In this content, Shengdefu Tools shares SECO’s latest solution in the field of high-temperature alloy machining – end mills. Thanks to revolutionary technological breakthroughs, these tools can increase the machining speed of high-temperature alloys by up to 40 times. The live event was very lively, with online users showing great interest in the cutting-edge solutions shared by Shengdefu and actively participating in the interaction. Therefore, we have selected some representative questions and provided answers for your reference.end mill
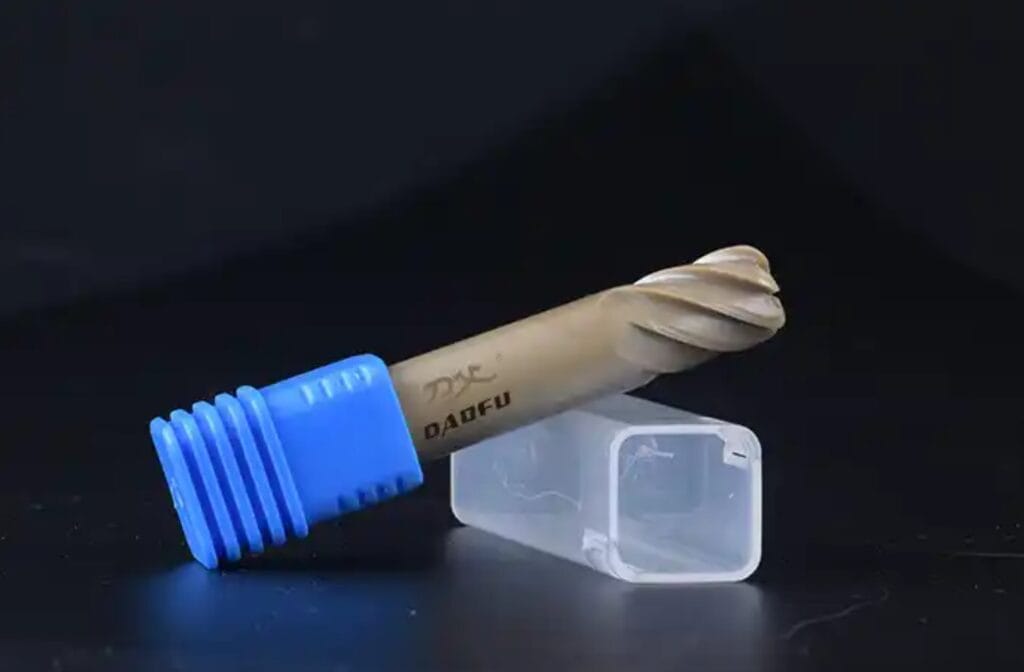
JCG790 Ceramic End Mill
- Q: What are the advantages of SECO ceramic tools in interrupted cutting compared to peers?
- A: Ceramic + cemented carbide, better toughness
- Q: What is the linear speed of the ceramic end mill? How is the overall cost-effectiveness?
- A: 350-1500 m/min
- Q: We are now encountering new materials such as titanium aluminum alloys. Is this type of material suitable for ceramic machining, for example, titanium alloys?
- A: Titanium alloys are not recommended for ceramic end mills
- Q: Are ceramic end mills suitable for cutting fluids?
- A: No, they are not suitable
- Q: Which is more appropriate, water cooling or oil cooling?
- A: Dry cutting is recommended
- Q: What are the requirements for the machine tool when using ceramic tools?
- A: The spindle speed of the machine tool must be high
- Q: How does the machining speed of high-temperature alloys increase by 40 times?
- A: Cemented carbide linear speed is 20-30 m/min, while ceramic can reach 1200 m/min
- Q: What are the advantages of ceramic end mills in terms of tool adhesion during machining?
- A: Increasing the linear speed can improve chip adhesion issues
- Q: How is the overall cost-effectiveness? Can it be used for finishing besides roughing? How is the overall cost-effectiveness?
- A: Only for roughing
- Q: If a ceramic tool breaks, can it be repaired? How?
- A: Repair is not recommended
- Q: Where are the ceramic tools produced? What is the delivery lead time?
- A: Standard products, in stock
- Q: Are hydraulic chucks suitable for finishing, but not for roughing?
- A: The cutting force of ceramic end mills is not large, so hydraulic chucks are fine
- Q: Will the material harden after milling?
- A: Yes, but relatively less
- Q: Can plunge milling be done?
- A: Chip evacuation may be problematic, not recommended
- Q: Is the cutting depth half the diameter of the tool?
- A: 0.05 times the diameter, half is not allowed
- Q: Are ceramic end mills suitable for machining blisks? What is the maximum slope milling depth for a 12mm ceramic end mill? Does the slot width change significantly after rough milling with a 12mm ceramic end mill?
- A: Suitable for blisk machining; the slope angle can be 0.5 degrees; the slot width change is not significant, mainly consider burrs and material changes
- Q: What machining methods are typically used for ceramic tools? If the linear speed is reduced, will the tool life increase?
- A: Side milling or high feed milling; reducing the linear speed does not necessarily increase the life, and if too low, it may cause more breakage
- Q: How to reduce or eliminate work hardening during machining?
- A: Reduce the number of passes
- Q: How to avoid tool breakage when machining high-temperature alloy castings with ceramic tools?
- A: Better runout, higher precision, and vibration-damping properties
- Q: How effective are ceramic tools for machining stainless steel?
- A: Not recommended
- Q: Why is a high-precision ER collet preferred over a hydraulic chuck?
- A: High-precision ER collets are reliable, heat-resistant, and have some vibration-damping capabilities
- Q: After installing the tool, is there a requirement for tool runout? How many microns?
- A: 5 microns
- Q: What is the maximum cutting depth for slope milling?
- A: 0.5 degrees
Formatting Instructions:
- Headings: Use a font size of 24px for main headings (e.g., “Solving Cutting Vibration Issues: All You Need to Know!”).
- Subheadings: Use a font size of 20px for subheadings (e.g., “JCG790 Ceramic End Mill”).
- Questions and Answers: Use a font size of 16px for questions and answers.
- Bold: Bold important terms or actions, such as “Ceramic + cemented carbide, better toughness” and “Dry cutting is recommended”.
- Spacing: Ensure there is a line break between each question and answer for readability.
This format should make the content more visually appealing and easier to read when you copy it to a webpage. If you need further adjustments or specific CSS styles, let me know!