End mills are the most commonly used milling cutters on CNC machine tools, and their characteristics can be summarized as follows:
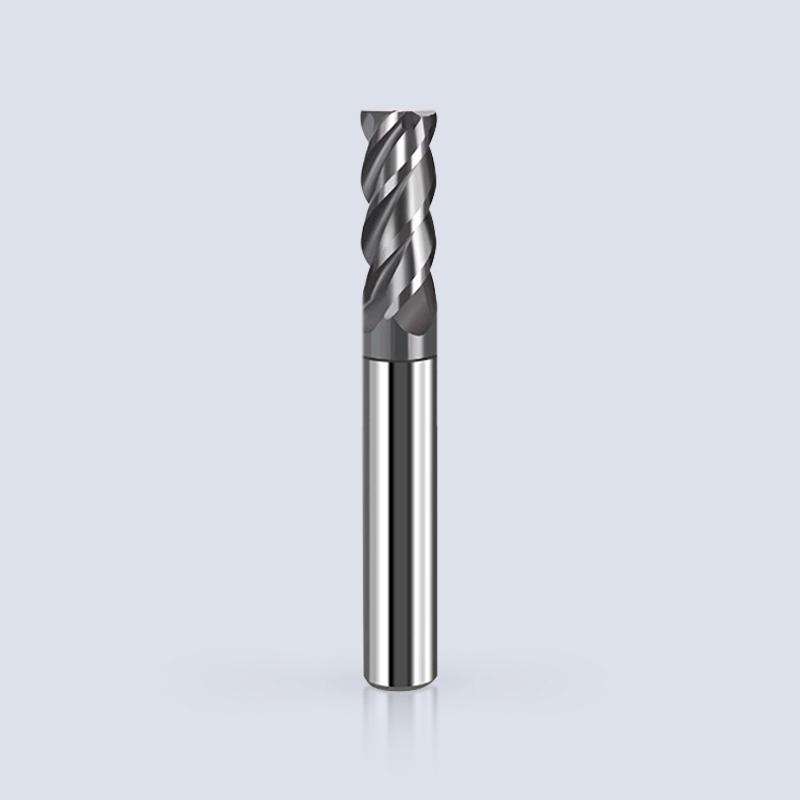
First, structural characteristics
Main cutting edge and secondary cutting edge: The main cutting edge of the end mill is located on the cylindrical surface, and the cutting edge on the end face is the secondary cutting edge. This structure allows the end mill to cut simultaneously or individually.
No center edge: The end mill has no center edge, so it cannot feed along the axial direction of the milling cutter during operation.
Helix angle: The helix angle of the end mill has an important influence on the cutting performance. The larger the helix angle, the longer the contact line between the workpiece and the blade, and the smaller the load on the blade per unit length, which is conducive to extending the tool life. But on the other hand, the increase in the helix angle will also increase the axial component of the cutting resistance, which may cause the tool to fall off the tool holder. Therefore, when using a tool with a large helix angle, the tool holder must have good rigidity.
Core thickness: The core thickness is an important factor in determining the rigidity and chip groove of the end mill. The core thickness of the overall end mill is generally 60% of the outer diameter. As the core thickness increases, the rigidity increases, but the chip groove decreases, and the chip removal performance deteriorates; conversely, as the core thickness decreases, the rigidity decreases, but the chip removal performance increases.
Second, functional characteristics
Wide range of applications: End mills are mainly used for plane milling, groove milling, step face milling and profile milling, etc.
High cutting efficiency: The main cutting edge and the secondary cutting edge of the end mill can be cut at the same time, which improves the processing efficiency.
Few tool inventory varieties: End mills can be used for face milling, reducing the tool inventory varieties.
Third, precautions for use
Not suitable for milling of planes without steps: Since the main deflection angle of the end mill is 90°, the force on the tool is mainly radial force in addition to the main cutting force, which easily causes the tool bar to bend and vibrate, affecting the processing efficiency. Therefore, except in special circumstances, it is generally not recommended to use end mills to process planes without steps.
Pay attention to the clamping force of the tool holder: During the milling process, the end mill may sometimes gradually extend from the tool holder or even fall off completely. This is usually due to the oil film between the inner hole of the tool holder and the outer diameter of the end mill shank, resulting in insufficient clamping force. Therefore, when using the end mill, you need to pay attention to the clamping force of the tool holder.
Prevent vibration: There is a small gap between the end mill and the tool holder, and vibration may occur during the processing. Vibration will affect the processing accuracy and tool life, so measures should be taken to prevent vibration, such as reducing the cutting speed and feed speed, and increasing the rigidity of the tool system.
Fourth, material and coating
Material progress: In the past, high-speed steel integral end mills were commonly used. Now, with the advancement of coating technology and tool material technology, coated carbide integral end mills and indexable end mills have gradually become popular and widely used in mold processing, high-hardness material processing and other fields.
Coating effect: The coating not only maintains the strength and toughness of the tool body, but also improves the surface hardness and wear resistance, which helps to extend the tool life and improve processing efficiency.
In summary, end mills play an important role in machining with their unique structure and functional characteristics. However, some issues should be paid attention to during use to ensure machining quality and efficiency.