When choosing an مطحنة طرفية, you need to pay attention to the following key things to ensure that you choose the tool that best suits your machining needs:
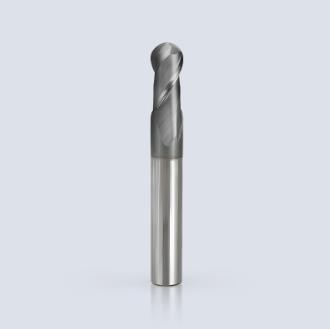
First, clear processing needs
Workpiece material:
Understand the basic material, characteristics, hardness, etc. of the workpiece being cut. Different materials have different requirements for tool materials, coatings, geometric shapes, etc.
Machining accuracy and surface roughness:
Select suitable tool accuracy and surface roughness according to machining requirements. High-precision machining requires the selection of high-precision tools, and for the workpiece with surface roughness requirements, the appropriate cutting edge and coating should be selected.
Cutting depth and shape:
Determine the depth of the cut and select the shortest length end mill that can be cut to increase the stability of the tool.
According to the shape of the workpiece (such as deep groove surface, rounded corner modeling, etc.) choose the appropriate end mill neck shape (such as standard, long neck, cone neck). Long neck and cone neck are suitable for deep digging. Cone neck end mill has high rigidity and can achieve better machining accuracy.
Second, choose the right tool material
High Speed Steel (HSS) :
Suitable for older, slower or less rigid machines, as well as one-off or very short-term production.
Cheap, not breakable, can tolerate unstable processing conditions.
Cemented carbide:
Preferred in CNC machines requiring higher speeds, fewer tool changes and higher productivity.
Long tool life, suitable for mass production.
Third, consider the number of grooves and chip removal slots
Number of grooves:
A smaller number of grooves (e.g. 2-3) provide more grooves space for long chip materials such as aluminum.
More chute slots reduce chute space but increase productivity for shorter chute materials such as medium to high carbon steel and iron.
Chute:
Proper chip removal is important because re-cutting chips can result in a significant reduction in tool life.
Fourth, pay attention to the end geometry
Choosing the right face milling cutter geometry is critical to the tool’s success. Pay close attention to the material and cutting parameters recommended by the manufacturer for a given tool.
Fifth, consider the tool coating
The coating helps reduce friction and protects the carbide from the heat generated during cutting.
Select the type of tool coating according to the type and hardness of the workpiece processed. For example, when processing the workpiece with hardness below HRC40 such as carbon steel, BWTiALN coating can be selected; When processing alloy steel S, tool steel and other parts with hardness of HRC50 or so, NanoTiAlN coating can be selected; When machining higher hardness workpieces, special coatings for high hardness processing can be selected.
Sixth, evaluate tool life and cost
Not cheaper is better. For high volumes and heavy workloads, it’s critical to invest in the right tools that can keep up with the workload.
Choosing cheap or unsuitable tools costs time and money due to material waste, scrap, tool waste, and increased wear and tear on CNC machines.
Seventh, other precautions
Tool diameter:
The requirements of the workpiece processing size should be considered, and the power required by the tool should be ensured within the rated power range of the machine tool.
Small diameter end mills need to consider whether the highest revolution of the machine tool can reach the lowest cutting speed of the tool.
Tool teeth:
The number of teeth determines the number of teeth involved in cutting at the same time during milling, affecting the smoothness of the cutting and the requirements for the cutting rate of the machine.
Coarse tooth milling cutter is mostly used for roughing, dense tooth milling cutter is suitable for finishing.
Left and right rotation:
Right-handed milling cutters are more commonly used in manufacturing and are suitable for most machining scenarios.
Left-handed milling cutter has certain advantages in high-precision machining, which can avoid the phenomenon of white cutting edge and skip cutting edge of workpiece.
To sum up, when purchasing end milling cutters, processing needs, tool materials, the number of grooves and chip removal slots, end geometry, tool coating, tool life and cost should be considered comprehensively to ensure the selection of the most suitable tool for processing needs.