The cutter point of the مطحنة طرفية refers to the positioning reference point of the tool installed on the cutter head of the end mill. The tool point determines the feed direction and cutting Angle of the cutting edge, which is a crucial parameter in NC programming and machining. The following is a detailed introduction to the cutter point of the end mill:
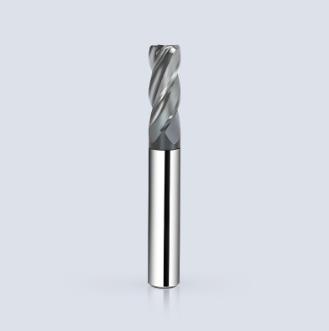
First, the definition of knife point
Basic concept: The tool point is a reference point on the tool that is used to determine the position of the tool in the workpiece coordinate system.
The cutter point of the end mill: for the end mill, the cutter point is generally taken at the intersection of the tool axis and the bottom surface of the tool, that is, the center point of the tool end face.
Second, the role of knife site
Programming benchmark: In numerical control programming, the tool point is the starting point and the end point of the tool trajectory, and the programmer prepares the tool trajectory according to the tool point.
Machining accuracy: The accuracy of the cutter point directly affects the machining accuracy. When setting the tool, it is necessary to ensure that the tool point coincides with the tool point to reduce the machining error.
Compensation adjustment: In CNC machining, tool wear, replacement and other factors will lead to changes in the tool point. Through the tool compensation function, the position of the tool point can be adjusted to ensure the machining accuracy.
Third, the choice of knife site
Processing requirements: According to different processing requirements, different cutting points can be selected. For example, when roughing, the front tool position (the position of the tool closest to the spindle) can be selected to obtain a large cutting force and cutting depth; When finishing, you can choose the back tool position (the position where the tool is farthest from the spindle) to obtain a smaller cutting force and cutting depth, and improve the machining accuracy.
Material characteristics: The hardness and shape of the machined material will also affect the choice of cutter site. For harder materials, the back tool position should be selected for processing to reduce the cutting force; For softer materials, the front tool position can be selected for machining.
Machine tool performance: The performance and accuracy of the machine tool also affect the selection of the tool point. On high-precision CNC machine tools, the tool position can be adjusted precisely by the tool compensation function to obtain higher machining accuracy.
Fourth, the application of knife site
Tool operation: Before CNC machining, it is necessary to operate the tool so that the tool point overlaps with the tool point. The selection of cutter points should be easy to measure and program to improve machining accuracy and efficiency.
Tool compensation: In the process of CNC machining, factors such as tool wear and replacement can lead to changes in the tool point. Through the tool compensation function, the position of the tool point can be adjusted to ensure the machining accuracy.
Machining monitoring: In the process of CNC machining, the position of the tool point can be monitored to find the tool wear, fracture and other problems in time, and take appropriate measures to deal with it.
Fifth, summary
The cutter point of end mill is a very important parameter in NC programming and machining. It determines the feed direction and cutting Angle of the cutting edge, which directly affects the machining accuracy and efficiency. In practical applications, it is necessary to select the appropriate tool point according to the processing requirements, material characteristics and machine tool performance and other factors, and ensure the machining accuracy and efficiency through the tool operation and tool compensation function.