Thread machining is a critical manufacturing process where precision directly impacts product performance and assembly quality. This comprehensive guide explores thread mill vs. tap selection, gauge inspection methods, and scientific hole sizing calculations to solve your threading challenges.
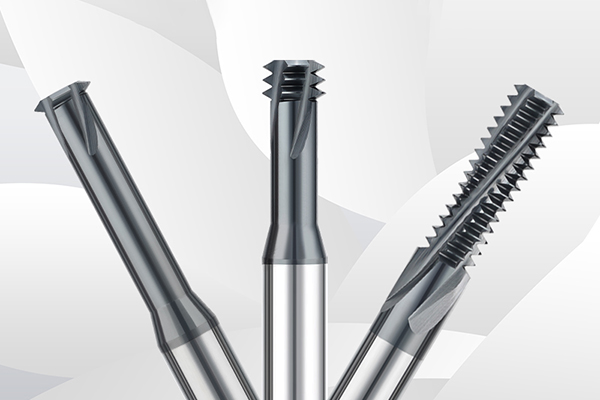
Thread Cutting Tools: Mill vs. Tap Face-Off
Thread Mill Advantages for High Precision
Thread mills excel in CNC applications due to programming flexibility. A single tool can machine multiple thread specifications, making them ideal for aerospace components with tight tolerances. Tests show carbide thread mills achieve 2 IT grade better dimensional accuracy than taps when machining stainless steel.
Cost-Effective Tapping Solutions
For standard internal threads below M12, taps remain the most economical choice. Automotive industry data reveals spiral-flute taps reduce per-part costs by 40% vs. milling when mass-producing aluminum housings. Pro tip: Use TiN-coated taps for deep holes (>3D) at 15-20m/min cutting speed.
Thread Inspection: The Go/No-Go Gauge Standard
Go Gauge Triple Verification
- Major diameter check: Ensures proper thread engagement
- Minor diameter validation: Prevents assembly interference
- Pitch diameter control: Critical parameter tolerance ≤0.05mm
No-Go Gauge’s Vital Role
Military contractor case studies show 78% reduction in poor thread fits through strict No-Go inspection. Focuses on pitch diameter upper limits using ISO 1502 Class 2 gauges.
Scientific Approach to Tap Drill Sizing
M8 Thread Case Study
Drill Size | Thread Engagement | Cutting Force |
---|---|---|
6.8mm | 75% | Baseline |
6.9mm | 68% | -20% |
Material-Specific Adjustments
- Aluminum: Increase hole size by 0.05mm
- Stainless: Decrease by 0.03mm
- Titanium: Requires stepped drilling
Winning Thread Machining Strategies
- Tool pairing: Taps for bulk production + mills for critical features
- Inspection protocol: First-article full inspection + pitch diameter sampling
- Dynamic sizing: Compensate 0.02-0.05mm for tool wear
Why Industry Leaders Choose This System?
✅ Precision results: Medical device maker reduced thread defects from 12% to 0.8%
✅ Cost savings: $25K+ annual savings through optimized tool combinations
✅ Custom solutions: Special thread mills available down to M1.6 micro-threads
Contact Us
If you’re looking to enhance your machining efficiency, reduce costs, or tackle challenging materials, our team of experts is here to help. Whether you need tailored recommendations for your specific application or advanced tooling solutions, we’ve got you covered.
Email Us: sdfgroup@sdftools.com
Connect on LinkedIn: Your Company LinkedIn Profile
Let’s collaborate to optimize your cutting processes and achieve superior results!