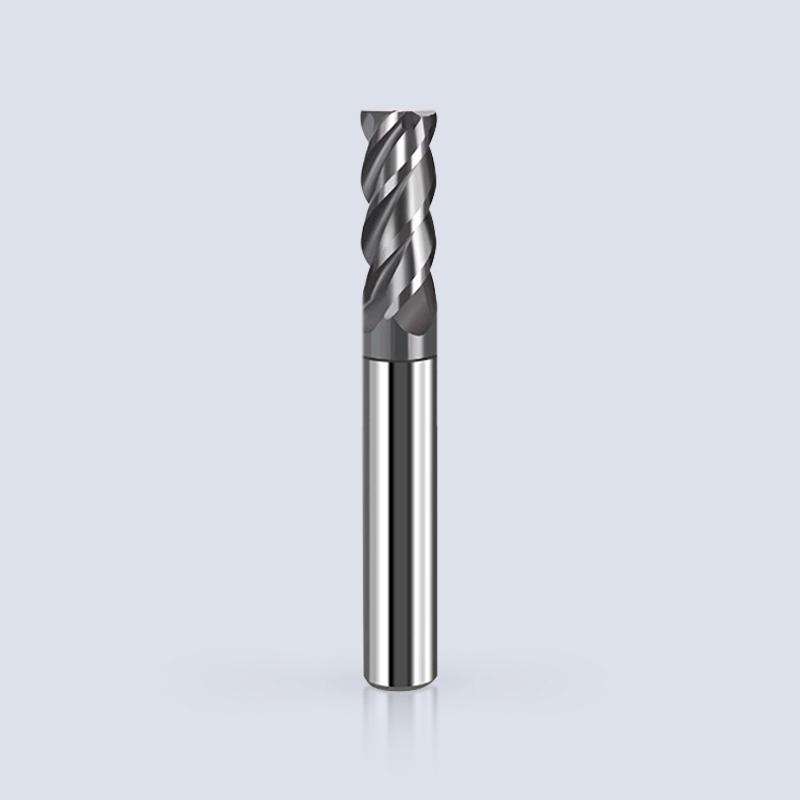
When choosing an end mill, you need to consider several factors to ensure that you get the most suitable tool. Here are some key considerations:
1. Processing requirements:
Processing materials: Different materials require different types of tools. For example, when processing metal materials, you need to choose a tool with high wear resistance; when processing plastic materials, you need to choose a tool with a sharper edge.
Processing accuracy: If high-precision processing is required, you need to choose an end mill with high tool accuracy.
Processing surface quality: If you need to obtain good processing surface quality, you need to choose an end mill with a sharper edge and good chip removal performance.
2. Tool size:
Tool diameter: The tool diameter should be selected according to the size and shape of the processed part. Generally speaking, the larger the tool diameter, the higher the processing efficiency, but the lower the tool rigidity.
Tool length: The tool length should be selected according to the depth of the processed part. Generally speaking, the longer the tool length, the deeper the processing depth, but the lower the tool rigidity. Therefore, choosing the shortest length can greatly increase the stability of the tool.
3. Tool Material:
The two most common materials used to make end mills are high-speed steel (HSS) and carbide. HSS is suitable for older, slower or less rigid machines and one-off or very short-run production. It will run slower but is cheaper, less brittle and more tolerant of unstable conditions. Carbide is preferred in CNC machines that require higher speeds, fewer tool changes and higher productivity.
4. Number of Flutes:
Flutes are spiral grooves that go around the side of the end mill. A smaller number of flutes (such as a 2-3 flute tool) will provide more flute space for long-chip materials (such as aluminum). More flutes reduce flute space but can increase productivity for shorter-chip materials (such as medium-carbon to high-carbon steel and iron). For steel, stainless steel, high-temperature alloys and iron, four-flute end mills are the first choice for grooving applications.
5. Type of Coating:
Coatings help reduce friction and protect carbide from the heat generated during cutting. Choose the type of tool coating based on the type and hardness of the workpiece being machined. For example, when processing workpieces with hardness below HRC40 such as carbon steel, BWTiALN coating can be selected; when processing workpieces with hardness around HRC50 such as alloy steel S and tool steel, NanoTiAlN coating can be selected; when processing workpieces with higher hardness, the tool shape, carbide material, and coating can be selected for high-hardness processing coatings dedicated to processing high-hardness materials.
6. Tool geometry:
Neck shape: The neck shape of the end mill is divided into standard type, long neck type and tapered neck type. It can be selected according to relevant conditions such as the processing depth, shape appearance, and three milling paths of the rough, medium and fine processing objects of the workpiece. The long neck type and tapered neck type can be used for deep excavation processing, and the interference angle should be considered when choosing between the two. Compared with the long neck type, the tapered neck type end mill has high rigidity, which can improve cutting conditions and achieve better processing accuracy, so the tapered neck type end mill should be selected as much as possible.
Ball head accuracy: According to the processing accuracy and the surface fineness of the workpiece, end mills with different ball head accuracy and smooth cutting edges are selected. The arc accuracy of ball-end mills is usually ±5μm, but there are also high-precision end mills with ±2~3μm, which can be selected when high-precision machining is performed.
7. Tool cost:
The cheaper the better. If you have high production and heavy workloads, it is crucial to invest in the right tools that can keep up with the workload. Choosing cheap or inappropriate tools will cost time and money due to material waste, scrap, tool waste, and increased wear on CNC machines.
In summary, when purchasing end mills, you need to consider multiple factors such as processing requirements, tool size, material, coating, geometry, and cost. Through careful evaluation and selection, you can ensure that you purchase the most suitable end mill, thereby improving processing efficiency and quality.