In CNC milling, vibrations may occur due to the limitations of cutting tools, tool holders, machines, workpieces, or fixtures, which can have an adverse impact on machining accuracy, surface quality, and machining efficiency. To reduce cutting vibration, it is necessary to consider relevant factors. The following is a comprehensive summary for your reference.
1. Poor Rigidity of Fixtures
- Evaluate the direction of the cutting forces and provide adequate support or improve the fixture.
- Reduce the depth of cut (ap) to lower the cutting forces.
- Choose sparsely toothed and uneven pitch end mills with sharper cutting edges.
- Select flute types with smaller tip radius and narrower parallel land.
- Use fine-grained uncoated inserts or thin-coated inserts.
- Avoid machining when the workpiece support is insufficient to resist the cutting forces.
2. Poor Axial Rigidity of Workpieces
- Consider using square shoulder end mills with positive rake angles (90° primary deflection angle).
- Choose inserts with L-shaped flutes.
- Decrease axial cutting forces by reducing the depth of cut, using smaller tip radii, and narrower parallel lands.
- Select uneven pitch and sparsely toothed end mills.
- Check for tool wear.
- Inspect the runout of the tool holder.
- Improve the clamping condition of the tool.
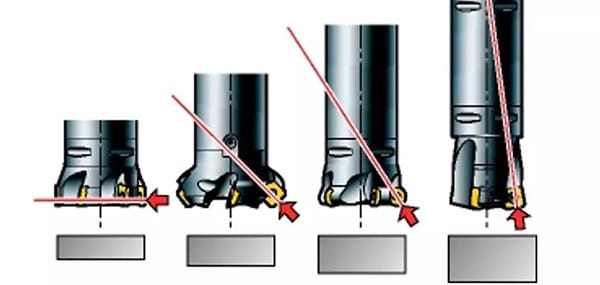
3. Excessive Tool Overhang
- Minimize overhang.
- Use uneven pitch and sparsely toothed end mills.
- Balance radial and axial cutting forces – 45° primary deflection angle, larger tip radius, or round insert end mills.
- Increase the feed per tooth.
- Use inserts with light-cutting geometries.
- Reduce the axial depth of cut (af).
- Apply climb milling during finishing operations.
- Use vibration-dampening extended adapters.
- For solid carbide end mills and indexable head mills, try using fewer teeth and/or a larger helix angle.
4. Milling Square Shoulders with a Less Rigid Spindle
- Choose the smallest possible diameter end mill.
- Select light-cutting end mills and inserts with sharp cutting edges.
- Try climb milling.
- Check the spindle runout to see if it is within the acceptable range of the machine.
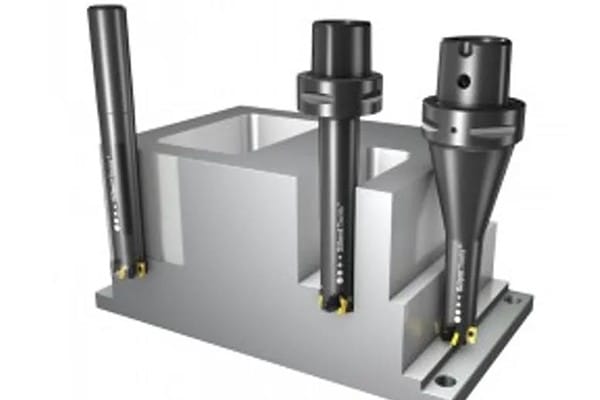
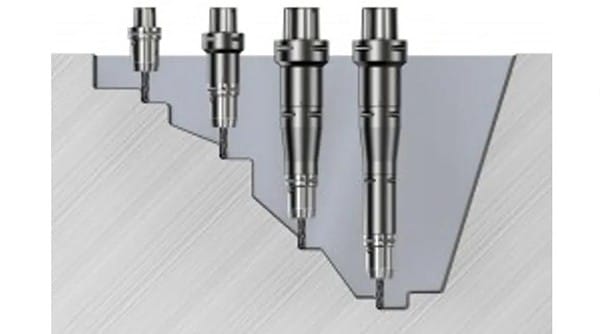
5. Unstable Table Feed
- Try climb milling.
- Tighten the machine’s feed mechanism; for CNC machines, adjust the feed screw.
- For conventional machines, adjust the locking screws or replace the ball screw.
6. Cutting Parameters
- Lower the cutting speed (vc).
- Increase the feed (fz).
- Change the depth of cut (ap).
7. Poor Stability
- Shorten the overhang.
- Enhance stability.
8. Vibration in Corners
- Use a lower feed rate with a large programmed corner radius.
Formatting Instructions:
- Headings: Use a font size of 24px for main headings (e.g., “Reducing Vibration in CNC Milling”).
- Subheadings: Use a font size of 20px for subheadings (e.g., “Poor Rigidity of Fixtures”).
- Bullets and Text: Use a font size of 16px for bullet points and regular text.
- Bold: Bold important terms or actions, such as “Evaluate the direction of the cutting forces” and “Minimize overhang”.
- Spacing: Ensure there is a line break between each section and after each bullet point for readability.
This format should make the content more visually appealing and easier to read when you copy it to a webpage. If you need further adjustments or specific CSS styles, let me know!