When using CNC end mills in machining, especially for complex workpieces, several precautions should be taken to ensure optimal performance and safety. Here are the key points to consider:
I. Precautions When Milling Complex Workpieces
1. Clamping of the End Mill
- Spring Collet Clamping: Most end mills used in machining are clamped with a spring collet, which is in a cantilevered state during operation. During milling, the end mill may gradually extend out of the collet or even fall out entirely, leading to the scrapping of the workpiece. This is usually due to an oil film between the collet’s inner hole and the end mill’s shank, resulting in insufficient clamping force.
- Cleaning Requirements: End mills are typically coated with rust preventive oil when they leave the factory. If non-water-soluble cutting oil is used during machining, a misty oil film can also adhere to the collet’s inner hole. Therefore, before clamping, the end mill shank and the collet’s inner hole should be cleaned with a cleaning solution and dried thoroughly.
- Large Diameter End Mills: For larger diameter end mills, even if the shank and collet are clean, drop-out accidents can still occur. In such cases, it is recommended to use a collet with a flattened notch and a corresponding side-locking mechanism.
- Collet Wear: If the collet has been used for a long time, its end may wear into a conical shape, making it difficult to clamp the end mill securely. In this case, a new collet should be replaced.
2. Vibration of the End Mill
- Micro Gaps: Due to the micro gaps between the end mill and the collet, vibrations may occur during machining, leading to uneven cutting and increased chip load, which can affect machining accuracy and tool life.
- Controlling Amplitude: If intentional vibration is used to achieve the desired slot width, the maximum amplitude of the end mill should be limited to 0.02mm or less to ensure stable cutting.
- Reducing Vibration: To reduce vibration, lower the cutting speed and feed rate. If significant vibration persists after reducing both by 40%, consider reducing the depth of cut. Resonance can be caused by factors such as excessive cutting speed, low feed rate, insufficient tool system rigidity, inadequate workpiece clamping, and workpiece geometry. Adjust the cutting parameters, increase tool system rigidity, and increase the feed rate as needed.
3. End Cutting of the End Mill
- Extended Length: In CNC milling of molds and other workpiece cavities, when machining recessed or deep areas, the end mill’s overhang length must be increased. Long-fluted end mills are more prone to vibration and breakage due to their flexibility. It is advisable to use a short-fluted, long-shanked end mill when only the end cutting edges are needed.
- Horizontal CNC Machines: When using large-diameter end mills on horizontal CNC machines, the weight of the tool can cause significant deflection. Extra caution should be taken with end cutting. If long-fluted end mills are necessary, significantly reduce the cutting speed and feed rate.
4. Selection of Cutting Parameters
- Cutting Speed: The selection of cutting speed primarily depends on the material of the workpiece.
- Feed Rate: The feed rate is determined by the material of the workpiece and the diameter of the end mill.
- Reference Tables: Some tool manufacturers provide cutting parameter selection tables, which can be used as a reference. However, the actual selection should be adjusted based on the specific conditions of the machine, tool system, workpiece shape, and clamping method.
- Prioritizing Tool Life: If tool life is a priority, reduce the cutting speed and feed rate. If the chip evacuation is poor, increase the cutting speed.
5. Choice of Cutting Method
- Climb Milling: Climb milling helps prevent tool edge damage and extends tool life. However, two points need to be noted:
- On conventional machines, eliminate any play in the feed mechanism.
- Use conventional milling (up-milling) when the workpiece surface has an oxide layer or other hardened layers from casting or forging processes.
6. Use of Carbide End Mills
- High-Speed Steel (HSS) vs. Carbide: HSS end mills have a wider range of applications and are more forgiving of slight deviations in cutting conditions. Carbide end mills, while highly wear-resistant at high speeds, have a narrower range of applications and require strict adherence to specified cutting conditions.
II. Fault Diagnosis Methods for CNC Milling Machines
Visual Inspection
- Visual Check: Carefully inspect for burned fuses, damaged components, and open circuits. Also, check for bent or wobbling transmission shafts in the mechanical parts.
- Auditory Check: Listen for abnormal sounds from the CNC machine, such as squeaking from loose or corroded transformer cores, buzzing from relays and contactors with large magnetic circuit gaps, and mechanical friction, vibration, and impact noises.
III. Preparations Before Operating a CNC Drill and Milling Machine
Preparation Steps
- Familiarize with the Machine: Understand the general performance, structure, transmission principles, and control programs of the CNC drill and milling machine. Master the functions and operating procedures of all buttons and indicator lights. Do not operate or adjust the machine until you fully understand the entire process.
- Pre-Operation Checks: Before starting the machine, check the electrical control system, lubrication system, and oil quality. Ensure that all operating handles are in the correct position and that the workpiece, fixtures, and tools are securely clamped. Check the coolant level, then run the machine at a slow speed for 3-5 minutes to verify that all transmission components are functioning normally. Only proceed with normal operation once no faults are detected.
- Program Debugging: After completing program debugging, obtain approval from the instructor before proceeding step-by-step. Do not skip any steps.
- Check Origin and Tool Data: Before machining parts, strictly check the machine origin and tool data, and perform a dry run simulation without cutting.
IV. Precautions for Using Fixed Cycle Functions on CNC Drill and Milling Machines
- Spindle Rotation: Before initiating a fixed cycle, use auxiliary functions to rotate the spindle (e.g., M03 for clockwise rotation). If the spindle stop command (M05) is used, ensure the spindle is re-rotated before continuing with the fixed cycle.
- Coordinate Data: In fixed cycle mode, the program segment must include X, Y, Z (including R) coordinate data; otherwise, the fixed cycle will not execute.
- Canceling Fixed Cycles: Besides G80, G00, G01, G02, and G03 can also cancel fixed cycles. Be mindful of this during programming.
- Tool Length Compensation: In fixed cycle mode, C43 and C44 still function as tool length compensation commands.
- Mid-Cycle Interruption: If the CNC machine is stopped mid-cycle using a reset or emergency stop, the hole machining mode and data are still stored. When resuming, pay special attention to complete the remaining actions of the fixed cycle.
Formatting Instructions:
- Headings: Use a font size of 24px for main headings (e.g., “Precautions for Using CNC End Mills in Machining”).
- Subheadings: Use a font size of 20px for subheadings (e.g., “I. Precautions When Milling Complex Workpieces”).
- Bullets and Text: Use a font size of 16px for bullet points and regular text.
- Bold: Bold important terms or actions, such as “Spring Collet Clamping” and “Cleaning Requirements”.
- Spacing: Ensure there is a line break between each section and after each bullet point for readability.
This format should make the content more visually appealing and easier to read when you copy it to a webpage. If you need further adjustments or specific CSS styles, let me know!
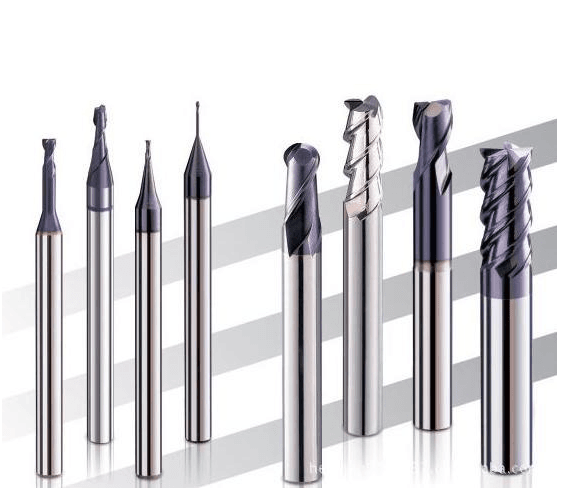