On the occasion of ANCA celebrating 50 years of advancements in tool manufacturing technology, Edmund Boland, the General Manager of ANCA CNC Machines (located in North Bayswater, Australia), with his forward-looking vision, reveals to us the blueprint for the cutting tool industry over the next 5 to 10 years.
Only One Person and a Dog?
The old story that future factories will have only one person and a dog—where the person’s job is merely to feed the dog, and the dog’s job is to keep the person away from the machines—will come close to reality in the field of tool grinding.
Mr. Boland states that the future tool manufacturing plants will be fully digitally connected, from the entry and storage of raw materials, through laser etching and blank preparation, to the grinding, edge honing, and coating of tools and cutters, all the way to the shipment of finished products. Each step will be precisely linked together. This comprehensive digitalization will bring unprecedented efficiency improvements. When work orders move from outer diameter pre-processing to five-axis grinders, the machines will automatically call up the correct programs to complete the tool grinding, with all information closely integrated with the company’s ERP and MES systems, providing precise data analysis to management, helping to make informed decisions and continuously optimize production processes.
It is an undeniable fact that once set up, individual processes such as cylindrical grinding or edge finishing are highly automated. In Mr. Boland’s view, the difference between companies lies in the degree of automation of these processes and the level of automation in material transfer between stations.
For small and medium-sized workshops, there might be a person responsible for moving pallets from the cylindrical grinder to the five-axis machine and scanning the pallets. But in terms of digitalization, the five-axis machine would receive a file indicating it is receiving those blanks, all of which is tied into the ERP system. The same applies to outsourced coatings, where information is sent digitally to the coating machine, but someone manually transfers the tools from the five-axis machine to the shipping department. In larger workshops, logistics carts would handle material movement. This is what ANCA Integrated Manufacturing System (AIMS) is about.
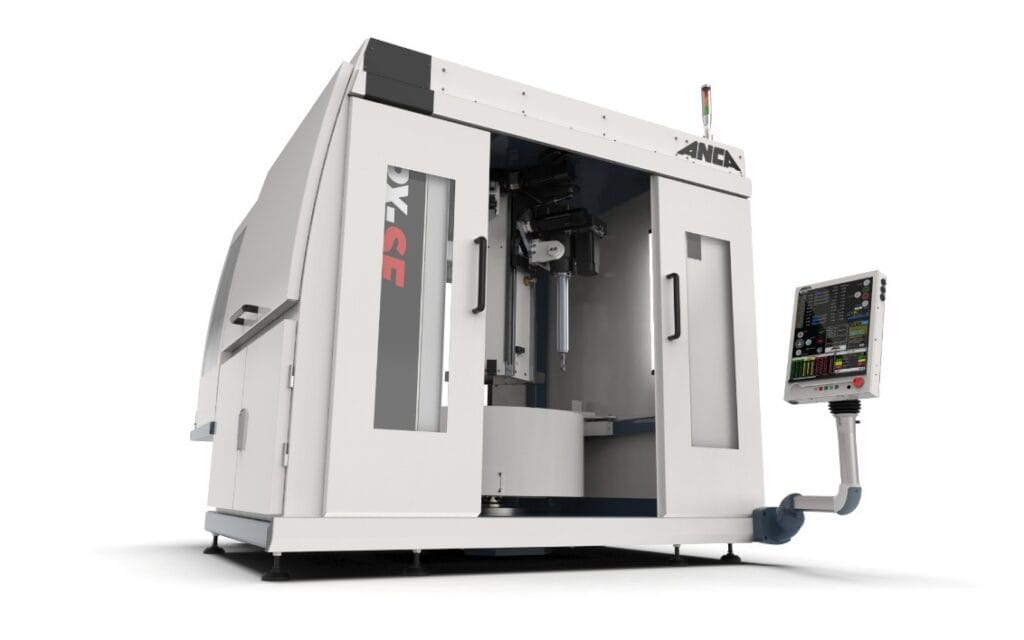
Improvement in Setup and Quality Mr. Boland says that as workshop automation increases, the quality of output becomes more stable, allowing workers to focus more on solving specific problems and optimizing the entire process with the help of artificial intelligence. There will always be some tools that exceed tolerance. At this point, someone needs to ask, “Why did this happen? What do we need to adjust? Is there a problem with a particular production step? Or is there an error in the program?”
Competitive companies will rely on a small group of highly skilled problem solvers. These individuals will continue to advance through advanced training provided by ANCA Academy.
Mr. Boland also believes that skilled machine installers will continue to play a role, though changes will occur in this area as well. “For example, technologies like automatic fixtures will be equipped with sensors and capable of self-adjustment.”
Mr. Boland adds that automatic compensation to correct errors found during processing has already become a reality, and this capability will only improve. For instance, with today’s technology, if the loaded blank is skewed, the probe will detect the error, and the grinding will automatically adjust to produce a satisfactory tool. However, “you still need to manually check the first piece, especially for new tools. After that, the system can take over. ‘Getting the first tool right’ has become our mantra. You should be able to measure the first tool, and if there’s an error, you can compensate for it.”
The increasing capabilities of in-machine measurement devices are one reason. Mr. Boland points out that their new generation of lasers can measure even in the presence of coolant mist or residual oil on the tool. Vision systems still require manual placement and removal, but “this will change. Compared to lasers, camera systems need better ventilation conditions, but there are solutions. Robots can blow out debris from the machine environment immediately after grinding. Or you could use a robot to introduce the camera from outside the machine.”
