End mills are made of a variety of materials, each with its own unique properties and scope of application. Here are some common end mill materials and their introduction:
First, high-speed steel
Definition and characteristics: High speed steel is a type of steel containing higher alloying elements, with high hardness, rigidity and wear resistance.
Advantages: high machining accuracy, fast cutting speed, high cutting efficiency.
Disadvantages: fast wear, easy to generate heat sources and have a negative impact on the cutting effect.
Application scenario: Often used to make mass production end milling cutter, suitable for processing a variety of grooves and step surface and other rough processing.
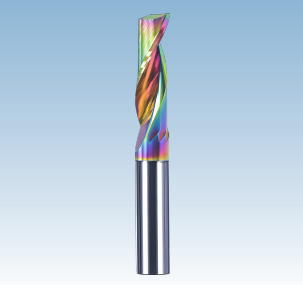
Second, cemented carbide
Definition and characteristics: Cemented carbide is made of tungsten, cobalt, titanium and other metal powder by mixing, pressing, sintering and other processes, with high hardness, high wear resistance, high strength and other characteristics.
Advantages: Can quickly cut high hardness materials, high wear resistance, can cut very hard materials.
Disadvantages: high cost, brittle quality, easy to break the tool in the case of rapid alternating cutting force.
Application scenario: It is one of the main materials for making high-quality end milling cutter, and is often used for processing difficult materials such as stainless steel and titanium alloy.
Third, ceramics
Definition and characteristics: Ceramics are increasingly used in the machining industry, especially in the areas of high-speed cutting and ultra-finishing. Ceramic end milling cutter has very good temperature resistance, durability and corrosion resistance.
Advantages: High cutting precision, temperature resistance, durability, corrosion resistance.
Disadvantages: high cost, high requirements for cutting conditions, not suitable for mass production.
Application scenario: Suitable for machining occasions requiring high precision and high cutting speed.
Fourth, other materials
Superhard materials: such as diamond coating or DLC coating and other processing of large front Angle, sharp cutting edge tools, suitable for processing brittle materials such as graphite.
Lightweight high-strength materials: such as aluminum, magnesium alloy, etc., are often used to manufacture indexable face milling cutter bodies to reduce tool weight and improve cutting efficiency.
Fifth, material selection considerations
When selecting end mill materials, the following factors need to be considered:
The hardness of the processing object: the workpiece with different hardness needs to choose the tool material with different hardness.
Material characteristics: such as thermal conductivity, work hardening, ductility, etc., these characteristics will affect the wear and cutting effect of the tool.
Cutting conditions: such as cutting speed, feed, depth of cutting, etc., these conditions will directly affect the service life and processing efficiency of the tool.
In summary, the material selection of the end mill should be determined according to the specific processing needs and workpiece characteristics. In practical applications, it is also necessary to combine the geometric shape of the tool, coating treatment and other factors to achieve the best processing effect.