Stainless steel is widely used in medical devices, food machinery, and precision components due to its corrosion resistance and high strength. However, its machinability is significantly more challenging than ordinary steel. Characteristics such as high toughness, strong adhesion, and poor thermal conductivity often lead to rapid tool wear and subpar surface quality. Leveraging years of R&D experience, SDFTools has developed a carbide tool solution specifically for stainless steel machining to help overcome these challenges.
I. Four Major Challenges in Stainless Steel Machining
1. High Toughness and Adhesion
Stainless steel (e.g., austenitic grades 304/316) contains high levels of Cr, Ni, and other elements, resulting in exceptional plasticity and toughness. During cutting, chips tend to adhere to the tool’s rake face under high temperature and pressure, forming built-up edges (BUE). These BUEs alter the tool’s effective geometry, causing fluctuations in cutting forces and dimensional inaccuracies.
2. Poor Thermal Conductivity
The thermal conductivity of stainless steel is only 1/4 to 1/2 that of carbon steel. Heat generated during cutting is difficult to dissipate, leading to localized cutting edge temperatures exceeding 700°C. This can cause tool material annealing or diffusion wear.
3. Work Hardening Tendency
Austenitic stainless steel is prone to martensitic transformation under cutting stress, resulting in a hardened surface layer with a 30%–50% increase in hardness and a depth of 0.1–0.3 mm. This accelerates flank wear.
4. Difficulty in Chip Breaking
The high toughness of stainless steel chips often leads to the formation of continuous spiral or ribbon-like chips, which can entangle the tool or workpiece, causing machine downtime or even safety hazards.
II. SDFTools Carbide Tool Solutions
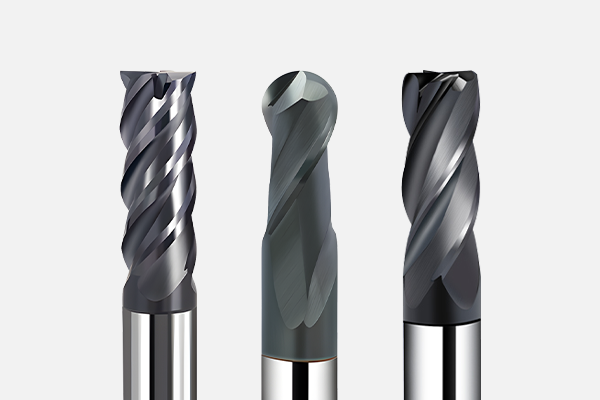
1. Specialized Carbide Tools for Stainless Steel
The G-SUS milling cutter, featuring ultra-fine grain carbide, combines high hardness (HRA 90) with superior toughness (25% improved crack resistance). It effectively addresses issues like material adhesion and crater wear, making it ideal for long-chip machining of heat-resistant alloy steels.
2. Optimized AlTiN Coating Technology
Stainless steel machining presents challenges such as rapid tool wear, short tool life, high friction, and BUE formation. SDFTools’ AlTiN-based PVD coating technology delivers outstanding results:
- Coating hardness reaches HV 3200, significantly reducing tool wear and extending tool life by 3× compared to standard coatings.
- Friction coefficient is reduced to 0.3, minimizing friction and suppressing BUE formation, effectively resolving key stainless steel machining challenges.
3. Precision Adjustment of Cutting Parameters
Roughing Parameters
- Cutting Speed (Vc)
- Range: 60–120 m/min (or 200–400 SFM)
- Example: For a 12 mm diameter cutter, RPM = (Vc × 1000) / (π × diameter) ≈ (80 × 1000) / (3.14 × 12) ≈ 2123 RPM (adjust based on machine capability).
- Feed per Tooth (Fz)
- Range: 0.05–0.15 mm/tooth
- Example: For a 4-flute cutter at 700 RPM, feed rate (F) = 0.1 × 4 × 700 = 280 mm/min.
- Cutting Depth
- Axial Depth of Cut (Ap): 0.5–2× tool diameter (e.g., 6–24 mm for a 12 mm tool).
- Radial Depth of Cut (Ae): 30%–50% of tool diameter (e.g., 3.6–6 mm for a 12 mm tool).
- Cooling and Lubrication
- Continuous cooling is essential to prevent thermal deformation.
Finishing Parameters
- Cutting Speed (Vc)
- Range: 80–160 m/min (or 260–500 SFM)
- Example: For the same 12 mm cutter at Vc = 120 m/min, RPM ≈ 3185.
- Feed per Tooth (Fz)
- Range: 0.03–0.08 mm/tooth
- Example: For a 4-flute cutter at 2000 RPM, F = 0.05 × 4 × 2000 = 400 mm/min.
- Cutting Depth
- Axial Depth of Cut (Ap): 0.1–0.5 mm (to ensure surface finish).
- Radial Depth of Cut (Ae): 5%–10% of tool diameter (or full-edge cutting).
- Cooling and Lubrication
- Continuous cooling is required to avoid thermal deformation.
Key Points: Avoid low cutting speeds (<60 m/min) to prevent cold welding; use appropriate cooling methods for rapid heat dissipation.
4. Tool Geometry Design
Large Rake Angle (15°–20°):
The tool features a 15°–20° rake angle design. A larger rake angle reduces cutting forces, ensures smoother cutting, minimizes deformation, and suppresses BUE formation, thereby improving surface quality and machining efficiency.
Sharp Cutting Edge + Micro-Blunting Treatment:
SDFTools’ cutting edges undergo professional blunting. This maintains sharpness for easy material penetration while enhancing edge strength to resist chipping. This balance ensures stable, efficient cutting and extends tool life.
Chip Breaker Design:
The chip breaker is specially engineered for stainless steel. Its unique design forces chips to curl and break, preventing long chips from entangling the tool or scratching finished surfaces. This improves machining safety and quality.
5. Cooling and Lubrication Strategies
Oil-Based Cutting Fluids:
Synthetic oils with extreme pressure (EP) additives reduce friction between the tool and workpiece, enhancing efficiency and surface quality.
Minimum Quantity Lubrication (MQL):
Ideal for high-speed machining, MQL precisely controls lubricant spray volume, minimizing thermal shock to tool coatings and extending tool life.