End milling cutter is one of the most widely used milling cutter on CNC machine tools, and there are many types, which need to be selected according to the specific processing needs. The following are the introduction and selection suggestions of the opposite type of milling cutter:
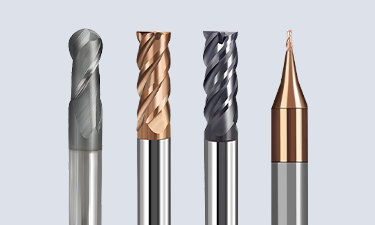
The main type of end mill
Integral end mill:
Features: The cutting edge part and the handle part are made of the same material, usually using carbide or high-speed steel.
Application: The integral end mill has good rigidity and is suitable for finishing.
Welded end mill:
Features: Welded carbide blade or CBN, PCD, etc., on the cutter body.
Application: Suitable for large diameter end milling cutter, low cost, but relatively poor rigidity.
Indexable blade end mill:
Features: The blade is fixed by clamping screws or pressure plates, and only needs to be replaced when the blade is worn or damaged.
Application: Suitable for roughing and semi-finishing, with high economy.
Classification by end cutting edge:
Through the center edge end mill: direct axial feed.
But center edge end mill: suitable for side feed.
Classification by spiral Angle:
Common spiral Angle: 30°, 40°, 60°, etc.
Features: The larger the spiral Angle, the better the cutting sharpness, but the chip removal performance may become worse; The smaller the spiral Angle, the better the chip removal performance, but the cutting sharpness may be insufficient.
Special type end mill:
Waveform end mill: can turn long thin chips into thick and short chips, smooth chip removal, large cutting thickness, long tool life.
Ball end mill: The milling head is ball-shaped, which is suitable for machining the surface of the workpiece with curved shape and high processing accuracy.
Side milling cutter: The cutting edge is arranged along the side of the milling cutter, which is suitable for machining the workpiece with narrow shape or the need to cut the side.
T-slot milling cutter: Used for machining T-slot shaped workpieces.
Face milling cutter: The cutting edge is arranged along the surface of the milling cutter, which is suitable for machining a large area of the workpiece surface.
Suggestions for the selection of end milling cutter
According to the material selection of the workpiece:
Lower hardness of the workpiece: such as aluminum alloy, you can choose high-speed steel end milling cutter or special aluminum milling cutter.
High hardness of the workpiece: such as hardened steel, stainless steel, etc., should choose carbide end milling cutter, and consider the use of appropriate coatings (such as TiCN, TiAlN, etc.) to improve tool life.
Select according to the processing form and accuracy requirements:
Surface machining: Choose a flat end mill or a rounded end mill.
Surface machining: Select ball end mill.
High precision machining: Select a high precision end mill, such as a ball end mill with an arc accuracy of ±5μm or less.
According to the depth of processing and workpiece shape selection:
Large machining depth: Choose a long neck or cone neck end mill.
The workpiece shape is complex: choose a flexible end mill, such as indexable blade end mill.
According to the number of cutting edges and spiral Angle selection:
Number of cutting edges: the more the number of cutting edges, the better the rigidity, but the chip removal performance may become worse; The fewer the number of blades, the better the chip removal performance, but the rigidity may be insufficient.
Helix Angle: Select the right helix Angle according to the machining material and cutting conditions to obtain the best cutting performance.
Based on processing efficiency and cost:
Roughing: Choose an end mill with good chip removal performance and good rigidity, such as a large spiral Angle end mill.
Finishing: Select end mills with high precision and good surface quality, such as integral end mills or high-precision ball end mills.
Consider the cost: under the premise of ensuring the processing quality, choose the cost-effective end mill.
Other points to note:
Tool length: On the premise of meeting the processing needs, try to choose a shorter end mill to improve the stability and processing quality of the tool.
Tool coating: Choosing the right coating can improve the wear resistance, heat resistance and lubrication of the tool, thereby extending the tool life.
In summary, the choice of end milling cutter is a comprehensive consideration process, which needs to be determined according to the specific processing needs. By selecting the type and parameters of end milling cutter reasonably, the machining efficiency can be improved, the machining quality can be guaranteed and the machining cost can be reduced.