Why Do Cutting Tools Require Passivation Treatment?
In precision machining, newly sharpened tools appear flawless but contain microscopic defects invisible to the naked eye—such as edge burrs, serrated notches, and coating protrusions. These defects cause stress concentration during cutting, leading to edge chipping, vibration, and heat buildup, ultimately reducing tool life by 30%-50%. Passivation treatment refines the cutting edge at the micron level through mechanical, chemical, or composite processes, transforming sharp yet fragile edges into controlled rounded or chamfered structures, achieving a “blunt-to-sharp” technological upgrade. This article comprehensively explains how passivation treatment has become a key technology for modern tool performance enhancement.
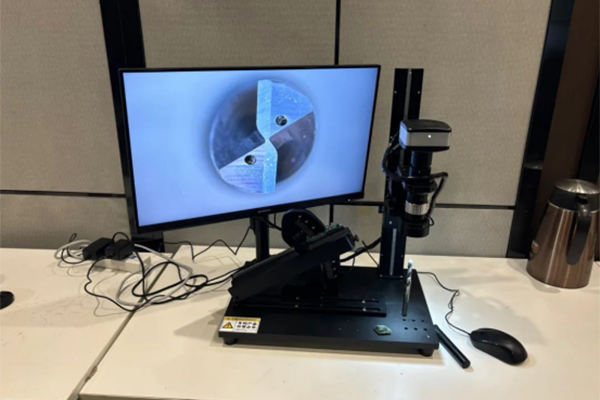
1. Primary Effects of Tool “Passivation”
1.1 Edge Rounding
Edge burrs cause tool wear and rough workpiece surfaces. After passivation, the edge becomes ultra-smooth, significantly reducing chipping and improving workpiece surface finish. Polishing the chip grooves enhances surface quality and chip evacuation.
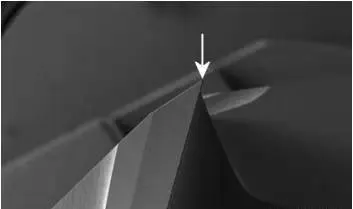
1.2 Polishing Treatment for the Chip Groove:
The smoother and more polished the groove surface, the better the chip evacuation performance, enabling higher-speed cutting. At the same time, the improved surface quality reduces the risk of the tool seizing or galling with the workpiece material. Additionally, it can reduce cutting forces by 40%, making the cutting process smoother and more efficient.
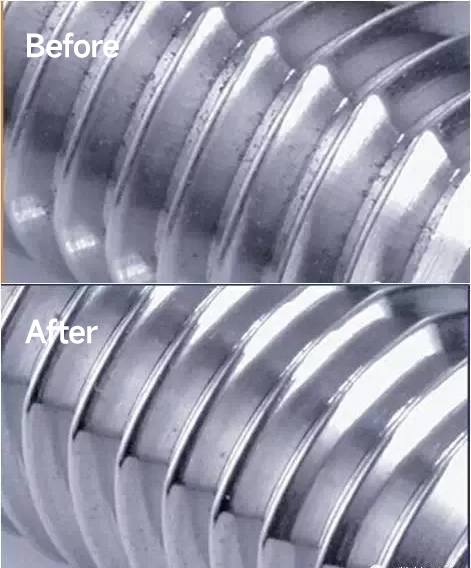
1.3 Coating Polishing
After coating, small protruding droplets may appear on the tool surface, which increase surface roughness. This causes greater frictional heat during cutting, thereby reducing cutting speed. After undergoing blunting and polishing , these droplets are removed, leaving behind numerous small pores. During machining, these pores can hold more cutting fluid, significantly reducing the heat generated during cutting and greatly improving the cutting speed.
