End milling cutter is the most commonly used milling cutter in CNC milling, and its structure is characterized by a cutting edge on the cylindrical surface and the end face, which can be cut simultaneously or separately. There are many types of end mills, and according to different classification standards, there can be the following divisions:
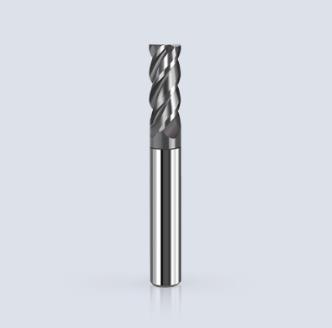
First, classification by blade number
The edge number of end milling cutter mainly has 2 edge, 3 edge, 4 edge, 6 edge and other types. The difference in the number of blades is related to the size of the chute area where the chips are collected. The smaller the number of blades, the larger the area of the chip sink, the smoother the chip discharge, but the worse the rigidity of the tool; The larger the number of edges, the smaller the area of the chip holding slot, the larger the cutting edge area, the higher the rigidity, but the chip removal performance may be affected.
2 – and 3-edge end mills: suitable for parts with poor rigidity or where large chip space is required.
4 – and 6-edge end mills: Suitable for machining where high rigidity and stability are required, such as finishing or high-speed machining.
Second, according to the bottom end tooth shape classification
End milling cutter can be divided into flat end milling cutter, circular end milling cutter and ball end milling cutter according to the shape of the bottom end teeth.
Flat end mill: The bottom is flat, suitable for processing planes, grooves, step surfaces and so on.
Arc head end mill: the bottom is arc, suitable for processing surface changes small, relatively flat area.
Ball end mill: the bottom is hemispherical, suitable for processing complex surfaces, such as molds, aviation parts, etc., can achieve better surface quality and shape accuracy.
Third, according to the cutting edge shape classification
According to the shape and use of the cutting edge, the end mill can also be divided into universal type, cone type, tooth type, forming milling cutter and so on.
Universal type milling cutter: wide range of use, suitable for groove processing, side processing and step surface processing, etc., in rough processing, semi-finishing and finishing can be used.
Cone milling cutter: used for cone processing after ordinary edge processing, such as die inclination processing and concave part processing.
Tooth type milling cutter: the blade is waveform, the chip is small, the cutting force is small, suitable for roughing, but not for finishing.
Molding cutter: molding cutter for machining outer R, the edge of which is processed into a shape consistent with the processed object, and the special shape is usually customized according to the shape and size of the product.
Fourth, classification by blade
According to the connection between the blade and the cutter body, the end mill can be divided into integral, welded, indexable and so on.
Integral end mill: the cutting edge part and the handle part are made of the same material, good rigidity, suitable for finishing. Commonly used manufacturing materials are high speed steel and carbide.
High-speed steel end mill: high toughness, not easy to lose, the price is relatively cheap, but the processing efficiency is lower than the carbide end mill, not suitable for processing high hardness of the workpiece.
Carbide end mill: high hardness, good wear resistance, high processing efficiency, suitable for processing high hardness of the workpiece.
Welded end mill: welded carbide blade or CBN, PCD, etc., on the cutter body, suitable for large diameter, all the use of cemented carbide or PCD manufacturing cost is higher.
Indexable blade end mill: by clamping screws or pressure plates to fix the blade, when the blade wear or damage, just replace the blade can be used again, with high economy. Mainly used for roughing and semi-finishing.
Fifth, according to other characteristics of classification
Classification by spiral Angle: the spiral Angle of the end mill is generally about 30°, and the size of the spiral Angle affects the sharpness of the cutting and chip removal performance. The smaller the spiral Angle, the worse the cutting sharpness; The larger the spiral Angle, the better the cutting sharpness, but it may lead to an increase in the force of the end mill in the exit direction, causing dislocation.
Classification by cutting edge length: the cutting edge length of the end mill is divided into ultra-short, short, medium, medium, long, long and other kinds of, the choice should be determined according to the depth of processing and workpiece shape and other factors.
Classification according to the shape of the tool handle: the shape and variety of the tool handle, such as flat straight handle, composite long handle, etc., suitable for different machine tools and clamping methods.
According to the structure of the knife neck classification: the design of the knife neck has standard type, long neck type, cone neck type, etc., which needs to be selected according to the depth of processing and the shape of the workpiece. Cone-neck end mills provide better rigidity and machining accuracy.
Sixth, special type end mill
T-slot milling cutter: used to process the workpiece with T-slot shape, often used in the T-guide rail and T-slot accessories of the machine tool.
Keyway milling cutter: there are two cutter teeth, the cylinder and the end face have cutting edges, the end edge extends to the center, both like an end mill and like a drill. When machining, the groove depth is reached by axial feed first, and then the whole length of the keyway is milled out along the direction of the keyway.
Drum milling cutter: The cutting edge is distributed on the circular surface of the radius R, and the end face has no cutting edge, which is suitable for processing the variable bevel Angle of the parts.
Sum up
There are many types of end milling cutter, and the selection needs to be considered according to the material, shape, processing requirements and the performance of the machine tool. The right choice can greatly improve the processing efficiency, reduce costs, and ensure the quality of processing.