At the same time, the list of features that can be measured internally and compensated for automatically will continue to grow. Today, “measurable features include outer diameter, tool profile, and groove depth. In a short period, we will be able to do more. For example, threads inside thread mills or taps. K-edges or tooth clearance, as long as it can be measured within the system, it can be compensated for.”
Boland does not think we will completely abandon standalone measuring machines like the ZOLLER Genius, especially when measuring complex features. However, he expects that the interaction between these systems and tool grinders will improve.
He explains that the key is to establish standardized measurement protocols for specific geometric features. “Before these measurement protocols are established, the tool grinder cannot compensate for measurement deviations. Currently, ANCA has a standard method for simpler end mills and drills. But as we install AIMS systems across our customer base, we are also working with these customers to expand the range of measurements we can compensate for. For example, we are developing quite complex form tools and complex end mills.
Sub-micron Tolerances It’s no secret that tolerances are getting smaller. Boland says that achieving micron and sub-micron levels of precision will be key to breakthroughs in many application areas in the future. The demand for such precision, due to the advantages of these cutting tools, “will increase.” Whether it’s the surface finish of the machined part, the life of the tool, or other factors, eliminating all minor errors within the cutting tool can significantly enhance its performance.
This is also why the market is increasingly favoring solid rotary tools over indexable tools. Boland says, “Customers need the rigidity of solid rotary tools, which is beneficial for tool transmission, while also achieving excellent surface finishes.”
“Maintaining higher levels of precision requires not just the high-functioning automation, in-process measurement, and closed-loop compensation mentioned earlier,” Boland lists, “but also seemingly simple yet equally important factors, such as air conditioning, cooling filtration systems, and the type of grinding wheels chosen… All of these impact the final precision. So, it’s not just about the tools and the tool grinders, but the entire system around them.”
“Eliminating vibration is absolutely critical. It’s no longer acceptable to mount mist collectors directly on top of the machine. Cooling units inside the machine will become very important. If they vibrate, it will affect the precision. Therefore, central cooling systems and central mist collectors become a necessity.”
While Boland predicts a growing demand for higher-precision tools, he also sees a sustained demand for lower-cost tools. This, along with the inherent cost and difficulty of meeting the tightest tolerances, will somewhat limit the full adoption of the improvements discussed above.
Material Trends Boland believes that cemented carbide remains the predominant material for cutting tools, but its dominance is being strongly challenged by PCD (Polycrystalline Diamond). It is expected that PCD’s market share may reach 30% within the next decade. Ceramics are also gaining attention, though they still represent a small portion.
Similarly, the demand for material removal techniques beyond grinding is also on the rise. Boland says that wire EDM and rotational EDM currently dominate in the PCD field, but laser ablation technology is also worth watching. “This is definitely an emerging technology. Customers with early machines are using it not only for PCD but also for cemented carbide, especially for micro-tools, where interesting results are being achieved by tool manufacturers.
“For PCD, laser ablation certainly has advantages over melting processes. It doesn’t require coolants or consumable copper electrodes.” Thus, although the cost of the machines may still be 40-50% higher than competing technologies, they may save costs over time due to lower consumables. Laser ablation can also create shapes and surface features that erosion cannot. Conversely, for larger-diameter tools, laser ablation makes less sense. So, Boland remains uncertain whether laser ablation will become a mainstream solution in the short term.
Similarly, additive manufacturing is unlikely to replace some material removal applications in industry. And its applicability to cutting tool production seems limited. “I don’t think it will become efficient enough within ten years. But it could find a place in the production of special tools, such as those with internal coolant channels. It could also play a role in making large, expensive cutting tools. But even if it were widely adopted, I don’t believe its precision would be sufficient to replace finishing.”
Other Market Considerations Regarding productivity, although automation solutions might lead some to believe that fine grinding technology will gradually disappear, Boland points out that regrinding will remain a viable business. This is because regrinding not only enhances productivity but also aligns with sustainability principles.
Forward-thinking tool producers are achieving greater productivity, which is driving an increasing demand for quick turnaround times. This trend applies not only to mass production but also to small batches of specialized tools. Boland emphasizes that the ability to easily produce optimized special tools for specific jobs is crucial for customers.
While the development of electric vehicles has reduced the automotive industry’s demand for cutting tools by 50%, this varies globally, with the US lagging behind in EV adoption, providing a buffer for cutting tool manufacturers. “Applications outside the EV sector are also growing, which may serve as a counterbalance,” says Boland, but the overall impact of EVs will undoubtedly be significant.
On the path of technological development, the future is full of uncertainties. Will hydrogen replace electric vehicles? Will ultra-clean fuels make a comeback, giving internal combustion engines a new lease on life? These questions remain unanswered.
Changes in Service and Support Boland predicts that artificial intelligence will “become a great mechanism for improving productivity in the future.” By utilizing AI for predictive maintenance, companies can accurately forecast component failures, automatically order replacement parts, ensuring the stable operation of production lines. As a result, preventive maintenance becomes targeted and efficient, while ensuring almost seamless uptime.
Boland notes that with the proliferation of multi-machine automation systems, any downtime becomes intolerable. Therefore, the ability to provide rapid, round-the-clock service and support will become a key competitive differentiator. To achieve this, companies can leverage remote and predictive diagnostics to reduce the need for on-site service personnel.
Whatever the future holds, it will certainly be interesting. If Boland’s predictions are off, you can always count on your faithful canine companion.