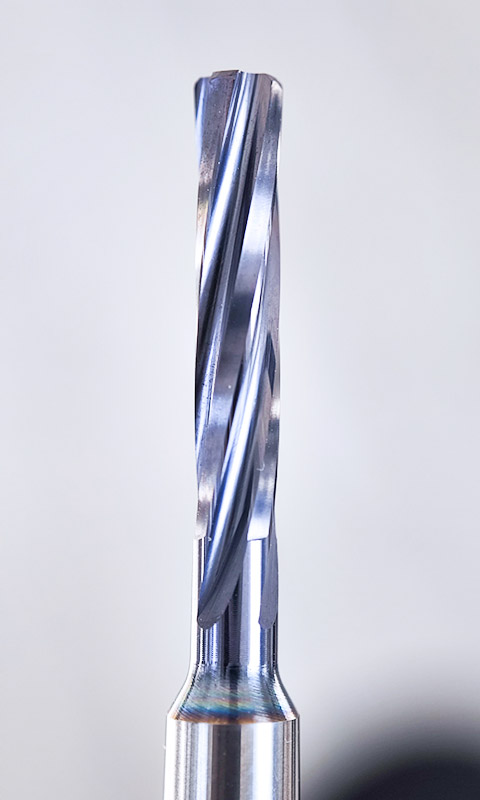
Customer Background
A globally renowned automotive parts manufacturer, Company X, has long been producing high-precision engine blocks and transmission housings. Their core process requires achieving a surface roughness of Ra0.4μm when machining Ø4.0±0.01mm diameter holes. Previously, the customer used standard reamers but faced issues such as short tool life (only 500 pieces per edge), low machining efficiency (frequent machine stops for tool changes), and occasional surface waviness, leading to high production costs.
Technical Challenges
- Harsh Machining Environment: The workpiece material is high-strength cast iron (HB220-260), generating high temperatures and abrasive wear during cutting.
- Precision and Quality Requirements: Hole diameter tolerance ±0.01mm and surface roughness Ra0.4μm must be met 100%.
- Cost and Efficiency Pressure: The original process took 2.5 minutes per piece, with high tool replacement frequency, resulting in annual loss costs exceeding $120,000.
SDFTools Customized Solution
Based on customer needs, the SDFTools team introduced the GCR-D6xID1x100-CS internal cooling reamer, integrating four core technologies:
- High-performance Material and Coating Optimization
- Material Upgrade: Using GUHRING’s GCR series ultra-hard substrate, increasing chipping resistance by 40% and doubling wear resistance compared to ordinary carbide.
- Custom Coating: Paired with a patented composite coating (AlCrN+MoS2), verified through a “Coating Information Sheet,” reducing the friction coefficient by 30%, effectively suppressing built-up edge and ensuring surface finish.
- Intelligent Internal Cooling Design
- Built-in cooling channels precisely guide coolant to the cutting edges, reducing cutting temperatures by 60% and avoiding thermal deformation-induced hole diameter deviations.
- Pre-drilling Synergy Process
- Provides a Ø3.80mm pre-drilling solution, controlling the allowance precisely at 0.1mm (0.02mm per side), reducing reaming load, minimizing tool vibration, and ensuring hole wall consistency.
- Dynamic Parameter Matching
- Recommends cutting parameters (Vc=80m/min, f=0.08mm/r) based on material characteristics, achieving an optimal balance between efficiency and tool life.
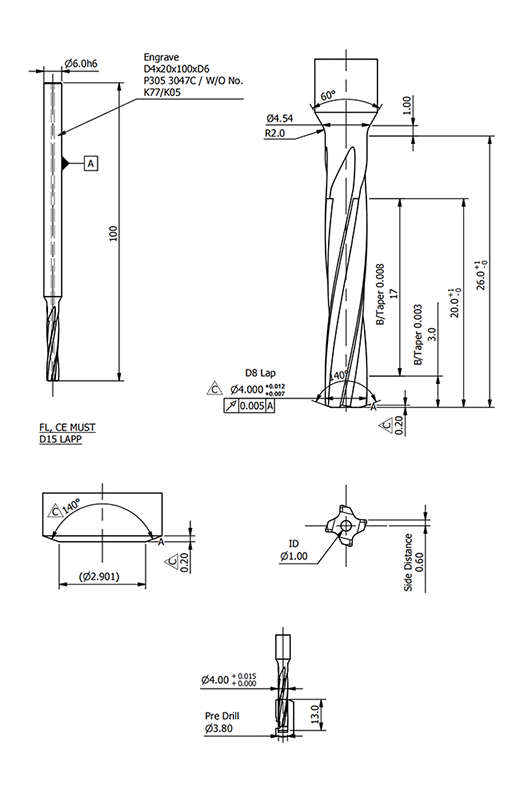
Results and Value
- Efficiency Leap: Reduced processing time per piece to 1.2 minutes, increasing production efficiency by 108%.
- Life Span Breakthrough: Single-edge processing life reaches 2000 pieces, reducing annual tool costs by over 65%.
- Zero Defects: Hole diameter qualification rate reaches 100%, with stable surface roughness of Ra0.3-0.35μm, achieving the customer’s “zero rework” goal.
- Environmental Benefits: The internal cooling system reduces coolant usage by 30%, aligning with the customer’s green manufacturing strategy.
Customer Feedback
“SDFTools’ custom reamers not only solved our technical bottlenecks but also brought significant cost reduction and efficiency improvements. From material selection to coating, from design to process support, it fully demonstrated their professional depth!”
About SDFTools
As an innovator in the field of precision tool customization, SDFTools always focuses on customer pain points, providing full-chain solutions from process analysis, tool design to production optimization. Whether in aerospace, automotive manufacturing, or medical device fields, we empower precision manufacturing with technology, helping you gain a competitive edge.
Technology-driven, precision-focused—SDFTools, your efficient machining partner.