I. Challenges in Engine Connecting Rod Machining and Innovative Tooling Solutions
1、Importance and Industry Background of Connecting Rod Machining Connecting rods, as core components of internal combustion engines, perform the critical function of converting piston reciprocating motion into crankshaft rotational motion. In automotive manufacturing, construction machinery, and aircraft engines, the machining precision of connecting rods directly impacts engine performance and service life. Statistics show approximately 15% of engine failures relate to connecting rod quality issues, with insufficient machining accuracy being a primary cause.
42CrMo alloy steel, a common high-strength connecting rod material, presents significant machining challenges with its HRC28-35 hardness range. Particularly in φ9mm counterbore machining at bolt connection outlets, conventional tools often suffer from short tool life and instability, leading to high production costs.
2、Why Choose Custom Tools? SDFTools’ Professional Value from Customer Pain Points In precision machining, standard tools often fail to meet special working condition requirements. A prominent automotive parts manufacturer faced severe challenges machining 42CrMo connecting rod bolt holes: standard tools lasted only 500-800 pieces with unstable performance, causing high production costs. This exemplifies where SDFTools’ custom tooling services deliver exceptional value.
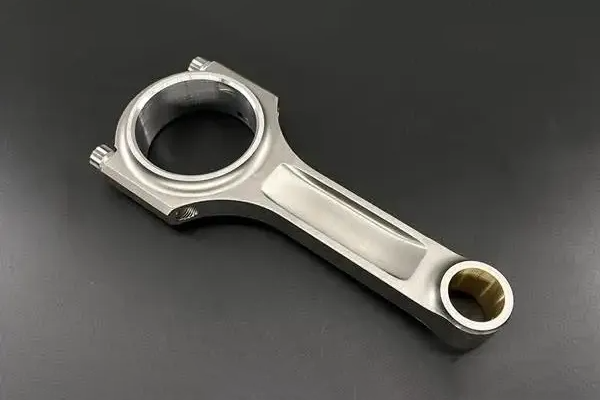
II. Real Machining Challenges Faced by Customers
1、Machining Requirements:
- Material hardness: HRC28-35 high-strength alloy steel
- Machining depth: 10mm (length-diameter ratio >1:1)
- Machining position: Oblique surface plunge milling
- Tool life requirement: Stable performance for 800+ pieces
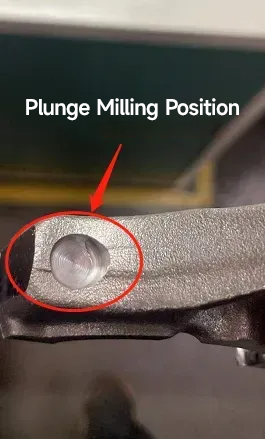
2、Key Issues:
- Vibration and tool deflection: Long interference length in oblique surface plunge milling with slender extension rods caused severe vibration (0.05-0.1mm diameter deviation)
- Dimensional inaccuracy: ±0.05mm bore diameter variation
- Rapid tool wear: Resulting in worse deflection, unstable centering, oversized holes, and breakage (500-800 pieces average tool life with 8% rejection rate)
- Unstable surface quality: Ra 0.8-1.6μm variation
- Cost control: Unstable tool life increased per-piece cost by 30%, causing $50,000+ annual losses
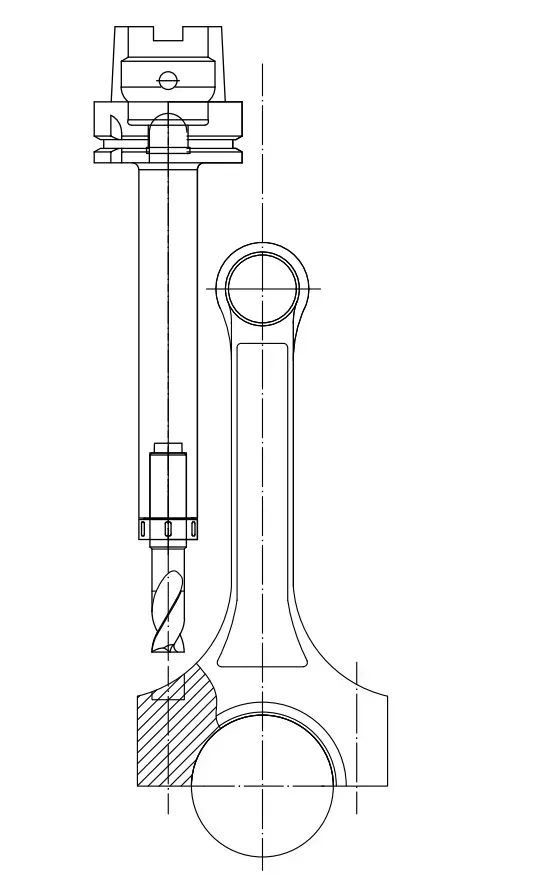
III. SDFTools Custom Solution Implementation
1、Comprehensive On-Site Diagnosis Our engineering team conducted 2-day evaluations:
- Vibration analyzer data collection
- Existing tool wear pattern analysis
- 50 machined hole measurements
- Complete machining parameter documentation
2、 Targeted Customized Solutions
Based on diagnostic results, we provide exclusive solutions:
Customer Needs AnalysisThrough in-depth interviews, data collection, and scenario-based research, we identify specific pain points in material processing (e.g., short tool life, insufficient machining accuracy) and quantify performance indicator requirements.
