix angle of the end mill. When the rigidity of the machine is insufficient, it is not suitable to choose the end mill with too large helix angle.
In summary, the helix angle of the end mill has a multifaceted impact on processing. In practical application, according to the specific processing materials, processing requirements, machine performance and other factors to consider, select the appropriate helix angle to obtain the best processing results.