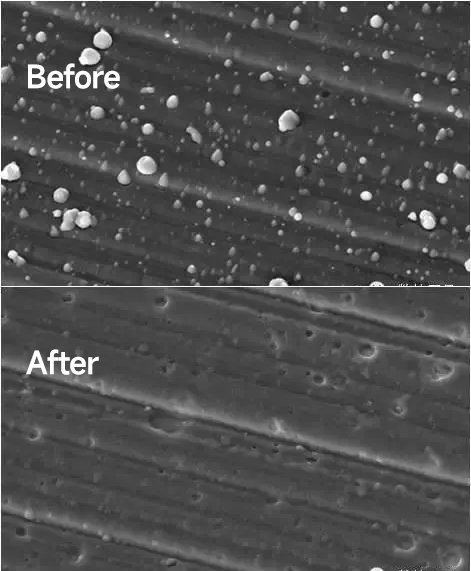
2. Five Core Benefits of Passivation Treatment
2.1 Eliminate Micro-Defects, Strengthen Edge Structure
Sharp cutting edges are prone to developing tiny cracks or chipping during use. Blunting treatment can eliminate these irregular microscopic edge imperfections, enhancing the overall strength of the tool and reducing the risk of edge chipping.
- Burr Removal : Sandblasting/grinding eliminates 0.5-2μm burrs, reducing chipping risks.
- Crack Repair : Seals micro-cracks, increasing carbide drill life from 500 to 2,000 holes.
- Coating Protection : Pre-passivation reduces coating delamination by 75%, enhancing TiAlN adhesion.
2.2 Optimize Thermal Management, Extend Tool Life
After blunting treatment, the cutting edge of the tool becomes more rounded, which reduces wear caused by stress concentration during the cutting process, thereby extending the tool’s service life.
- Surface roughness reduction (Ra0.8 → Ra0.2) lowers cutting temperatures by 15%-20%.
- Rounded edges increase chip contact paths, improving heat dissipation.
- Polished grooves reduce cutting forces by 40%.
2.3 Improve Machining Accuracy & Surface Quality
Tools that have undergone blunting treatment can reduce the surface roughness of the machined workpiece, improving its surface finish. This is particularly important for high-precision machining.
- Dimensional stability: Tolerance improves from ±0.02mm to ±0.005mm.
- Surface finish: Ra value optimizes from 1.6μm to 0.4μm.
- Burr height in aluminum machining drops from 0.15mm to <0.03mm.
2.4 Enhance Coating Functionality & Coolant Utilization
After the cutting edge is blunted, the friction during cutting is reduced, and the stability of the tool during the cutting process is improved, which helps to enhance machining efficiency.
- Pre-passivation boosts PVD coating adhesion by 60%.
- Nano-pores retain coolant for sustained lubrication.
- Polished coatings enable 20% faster cutting in superalloys.
2.5 Improve Machining Stability & Consistency
Tools that have undergone blunting treatment exhibit greater stability across different machining processes, which helps achieve consistent machining results.
- Vibration reduction: Cutting force fluctuation decreases by 50%.
- Batch tool consistency: Surface roughness deviation <10%.
3. Three Typical Passivation Strategies
3.1 General Passivation
- Dry sandblasting (220-grit alumina, 10-15s) for HSS tools.
- Wet grinding (diamond paste) for carbide tools, edge radius 15-25μm.
3.2 Coating-Specific Passivation
- Pre-passivation (5-8μm) prevents coating delamination.
- Post-coating polishing with diamond slurry removes droplets.
3.3 Specialty Material Machining
- Titanium alloys: 20-30μm edge radius with chipbreaker design.
- Graphite: 3-5μm ultra-fine passivation to prevent built-up edges.
4. Economic Validation of Passivation
Case study: Automotive engine block production line
- Tool life: 1.8h → 6.2h (+244%).
- Tool changes: 8 → 2 per shift (-75%).
- Defect rate: 2.3% → 0.5% (-78%).
5. Future Trends in Passivation Technology
- AI-Driven Passivation : Vision systems auto-adjust parameters.
- Multi-Layer Surface Engineering : Passivation + nitriding + coating.
- Nano-Passivation : Atomic layer deposition (ALD) for 1-5nm edge treatment.
Contact Us
If you’re looking to enhance your machining efficiency, reduce costs, or tackle challenging materials, our team of experts is here to help. Whether you need tailored recommendations for your specific application or advanced tooling solutions, we’ve got you covered.
Email Us: sdfgroup@sdftools.com
Connect on LinkedIn: Your Company LinkedIn Profile
Let’s collaborate to optimize your cutting processes and achieve superior results!