Material Characteristics StudyAnalyze the physical and chemical properties of the materials to be processed (e.g., hardness, thermal conductivity, wear resistance) to provide a scientific basis for subsequent tool design. For example, thermal deformation coefficients must be considered for high-temperature alloys.
Machining Condition SimulationUse digital twin technology to simulate actual machining environments (e.g., cutting speed, cooling conditions), predict potential tool wear patterns, and optimize design directions.
Tool Structure DesignCustomize tool geometric parameters (e.g., rake angle, cutting edge reinforcement) based on prior research, and optimize stress distribution through finite element analysis to enhance structural stability.
Special Coating DevelopmentDevelop functional coatings (e.g., TiAlN multilayer composite coatings) using PVD/CVD processes to improve high-temperature resistance, anti-adhesion properties, etc. Coating thickness and composition are adjusted according to working conditions.
Trial Machining VerificationTest the actual performance of tools in small-batch production, collecting data such as cutting force and surface roughness, and compare with simulation results for validation.
Parameter OptimizationFine-tune cutting parameters (e.g., feed rate, spindle speed) or coating processes based on trial machining feedback to ensure performance meets standards. For example, adjusting coating deposition temperature to improve adhesion.
Batch ApplicationAfter completing full-process verification, scale up production and provide continuous monitoring services, dynamically optimizing solutions according to changes in the customer’s production line.
Question: Translate into English, paying attention to the translation of professional terms. Do not alter the original text—translate it as is.
3、SDFTools Innovative Cutting Tool Design Solutions
3.1 Patented Edge Treatment Technology
The tool groove profile is specially designed, and the cutting edge adopts SDFTools’ latest processing technology. This ensures edge sharpness while effectively protecting the edge and guaranteeing consistency across all tool edges, thereby improving operational stability during tool use.
- Optimized edge geometry
- Multi-layer gradient hardness treatment (surface hardness up to HV3200)
- Nano-level edge honing (R0.02mm)
3.2 Enhanced Tool Structure
The tool core thickness is increased to enhance overall rigidity while maintaining smooth chip evacuation.
- Core thickness increased by 30%, bending stiffness improved by 45%
- Asymmetric helical flute design, chip evacuation efficiency increased by 60%
- Customized extension shank connection structure, vibration reduced by 70%
3.3 High-Performance Material Composition
Specialized selection of tool substrate materials and coatings ensures more stable tool lifespan.
- Substrate: Ultra-fine grain carbide (grain size 0.5μm)
- Coating: AlTiN+MoS2 composite coating, friction coefficient reduced to 0.3
- Heat treatment: Multi-stage temperature-controlled sintering process, residual stress <50MPa
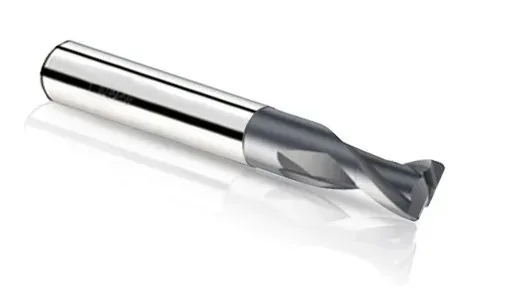
IV. Solution Performance Benefits
Metric | Conventional | SDFTools Custom | Improvement |
---|---|---|---|
Tool Life | 650 pieces | 1200 pieces | +85% |
Accuracy | ±0.05mm | ±0.01mm | 5x better |
Surface Finish | Ra0.8 | Ra0.4 | 50% smoother |
Customer Benefits:
- $58,000 annual tooling cost savings
- 300 fewer downtime hours/year
- Quality rate improved from 92% to 99.5%
- Earned “Premium Supplier” certification
V. Core Advantages of SDFTools Customization Services
- Professional Diagnostic Capabilities:
- Analysis team with 15 years of tool customization experience
- Equipped with imported inspection equipment (ZEISS microscopes, etc.)
- Established machining database covering 200+ materials
- Rapid Response Mechanism:
- Preliminary solution provided within 72 hours
- First prototype completed in 15 days
- Batch delivery achieved in 30 days
- Continuous Optimization Services:
- Regular tool health inspections
- Dynamic adjustment of machining parameters
- Quarterly technical follow-ups
VI. Does Your Business Need Custom Tools?
Consider our services when you need:
✓ Special material machining
✓ Strict surface quality requirements
✓ Standard tool life issues
✓ Vibration/tool deflection problems
✓ Per-piece cost reduction
Contact Now:
🌐 Website: https://sdftools.com/contacts/
📧 WhatsApp: +65 89420188
Why Industry Leaders Choose SDFTools?
“We don’t cost more than standard tools—we make your total machining costs lower!” — SDFTools Technical Director
Through this real case, you can see how SDFTools customized cutting tools create remarkable value for customers. With 200+ successful cases in our portfolio, we stand ready to provide professional solutions for your specialized machining needs.
http://wish-club.ru/forums/index.php?autocom=gallery&req=si&img=5233