Introduction: Limitations of Traditional Processes and Innovative Breakthroughs
In traditional internal thread machining processes, it is usually necessary to first drill a pilot hole with a drill bit and then switch to a tap or thread milling cutter for thread machining. This step-by-step approach not only increases tool management costs (such as the preparation and replacement of tool holders and collets) but also limits productivity improvements, especially in high-volume production. To overcome this bottleneck, SDFTools developed the Thread Drilling and Milling Cutter after successfully launching the drill-tap combination tool. This innovative tool integrates drilling, chamfering, and thread milling functions into one, significantly improving machining efficiency and reducing production costs.
As a company specializing in the development of high-performance cutting tools for challenging applications, SDFTools is committed to optimizing tool performance, enhancing machining efficiency, extending tool life, and reducing part rejection risks. We not only provide high-performance tools but also offer professional integrated machining solutions tailored to customer needs, helping them achieve more efficient and stable production.
I. Customer Case Background and Demand Analysis
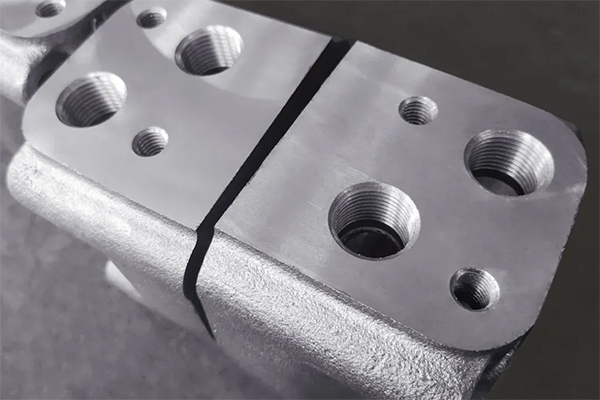
1. Part Information
- Part Name: Valve Body
- Material: QT700 (high-strength ductile iron, prone to wear during machining)
- Machine Tool: Vertical Machining Center
- Cooling Method: External Cooling
- Machining Area: 2x G1/2 threaded holes on the end face (requiring pilot hole drilling, chamfering, and threading)
- Life Requirement: 8,000 holes
2. Customer’s Original Process and Pain Points
The customer originally used a step drill + thread milling cutter for a two-step machining process:
- First, drill the pilot hole with a step drill.
- Then, switch to a thread milling cutter for threading.
Main Issues:
- Low Efficiency: Increased tool change and adjustment time, affecting batch production cycle.
- Complex Tool Management: Multiple tool holders and collets required, increasing management costs.
- Uneven Load: The drilling edges participated in threading, causing excessive cutting force and reducing tool life.
II. Innovative Optimization of SDFTools Thread Drilling and Milling Cutter
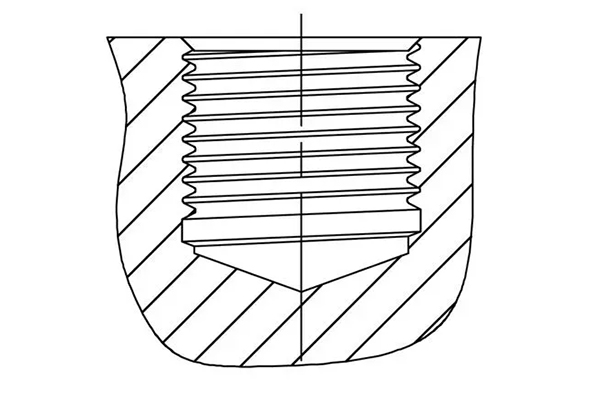
1. Description of Machining Challenges
The customer originally used a step drill for pilot holes and a thread milling cutter for threading. To further improve efficiency, a single tool capable of machining the pilot hole, chamfering, and threading was needed. However, when combining the two functions into one tool, the drilling edges would also engage during thread milling, resulting in excessive load during threading.
2. Tool Design Highlights
To meet the customer’s demands for high efficiency, long life, and low load, SDFTools customized the Thread Drilling and Milling Cutter with the following optimizations:
- Optimized Edge Design: Special geometric angles ensure balanced cutting performance for drilling and milling, extending tool life.
- Unique Flute Structure: Enhances chip evacuation, prevents chip entanglement, and maintains tool rigidity.
- Large Core Thickness + Short Drilling Edges: Improves tool rigidity, reduces vibration, and lowers machining load.
- Increased Rake and Clearance Angles: Reduces cutting resistance and improves surface finish.
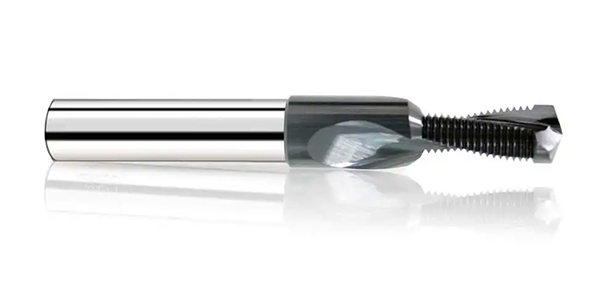
3. Advantages of Combined Machining
- Single Setup Completion: Eliminates tool change time, improving production efficiency.
- Reduced Tool Count: Only one tool is needed for pilot hole, chamfering, and threading, lowering management costs.
- Load Optimization: Structural improvements prevent excessive drilling edge engagement during milling, extending tool life.
III. Actual Machining Tests and Performance Comparison
1. Cutting Parameters
Parameter | Value |
---|---|
Tool Diameter | Φ18.85 |
Cutting Speed | 80 m/min |
Spindle Speed | 1350 rpm |
Feed Rate (Drilling) | fz 0.12 mm/tooth |
Feed Rate (Thread Milling) | fz 0.05 mm/tooth |
2. Life Comparison
Tool Type | Life (Number of Holes) |
---|---|
Original Step Drill | 8,000 |
Original Thread Milling Cutter | 8,000 |
SDFTools Thread Drilling and Milling Cutter | 10,000+ |
3. Customer Benefits
- 30%+ Efficiency Improvement: Reduced tool change time and shorter machining cycles.
- 25% Longer Tool Life: Optimized design reduces wear, lowering cost per hole.
- Enhanced Machining Stability: Reduced vibration improves thread accuracy and surface quality.
IV. Conclusion: Core Value of SDFTools Thread Drilling and Milling Cutter
SDFTools’ Thread Drilling and Milling Cutter not only resolved the customer’s efficiency bottleneck in machining QT700 valve bodies but also achieved longer tool life and more stable machining quality through combined tool design and optimized cutting performance. This solution is particularly suitable for high-volume, high-precision thread machining applications, such as automotive components, hydraulic valve bodies, and aerospace parts.
If you are seeking a more efficient and cost-effective thread machining solution, contact SDFTools today! We offer professional tool selection and process optimization support.