With the rapid development of 5G communications, IoT, and consumer electronics, precision machining of electronic components has entered the micron-level era. From miniature sensors in smartphones to precision connectors in spacecraft, machining accuracy requirements are increasing at an annual rate of 15%. This article systematically analyzes how 0.01-3mm diameter hard alloy end mills are driving technological transformation in micro-precision machining through material innovation, structural optimization, and process advancements.
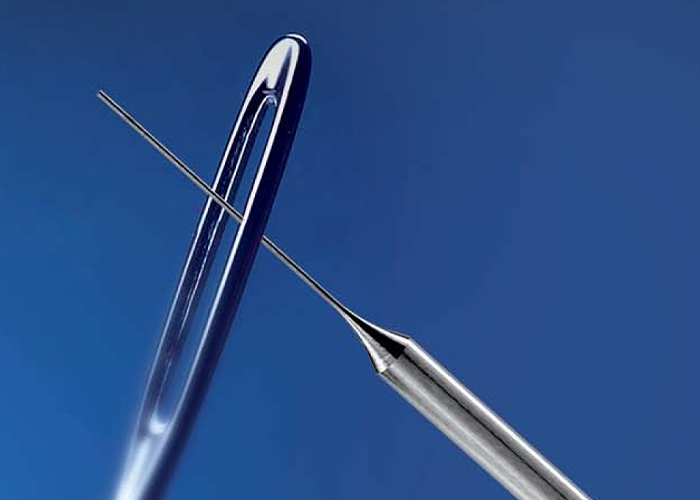
Challenges in Ultra-Precision Machining for Electronics Manufacturing
Modern electronic components exhibit three key technical characteristics: miniaturized structures, complex irregular surfaces, and an increasing proportion of difficult-to-machine materials. For example, Type-C connectors require ±2μm accuracy for their 24° trapezoidal teeth, while the wall thickness of micro control unit (MCU) carriers is generally ≤0.15mm. In terms of materials, challenging substrates like ceramic and titanium-copper alloys now account for over 35% of high-end electronic components.
Traditional 0.8-2mm high-speed steel end mills face fundamental limitations:
- Cutting speeds are capped at 200-300 m/min, insufficient for high-efficiency production.
- Radial deviation reaches 0.03mm when length-to-diameter ratios exceed 5:1.
- Tool life is limited to 7-9 pieces when machining hard materials like SK7 spring plates.
As Li Xueguang, R&D lead at China Minmetals, notes: “China long depended on foreign suppliers for 0.01-0.04mm micro end mills, which constrained domestic production capabilities for precision electronics.”
Key Breakthroughs in Tool Design Innovation
Material Technology Advancements
Modern micro end mills utilize ultra-fine grain (0.3μm) hard alloy substrates. The WCP20 formulation increases flexural strength to 4,800 MPa—a 40% improvement over conventional materials. Jinzhou Company’s 0.01mm micro-end mill employs WC-Co hard alloy with 0.2-0.5μm grains, achieving six precision-ground surfaces on a tool just 1/8 the diameter of a human hair.
In coating technology, a four-layer alternating TiAlN/DLC nanocomposite reduces friction coefficients to 0.12 (60% lower than traditional coatings). Research by International Metalworking News confirms that PVD TiAlN or CVD diamond coatings (1-3μm thick) significantly enhance wear resistance and thermal stability. These advancements extend PCB micro-hole machining life to 12,000 holes while achieving Ra0.05 surface finishes for medical micro-implants.
Geometric Structure Innovations
An asymmetric helix design (35° cutting edge + 45° chip evacuation) reduces vibration amplitude by 82% and improves thin-wall aluminum part flatness to 0.01mm/m. Tencent Cloud Developer Community highlights how tapered shanks and cylindrical tool holders enhance rigidity, while parabolic flute geometry (1.5:1 depth-to-width ratio) triples chip evacuation efficiency for composites.
Tool configurations for diverse needs:
- Solid carbide end mills: 0.1-2mm diameter, two-flute design for high-precision micro-machining
- Indexable mini end mills: 10-20mm diameter, combining carbide inserts with vibration-damping toolholders
- Mirror-finishing tools: 2μm ball-nose radius accuracy, 0.010mm corner radius precision
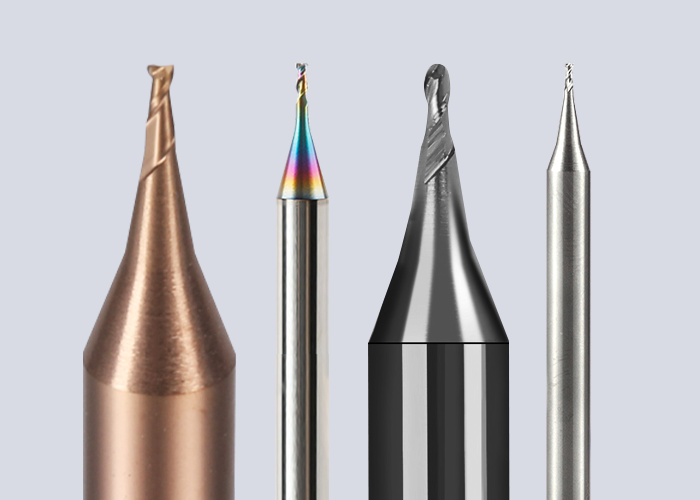
Technical Analysis of Key Applications
5G Micro-Antenna Array Machining
Using φ0.4mm ball-nose end mills at 45,000 RPM with 0.03mm depth of cut achieves <2μm contour error and Ra0.1 surface finish. HSK25-E shrink-fit toolholders with ≤1μm radial runout are critical. International Metalworking News emphasizes recalculating cutting speeds based on actual working diameter—e.g., a 0.5mm ball-nose mill at 0.05mm cut depth effectively operates at 0.3mm diameter.
IC Substrate Dicing
For 0.2mm-thick aluminum nitride ceramic, two-flute square end mills with anti-vibration grooves and PCD hybrid edges reduce edge chipping from 19% to 0.5%. DJTEC Corporation research shows precision-ground H-grade inserts (±0.005mm diameter tolerance) maintain 0.004mm contour accuracy through 800 cutting cycles.
Industry Performance Data & Future Trends
Comparative data demonstrates significant efficiency gains:
- FPC flexible circuit micro-holes: 58% faster (148 → 62 seconds/part)
- Micro-motor shafts: 400% longer tool life (2 changes/shift → 12h continuous operation)
- RF connectors: 67% fewer steps (eliminating 3 finishing grind stages)
China Minmetals’ 0.01mm end mill can engrave 56 Chinese characters on a rice grain or 7 letters on a hair strand—earning it the moniker “the most exquisite industrial teeth.” These tools are accelerating advancements in electronics, bioengineering, and beyond.
Future development priorities:
- Diameter limits: Progressing from 0.1-2mm to 0.01-0.1mm
- Smart tool systems: Integrating cutting force sensors and adaptive controls
- Hybrid processes: Combining micro-milling with laser machining
- Green manufacturing: Cobalt-free binders and eco-friendly coatings
As Chinese manufacturing ascends the value chain, breakthroughs in micro hard alloy end mills will continue empowering precision electronics—providing critical support for 5G, AI, and other next-gen industries.